Gas piping – Sterling QVES User Manual
Page 16
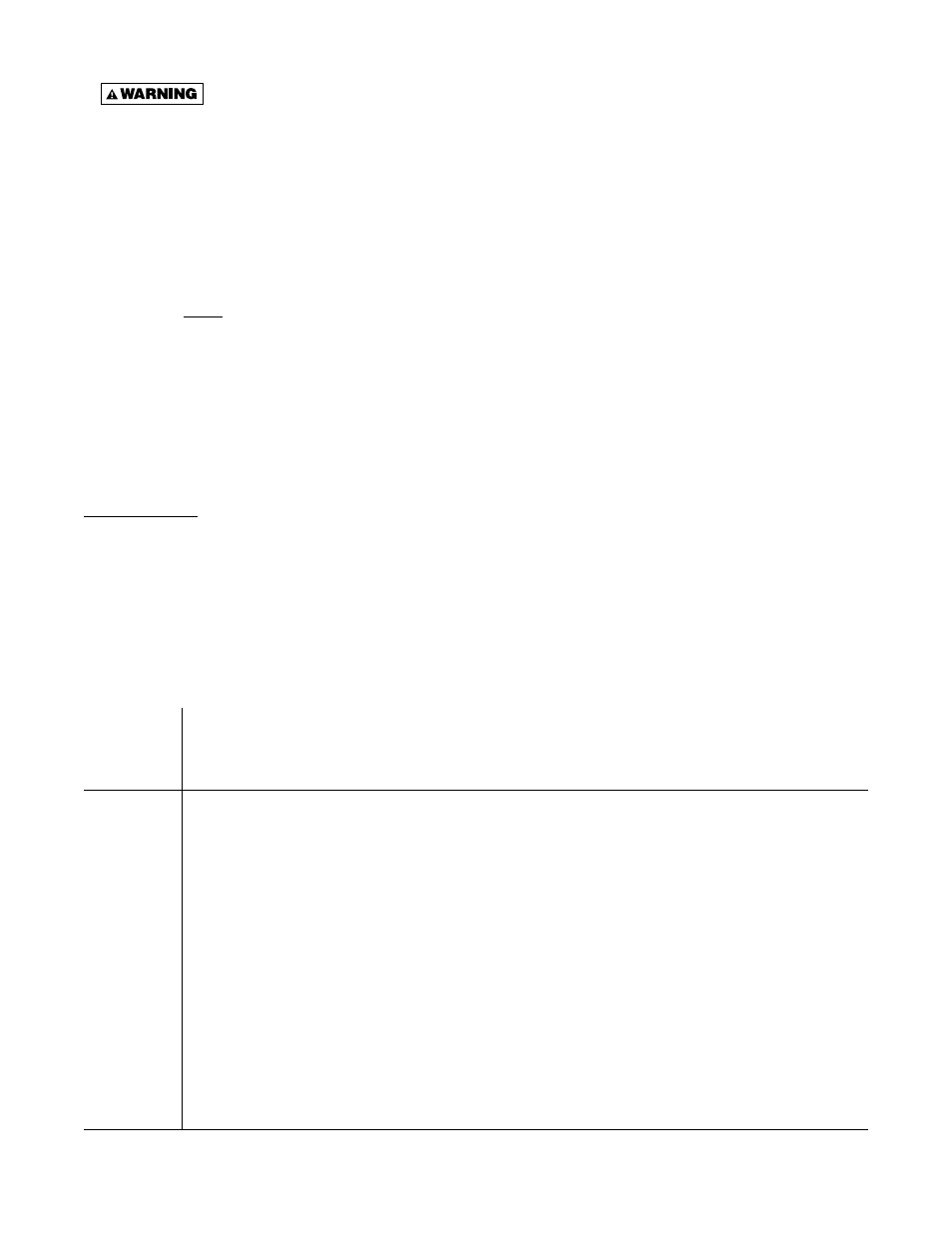
16
GAS PIPING
To avoid equipment damage or possible personal injury, do not connect gas piping
to this unit until a supply line pressure/leak test has been completed. Connecting the unit before
completing the pressure/leak test may damage the unit gas valve and result in a fi re hazard.
Do not rely on a shut off valve to isolate the unit while conducting gas pressure/leak tests. These
valves may not be completely shut off, exposing the unit gas valve to excessive pressure and damage.
PIPE SIZING
To provide adequate gas pressure at the gas duct
furnace, size the gas piping as follows:
1. Find the cu ft/hr by using the following formula:
Input
Cu ft/hr =
Btu
2. Refer to Table 5. Match “Legth of Pipe” with
appropriate “Gas Input - Cu Ft/Hr” figure. This
fi gure can then be matched to the pipe size at the
end of the column.
Example: It is determined that a 67 foot (20.4m) run of
gas pipe is required to connect a 200 MBTU gas duct
furnace to a 1,000 Btu/cu. ft (0.29 kW) natural gas supply.
200,000 Btu/hr
= 200 Cu ft/hr
1,000 Btu/cu ft
Using Table 5, a 1 inch nominal diameter pipe is needed.
NOTICE: See General Safety Information section for
english/SI (metric) unit conversion factors.
Nominal
Iron
Pipe Size
Internal
Dia.
Maximum Capacity of Pipe in Cubic Feet of Gas per Hour for Gas Pressures of 0.5 psi (3.5 kPa) or Less,
and a Pressure Drop of 0.5 Inch Water Column (124.4 Pa)
(Based on a 0.60 Specifi c Gravity Gas)
Length of Pipe, ft. (Meters)
GAS PIPE SIZE
in. in. 10 20 30 40 50
60 70 80 90 100
125
150
175
200
(mm) (3.0) (6.1) (9.1) (12.2) (15.2)
(18.3) (21.3) (24.4) (27.4) (30.5) (38.1) (45.7) (53.3) (61.0)
1/2
0.622
175
120 97 82 73
66 61 57 53 50 44 40 37 35
(16) (4.96) (3.40) (2.75) (2.32) (2.07)
(1.87) (1.73) (1.61) (1.50) (1.42) (1.25) (1.13) (1.05) (0.99)
3/4 0.824 360 250 200 170 151
138 125 118 110 103 93 84 77 72
(21) (10.2) (7.08) (5.66) (4.81) (4.28)
(3.91) (3.54) (3.34) (3.11) (2.92) (2.63) (2.38) (2.18) (2.04)
1 1.049 680 465 375 320 285
260 240 220 205 195 175 160 145 135
(27) (19.3) (13.2) (10.6) (9.06) (8.07)
(7.36) (6.80) (6.23) (5.80) (5.52) (4.96) (4.53) (4.11) (3.82)
1
1/4
1.380 1400 950 770 660 580
530 490 460 430 400 360 325 300 280
(35) (39.6) (26.9) (21.8) (18.7) (16.4)
(15.0) (13.9) (13.0) (12.2) (11.3) (10.2) (9.20) (8.50) (7.93)
1
1/2
1.610 2100
1460
1180 990 900
810 750 690 650 620 550 500 460 430
(41) (59.5) (41.3) (33.4) (28.0) (25.5)
(22.9) (21.2) (19.5) (18.4) (17.6) (15.6) (14.2) (13.0) (12.2)
2 2.067 3950 2750 2200 1900 1680
1520 1400 1300 1220 1150 1020 950 850 800
(53) (112) (77.9) (62.3) (53.8) (47.6)
(43.0) (39.6) (36.8) (34.5) (32.6) (28.9) (26.9) (24.1) (22.7)
2
1/2 2.469 6300 4350 3520 3000 2650
2400 2250 2050 1950 1850 1650 1500 1370 1280
(63) (178) (123) (99.7) (85.0) (75.0)
(68.0) (63.7) (58.0) (55.2) (52.4) (46.7) (42.5) (38.8) (36.2)
3 3.068 11000 7700 6250 5300 4750
4300 3900 3700 3450 3250 2950 2650 2450 2280
(78) (311) (218) (177) (150) (135) (122) (110) (105) (97.7) (92.0) (83.5) (75.0) (69.4) (64.6)
4 4.026 23000
15800
12800
10900 9700
8800 8100 7500 7200 6700 6000 5500 5000 4600
(102) (651) (447) (362) (309) (275)
(249) (229) (212) (204) (190) (170) (156) (142) (130)
1. Determine the required Cu. Ft. / Hr. by dividing the rated heater input by 1000. 2. FOR NATURAL GAS: Select the pipe size directly from
the table. 3. FOR PROPANE GAS: Multiply the Cu. Ft. / Hr. value by 0.633; then use the table. 4. Refer to the metric conversion factors
listed in General Safety section for SI unit measurements/conversions.
Table 5
NOTICE: If more than one gas duct furnace is to be
served by the same piping arrangement, the total cu
ft/hr input and length of pipe must be considered.
NOTICE: If the gas duct furnace is to be fi red with LP
gas, see below and consult the local LP gas dealer
for pipe size information.
NOTICE: HEATER INSTALLATION FOR USE WITH
PROPANE (BOTTLED) GAS MUST BE MADE BY A
QUALIFIED L.P. GAS DEALER OR INSTALLER. HE
WILL INSURE THAT PROPER JOINT COMPOUNDS
ARE USED FOR MAKING PIPE CONNECTIONS; THAT
AIR IS PURGED FROM LINES; THAT A THOROUGH
TEST IS MADE FOR LEAKS BEFORE OPERATING
HEATER; AND THAT IT IS PROPERLY CONNECTED
TO PROPANE GAS SUPPLY SYSTEM.
Before any connection is made to an existing line
supplying other gas appliances, contact the local gas
company to make certain that the existing line is of
adequate size to handle the combined load.