Operation, Safety precautions, General description – Lincoln Electric IM10058 POWER WAVE STT MODULE User Manual
Page 15: Power-up sequence, Duty cycle, Common welding procedures, Recommended processes and equipment, Warning, Recommended processes, Process limitations
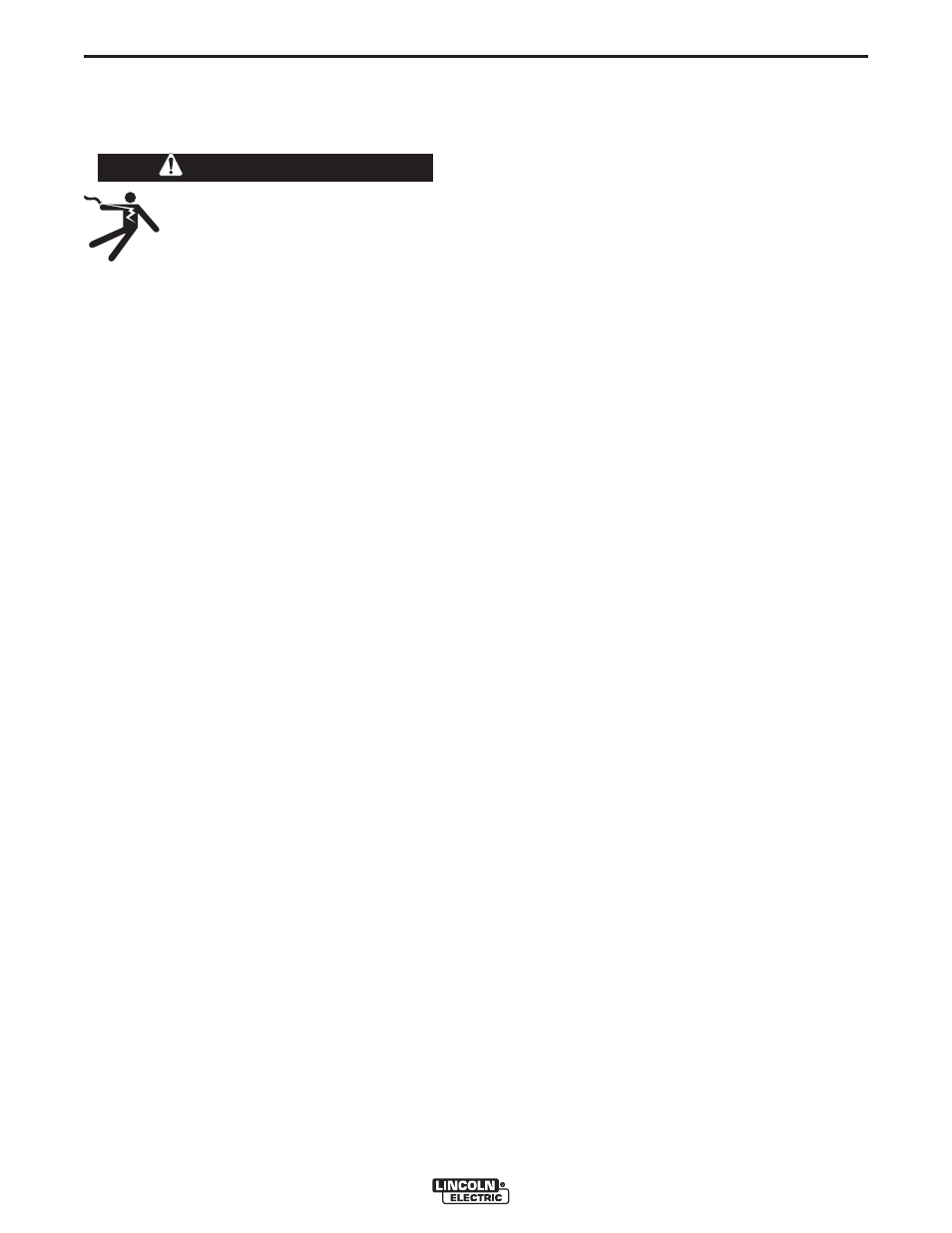
B-1
OPERATION
POWER WAVE
®
STT
®
MODULE
B-1
SAFETY PRECAUTIONS
Read this entire section of operating instructions
before operating the machine.
ELECTRIC SHOCK can kill.
• Disconnect input power before
servicing.
• Do not operate with covers removed.
• Do not touch electrically live parts.
• Only qualified persons should install, use or
service this equipment.
------------------------------------------------------------------------
GENERAL DESCRIPTION
General Physical Description
The POWER WAVE
®
STT
®
MODULE is an accessory
enabling compatible power sources to perform the STT
®
function without limiting the normal multi-process rating
of the host machine. It is intended for use with medium
range “S”– series Power Wave
®
power sources such as
the S350. The module itself is a low profile pedestal,
designed to seamlessly integrate with compatible power
sources and water coolers.
General Functional Description
The POWER WAVE
®
STT
®
MODULE is essentially a
high speed, high capacity output switch, connected in
series with the positive output of the power source. It
communicates module status and identification informa-
tion to the power source via the ArcLink
®
protocol, and
receives a high speed synchronized switching command
via a dedicated digital link.
POWER-UP SEQUENCE
The POWER WAVE
®
STT
®
MODULE will be powered up
at the same time as the power source. The status light
will blink green for about a minute while the system is
configuring. After this time, the status lights will turn a
steady green indicating the machine is ready.
The fan in the POWER WAVE
®
STT
®
MODULE will run
only when the power source fan is activated.
DUTY CYCLE
The POWER WAVE
®
STT
®
MODULE is rated at 450
amps at a 100% duty cycle. It is further rated to support
500 amps at a 60% duty cycle and 550 amps at a 40%
duty cycle. The duty cycle is based on a ten-minute peri-
od. A 60% duty cycle represents 6 minutes of welding
and 4 minutes of idling in a ten-minute period.
Note:
The POWER WAVE
®
STT
®
MODULE is capable of
withstanding a peak output current of 750 amps. The
allowable maximum average output current is time
dependant, and ultimately limited by the host power
source.
COMMON WELDING PROCEDURES
MAKING A WELD
Choose the electrode material, electrode size, shielding
gas, and process (GMAW, GMAW-P, GMAW STT etc.)
appropriate for the material to be welded.
Select the weld mode that best matches the desired
welding process. The standard weld set shipped with the
host power source encompasses a wide range of com-
mon processes that will meet most needs. If the STT
modes are not available, or if a special weld mode is
desired, visit www.powerwavesoftware.com or contact
the local Lincoln Electric sales representative.
To make a weld, the power source needs to know the
desired welding parameters. Set the parameters on the
user interface typically located on the wire feeder. The
user interface sends the parameters (arc voltage, wire
feed speed, UltimArc
TM
value, etc.), to the power source
via the ArcLink
®
communication protocol through the con-
trol cables. The power source controls the POWER
WAVE
®
STT
®
MODULE based on the selected weld
mode.
For a more detailed description, and specific operating
instructions, consult the power source Instruction
Manual.
RECOMMENDED PROCESSES AND
EQUIPMENT
RECOMMENDED PROCESSES
The POWER WAVE
®
STT
®
MODULE is recommended
for all process supported by the host power source
including, but not limited to SMAW, GMAW, GMAW-P,
GMAW-STT.
PROCESS LIMITATIONS
The POWER WAVE
®
STT
®
MODULE is unaffected by
the voltage at the load, and therefore processes are only
limited by the current and duty cycle ratings listed in the
specifications for the product. The POWER WAVE
®
STT
®
MODULE is designed to protect itself from the excessive
transient voltages associated with highly inductive weld
circuits. These high inductance circuits may result in
unsatisfactory performance, but will not damage the
module.
WARNING