Sterling ME User Manual
Page 12
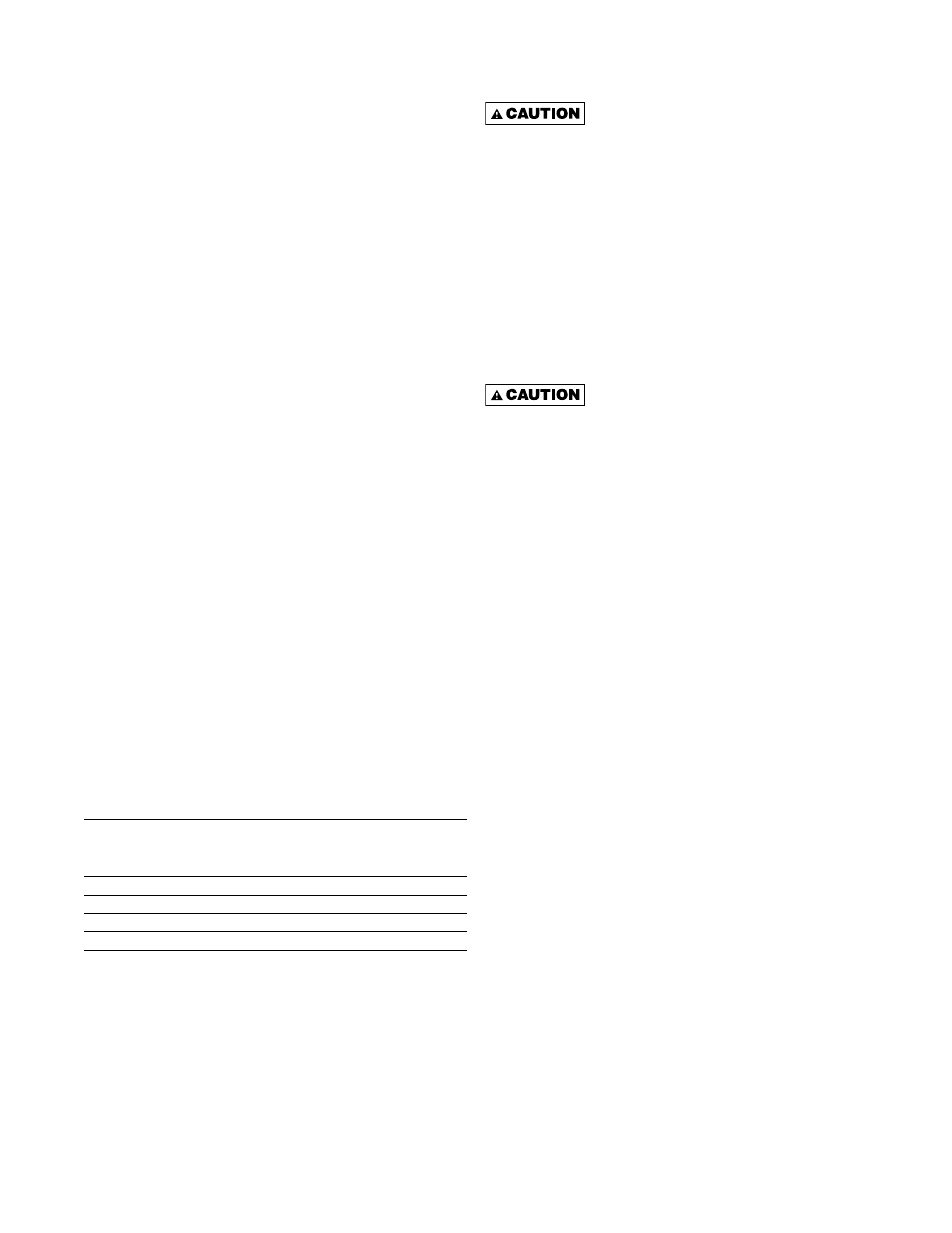
— 12 —
Three Stage Units: Dual duct furnace models: First
furnace is equipped with two stage heating; second
furnace is equipped with single stage heating but fi red
independently, giving three stages of heating.
Triple duct furnace models: Each duct furnace is
e q u i p p e d w i t h s i n g l e s t a g e h e a t i n g bu t f i r e d
independently, giving three stages. Each stage is 33% of
the unit’s full input rate. Duct furnace one will always light
fi rst and disengage last.
Four Stage Units: Dual duct furnace models only. Each
duct furnace is equipped with two stage heating but fi red
independently, giving four stages. Each stage is 25% of
the units full input rate. Duct furnace one will always light
fi rst and disengage last.
Six Stage Units: Triple duct furnace models only. Each
duct furnace is equipped with two stage heating but fi red
independently giving six stages. Each stage is 16.5% of
the units full input rate. Duct furnace one will always light
fi rst and disengage last.
Electronic Modulation Units: These units are equipped
with an electronic modulating control which provides unit
fi ring capabilities of 50 to 100% of the units full input rate.
This control is found in the gas train downstream of the
gas valve and allows main burner ignition only at the
maximum rate. A thermostat with remote setpoint
adjustment modulates the gas input.
Multi-Stage w/Electronic Modulation Units:These dual
and triple duct furnace models are equipped with an
electronic modulating control on duct furnace one and
single or two stage heating on each successive duct
furnace. Furnace one (modulated) will fi re fi rst and
disengage last. Additional stages of heat will engage
after furnace one has fi red at maximum modulation
capability for the duration of the delay setting. The
amount of modulation and each stage size depends upon
unit size and the number of stages. See following chart.
Modulation
Stage
Number
Capabilities
Size
of Stages (% of full input) (% of full input)
2
25 - 50
50
3
16.5 - 33
33
4
25 -50
25
6
16.5 - 33
16.5
AIR HANDLING REQUIREMENTS
AND ADJUSTMENTS
Remove wooden shipping support
from beneath blower housing of Blower Section (if
applicable) to prevent possible unit damage or
improper unit operation.
Static Pressure through the unit should never exceed
2.0” W.C. (0.50 kPa). Units operate at a temperature rise
range of 30 to 80°F (17 to 44°C).
NOTICE: It is important that the fi nal temperature
leaving the unit does not exceed 160° F (71°C). When
fi nal air throughput adjustments are being made, a
check of the discharge air temperature should be
made after unit has operated for 15 to 20 minutes.
A unit should never be allowed to
cycle on the primary limit for a prolonged period of
time. It is a safety control to prevent a fi re. If cycling
on the primary limit is noted, corrective measures
should be taken immediately. Failure to do so could
result in unit damage or a fi re.
NOTICE: At initial unit installation, unit should be
started momentarily to confi rm proper blower wheel
rotation as the unit will deliver some air with the
blower wheel running backwards.
Two basic air control systems can be used to deliver
conditioned air to the occupied space: intermittent or
constant fan operation.
Intermittent Fan Operation: The unit employs an air
control system which utilizes a fan time delay relay to
operate the fan while heating and the thermostat while
cooling. Refer to unit wiring diagram.
Constant Fan Operation: The unit can be wired to give
an air control system which constantly circulates air
through the unit and occupied space with constant fan
operation. Refer to unit wiring diagram.
NOTICE: Check blower belt tension. Proper belt
tension is important to the long life of the belt and
motor. Proper belt tension will allow the belt to be
depressed
1
/
2
" to
3
/
4
".
It is important that the blower motor and the blower
wheel pulleys be in good alignment, with the motor and
blower shafts parallel.
Belt tension must be adjusted to give approximately
3
/
4
" defl ection of the belt when fi nger pressure is applied
to the middle of the belt (See fi gure 12). Small changes
in this tension may be necessary for optimum operation.
Belts will stretch over a period of time, requiring an
adjustment to this tension. See MAINTENANCE section
for belt and pulley adjustments.