Motor operation and maintenance, Maintenance instructions, Sealed bearings – Davey ISOSPEC CM Series ISO2858 Heavy Duty Industrial Centrifugal Pump User Manual
Page 5: Open (regreasable) bearings, Recommended lubricant
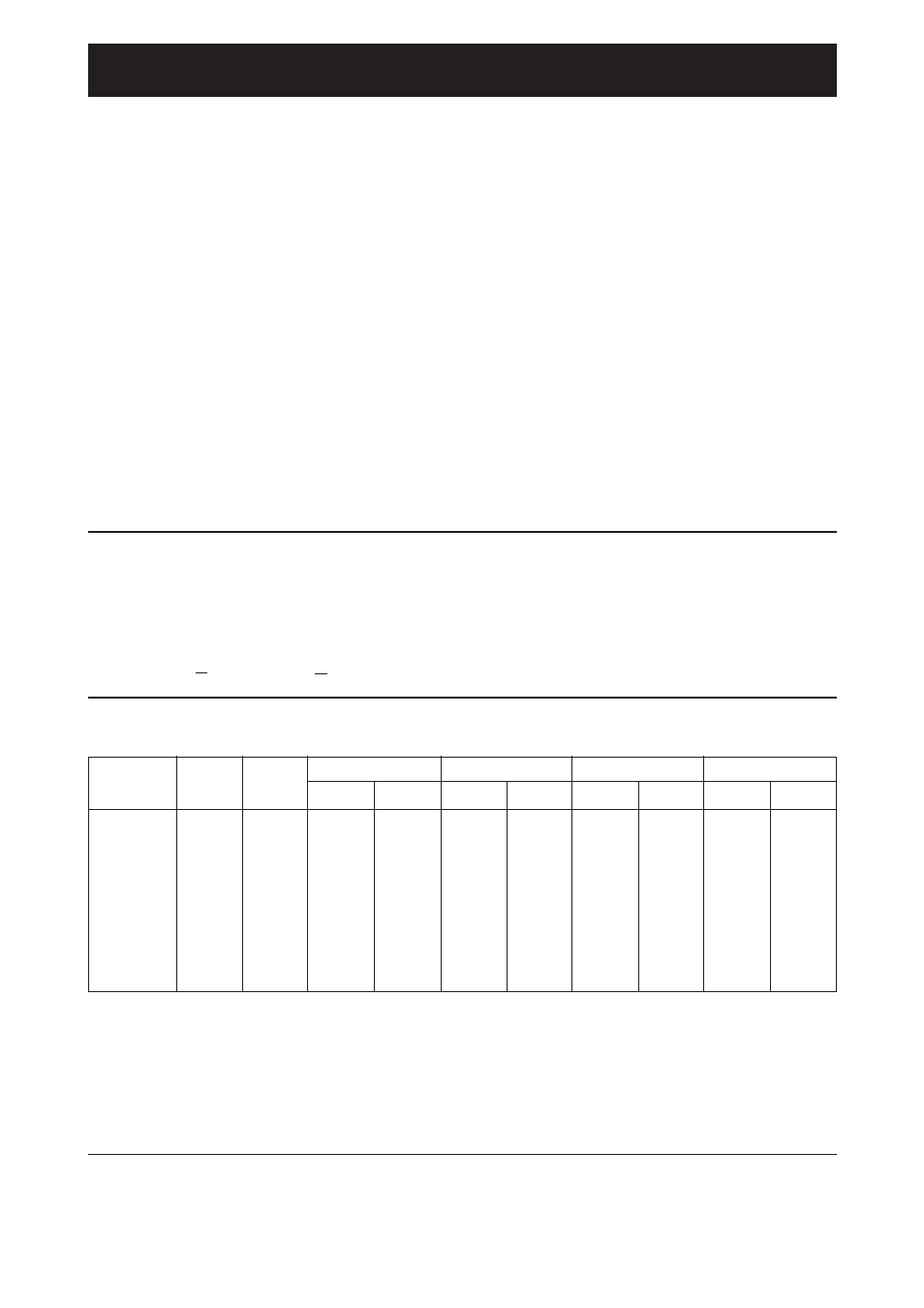
~ 5 ~
MOTOR OPERATION AND MAINTENANCE
Maintenance Instructions
The following maintenance instructions apply to all SGA
motors except for hazardous location motors. For
SGAE, SGAN and SGAD motors maintenance must
be carried out by an authorized service agent. Contact
CMG for detailed instructions.
To obtain maximum service life from your electric
motor, it is recommended the following maintenance be
implemented and recorded in a plant log book.
A. Ensure air intake space is unobstructed.
B. On a weekly basis use an air hose to ensure all
airways are clear and free of dust.
C. Do not wash the motor down unless it is IP66 rated.
D. On a quarterly basis:-
i) Check motor terminals for tightness and contact.
ii) If terminal lug/lugs are discolored, re-terminate.
iii) Check operation of starting equipment, ensuring
all terminations are tight.
iv) Check mechanical operation of thermal
overload.
v) Check mechanical operation of thermistor relay
(if fitted).
vi) Check operation of space heaters (if fitted).
E. On a six (6) monthly basis, in addition to the items in
‘D’ :-
i) Check stator resistance (compare to original and
enter in log book)
ii) Check supply voltage at motor terminals.
iii) Check bearings for noise/overheating.
F. On an annual basis, in addition to the items in ‘D’
and ‘E’ :-
i) Re-grease bearings in line with chart below.
Note: As indicated in the chart, some bearings
may require more frequent grease replacement.
ii) Strip motor down and clean thoroughly.
iii) Check bearings for wear/damage - replace as
necessary.
iv) Check all machine bolts for cracks or damage
- replace as necessary.
v) Check all holding bolts for signs of fatigue/
damage - replace as necessary.
vi) After re-assembly, check and record:-
Full Load Current
Full Load Voltages
Full Load Speed
vii) Ensure cooling fan is operational.
G. Ensure plant log book records commissioning data
and compare maintenance data with original.
Sealed Bearings
The required replacement interval for sealed bearings
is generally determined by the grease life which is
dependant on operating temperature, operating speed,
the limiting speed of the bearing and the type of grease.
Under normal operating conditions the following
relationship applies:-
n n
log t = 6.54 – 2.6 N – (0.025 – 0.012 N )T
Where:
t = Average grease life (hours)
n = Speed (RPM)
N = Bearing limiting speed with grease lubrication (RPM)
T = Operating temperature (°C)
For further information, please contact your nearest
CMG office for advice.
Open (Regreasable) Bearings
Recommended Grease Replenishment Intervals (Hours)
1)
Bearing
Qty of
3000 r/min
1500 r/min
1000 r/min
750 r/min
Bearing
bore
grease
number
[mm]
[g]
Ball
Roller
Ball
Roller
Ball
Roller
Ball
Roller
6312/NU312
60
20
3800
1900
10100
5050
16000
8000
20000
10800
6313/NU313
65
25
3400
1700
9400
4700
15100
7500
20000
10300
6314/NU314
70
30
3000
1500
8800
4400
14300
7150
19500
9750
6315/NU315
75
30
2570
1285
8200
4100
13500
6750
18500
9250
6316/NU316
80
35
2200
1100
7600
3800
12800
6400
17700
8850
6317/NU317
85
40
1800
900
7100
3550
12100
6050
16800
8400
6318/NU318
90
45
1650
825
6600
3300
11500
5750
16000
8000
6319/NU319
95
45
1500
750
5700
2850
9000
4500
14600
7300
6322/NU322
110
60
1200
600
4800
2400
8300
4150
13400
6700
1)
Based on maximum grease service life of 20,000 hours.
It should be noted that for motors fitted with Ball and Roller bearings, the lubrication intervals for both bearings should be
based on the roller bearing data.
The re-lubrication intervals recommended are calculated on the basis of normal working conditions.
Note: Air operated grease guns should
not be used.
Replenishment of grease media should be by means of a hand held grease gun whilst motor is running with relief plate
removed.
Recommended Lubricant
Use Lithium based grease such as Shell Alvania R3 unless otherwise specified. SGAH, SGASS and SGAHS require
extra high temperature grease, Magnalube G or equivalent.