Introduction, The.rapid.master, The.servo.feed./.rapid.master.feed.system – Rapid-Air SERVO FEED / RAPID MASTER User Manual
Page 3
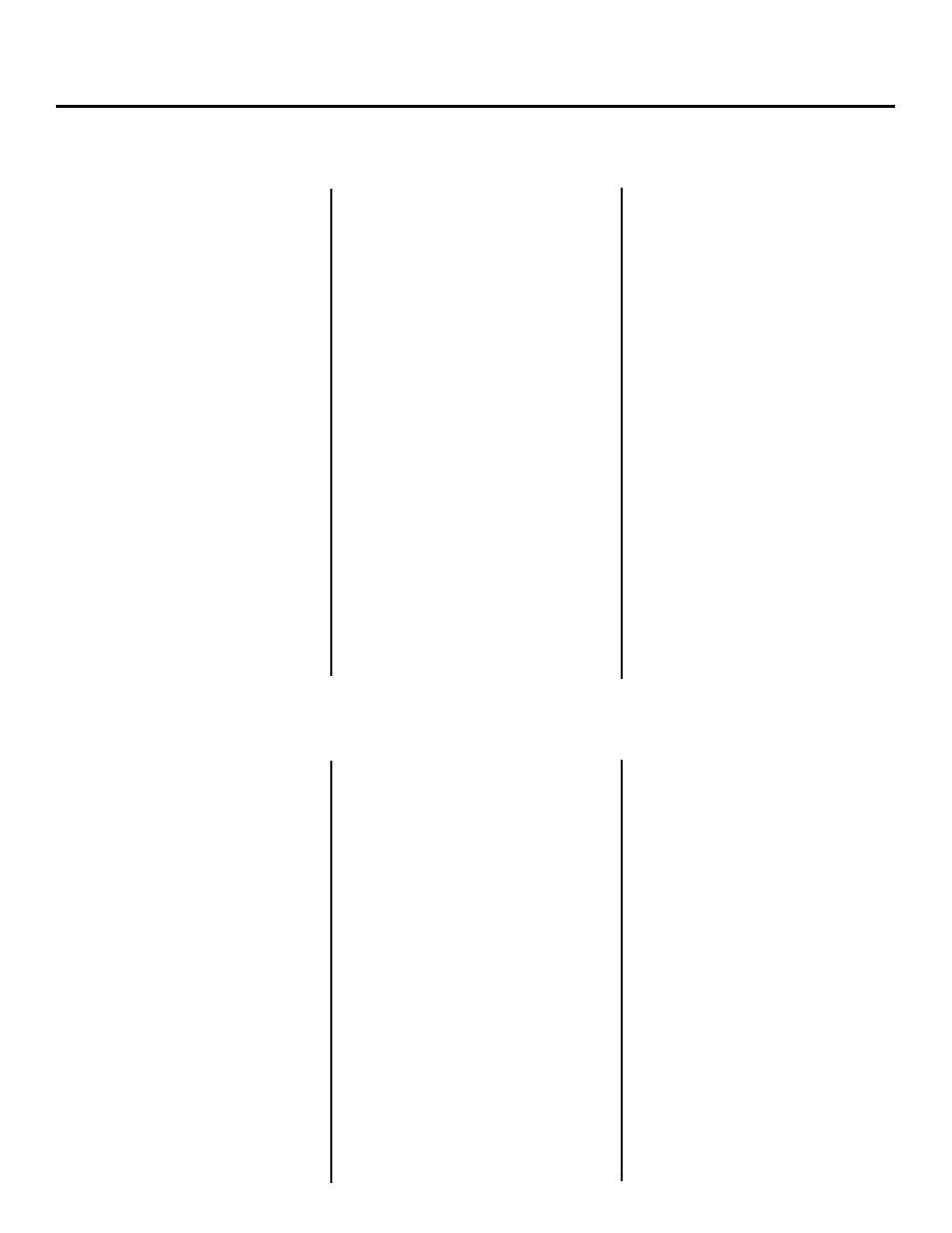
The Rapid Master that you have just re-
ceived is fully assembled and ready to
be put into production. Due to shipment
vibration and handling, the machine
should be checked to ensure all screws
and bolts are tight. Remove the cover
to the electrical controls and visually
inspect that all parts are in place and
secure. If the machine was damaged
in shipment, contact the carrier first to
report the damage and then Rapid-Air.
CAUTION:
THE RAPID MASTER MACHINE IS TOP
HEAVY WHEN NOT SITTING ON ITS
BASE LEGS. USE EXTREME CAUTION
WHEN MOVING THIS MACHINE!
Install machine on a level surface
with sufficient clearance for loading
and unloading process material. The
machine should be secured to the floor
through the four holes provided in the
feet of the machine using 7/16 tie-down
bolts. Or, can be installed using 1/2-13
introduction
The.Rapid.Master
In order to maximize your learning
time and troubleshoot any interface
problems, we would like to request that
the following items be complete before
calling us:
1. Servo unit should be completely
installed and aligned to a die on
the press.
2. 220 Vac electrical wiring, if required,
should be in place and unit
turned on.
3. Air should be connected
and ready to be used.
4. All servo interface questions
should be directed to Rapid-Air prior
to a start-up visit. Please call
815-397-2578 and ask to have
these questions directed to the
proper personnel.
leveling bolts and machine pads. The
pads keep the machine from walking
during operation and also act as a noise
reduction device.
The machine has two other require-
ments that need attention before put-
ting the Rapid Master into production.
1) The customer must provide
minimum CFM Air, at 75 to 120 PSI
of clean, dry, lightly lubed air to the
machine. Connect a minimum of
5/8” ID hose into the filter regulator
provided on the machine. The inlet
to the FRL is a NPT female thread.
2) The customer must provide
120 volt, 20 amp, 60 cycle
electrical power. If an extension
cord is used between the source
and the machine, it should be a
minimum 12 gauge wire to keep the
voltage loss down and for electrical
safety reasons.
The Rapid-Air Servo / Rapid Master
Feed system carries with it the quality
and reliability you have grown to expect
from a Rapid-Air product. The motion
control system is a programmable
industrial computer and this advanced
technology, combined with a highly
engineered precision roll feed, is
an unchallenged combination in the
press industry.
The compact mechanical package,
direct coupled with a brushless servo
drive motor, offers response and feed
speed accuracy unparalleled in any
other powered roll feed. Operator
interface is so simplified, a typical
setup person can have the servo feed
programmed and running in a mat-
ter of minutes. A step-by-step prompt
appears on a four line 88-character
The.Servo.Feed./.Rapid.Master.Feed.System
operator to jog the servo feed forward
or reverse at a slow rate. The operator
can select jog to length or jog continu-
ous to aid in threading up material.
The Rapid-Air Servo Roll Feed has been
designed to mount on a free-standing
table as close as possible to the press
The precision mechanical roll feed unit
has been designed for compactness,
ease of setup and installation. Three
cables with twist lock connectors, two
cables for the servo, one connected to
the cutter, and one air line are the only
external connections required. The
electrical controls are housed in a small
cabinet which should be mounted close
to the press working area. The operator
keypad and display are mounted on top
of the control cabinet.
display, which asks simple questions of
the operator. Entry of feed length, cutter
dwell time, and % maximum speed are
all that is required for a new setup.
Routine jobs can be stored, recalled,
changed and saved or run with a simple
2 digit job number entry. Up to 99 jobs
may be stored and recalled at will.
A resolver, direct coupled to the servo
drive motor for precise digital position
feedback, enable roll positioning
accuracy to +/- .0025 for any
programmed feed length or speed.
Operator programmed feed length, up
to 999.999 inches and % max speed
selection along with full jog features
on a pendant unit, allow the operator
to thread the material and inch it into
position. The inch feature enables the