C-400 – Pacific Laser Equipment C-400 User Manual
Page 5
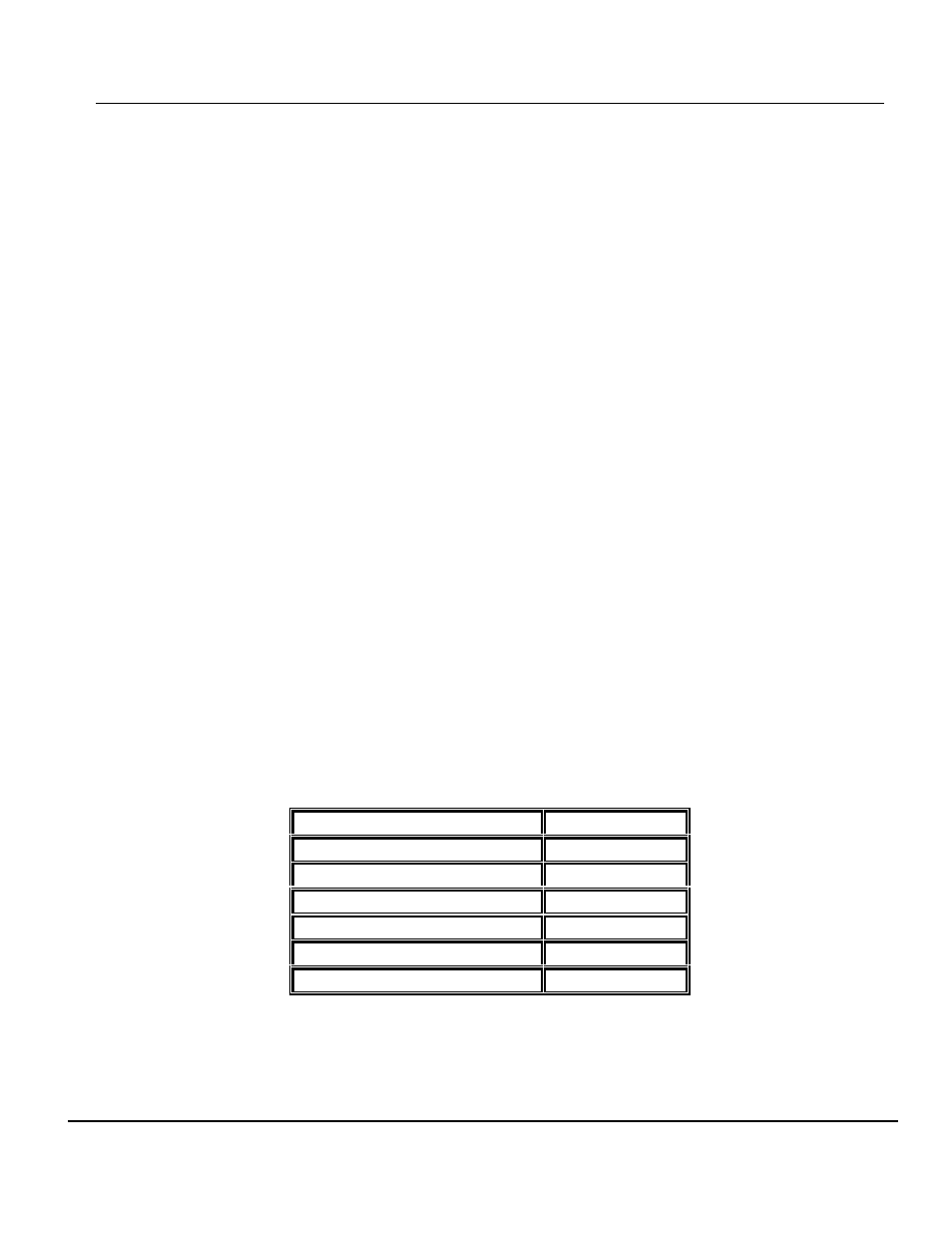
Motor controller 4ch
User manual
C-400
November 19, 2002
Release: 1.30
2002 by
Pacific Laser Equipment
PLEquipment, 3941 S. Bristol St. Unit D-122, Santa Ana, CA. 92704,
(
509-355-5155, Fax: 509-355-5155, Email: [email protected]
Page 5 of 21
Multi-Axis Control
The axis number will proceed whenever a specific axis needs to be moved or read.
Example: 1MR50000, 2MR-30000, 3TP, 4GH.
Default Values
C-400
©
has been designed to be as easy to use as possible. When shipped, the C-400
©
comes with
(factory) default settings. These settings can be read and changed using the Read_C400.vi and the
SET_C400.vi In most cases, the factory default values will be appropriate for the application.
Limit Sensors
During operation, the limit sensors (or switches) are used to stop the motion at the end of the allowable
travel range. Only one of the two switches will interrupt motion in a given direction.
When connecting other motor drives or mechanics, the correct limit switch wiring must be determined.
To do this, set the system into a safe position, set a low velocity with the SV command, begin motion
with an MR, MA or FE command and enable limit switch operation with the LN command. While the
motor is moving, actuate the limit switch toward which it is moving. If the motor stops, that is the correct
switch to connect at the end of desired motion for that direction. If the motor does not stop, actuate the
other limit switch. If the motor still does not stop, remove power and read further.
Each axis has provision for two limit switches and a reference switch, in addition to a
differential quadrature encoder input with index capabilities. For highest precision in a homing
application, motion is commanded until the reference switch is encountered, then continues at
a slower rate until the encoder index is found. With this procedure, the home position may be
repeated to an accuracy of one encoder count, or the ultimate accuracy of the system.
All limit and reference switch inputs are sensed through line receivers with 1 volt of hysteresis
for noise rejection. The encoder inputs use differential line receivers with 300 mV of hysteresis.
They may be used with single encoders, as well.
A capture/compare circuit is used to sense any change in the state of the limit and reference
switches. When any one of them changes, a maskable interrupt is generated. These are
several additional sources of interrupt, including excessive error, encoder error index, and
absolute and relative position breakpoints.
LM629 Data
1
Input register
6 (Read only)
Software reset
7 (Read only)
Interrupt register
2 (Read only)
Limit switch register
3 (Read only)
Configuration and output
6 (Read only)
LM629 Commands
0
(Desired channel selected by configuration register bits 6, 7, address 6)
The
C-400
©
controller uses National Semiconductor LM629 integrated circuits to perform the
servo control functions. If the user wishes to program them directly, the programming is done
exactly as described in National's programming manual. For those users wishing to use the
C-400
©
in an interactive manual mode, joystick operation is possible also as an add-on option.