KB Electronics KBDA-29 (1P) User Manual
Page 10
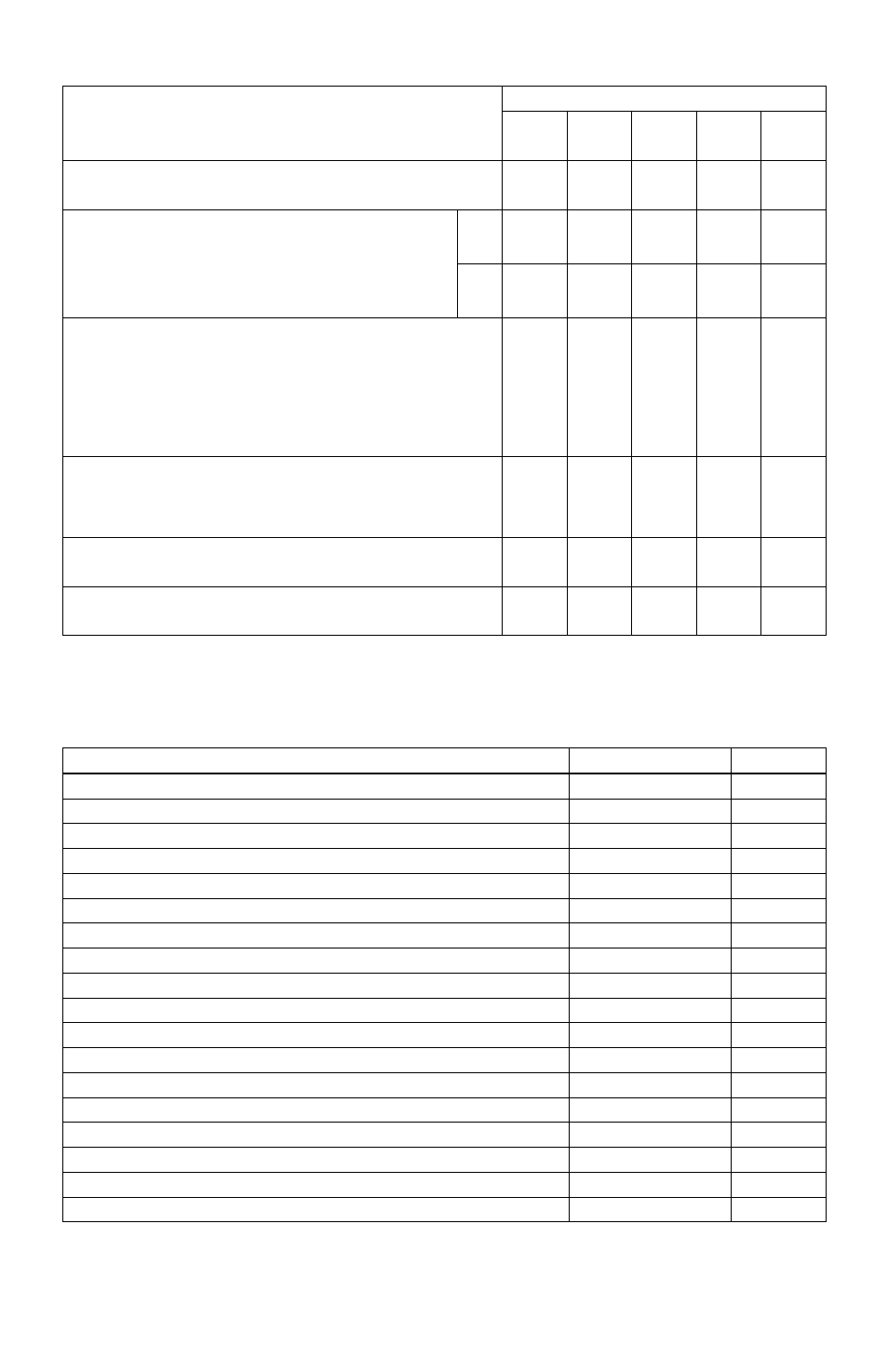
9
Description
Accessory Part No.
Model
KBDA-24D
Model
KBDA-27D
Model
KBDA-29
Model
KBDA-45
Model
KBDA-48
On/Off AC Line Switch – Disconnects the AC line. Mounts on the enclosure
cover and is supplied with a switch seal to maintain liquidtight integrity.
9482
9523
9532
9532
9532
AC Line Filter1 – Provides Class A Industrial Standard RFI (EMI)
suppression. Installs onto the drive’s PC board with quick-connect
terminals.
Suffix “S” – Filter must be used with built-in On/Off AC Line Switch.
Suffix “NS” – Filter must be used without On/Off AC Line Switch.
Suffix
“S”
9507
9512
9479
9479
9479
Suffix
“NS”
9507
9512
9515
9515
9515
IODA Input/Output Multi-Function Board – Provides a variety of functions,
which include preset frequency, up/down frequency control, signal isolation,
isolated output voltage for controlling auxiliary devices, open collector outputs,
and output relay contacts. Mounts on the drive’s PC board with two snap-ins
(located on the bottom of the mounting base) and two screws (provided). All of
the IODA inputs and outputs are isolated from the AC line.
See Appendix A, on page 42.
9668
9668
9668
9668
9668
Programming Kit – Includes DownLoad Module™ (DLM) handheld program-
ming device, which uploads and downloads drive programs, PC to DLM
serial and USB communication cables, DLM to inverter communication cable,
and PC Windows® based Drive-Link™ communication software.
9582
9582
9582
9582
9582
DIAC Modbus Communication Module – Allows direct communication
between drive and Modbus2 protocol.
9517
9517
9517
9517
9517
Liquidtight Fittings – Provide a liquidtight seal for wiring the drive. Kit
includes three 1/2” and one 3/4” liquidtight fittings.
9526
9526
9526
9526
9526
TABLE 1 – OPTIONAL ACCESSORIES
TABLE 2 – GENERAL PERFORMANCE SPECIFICATIONS
Notes: 1. Complies with CE Council Directive 89/336/EEC Industrial Standard. 2. Other protocols available – contact our Sales Department.
Notes: 1. IODA option board required. 2. Dependent on motor performance. 3. Do not operate the drive outside the specified AC line input voltage
operating range.
Description
Specification
Factory Setting
115 Volt AC Line Input Voltage Operating Range (Volts AC)
115 (± 15%)
—
208/230 Volt AC Line Input Voltage Operating Range (Volts AC)
208 (-15%) / 230 (+15%)
—
400/460 Volt AC Line Input Voltage Operating Range (Volts AC)
380 (-15%) – 460 (+15%)
—
Maximum Load (% of Current Overload for 2 Minutes)
150
—
Switching Frequency (kHz)
8, 10, 12
8
Signal Following Input Voltage Range1 (Volts DC)
0 – 5
—
Output Frequency Resolution (Bits, Hz)
10, .06
—
Minimum Operating Frequency at Motor (Hz)
0.3
—
Acceleration Time (Seconds)
0.1 – 180.0
1.5
Deceleration Time (Seconds)
0.3 – 180.0
1.5
Speed Range (Ratio)
60:1
—
Speed Regulation (30:1 Speed Range, 0 – Full Load) (% Base Speed) 2
2.5
—
Overload Protector Trip Time for Stalled Motor (Seconds)
6
—
Undervoltage/Overvoltage Trip Points for 115 Volt AC Line Input (± 5%) (Volts AC)3
76 / 141
—
Undervoltage/Overvoltage Trip Points for 208/230 Volt AC Line Input (± 5%) (Volts AC)3
151 / 282
—
Undervoltage/Overvoltage Trip Points for 400/460 Volt AC Line Input (± 5%) (Volts AC)3
302 / 567
—
Run/Fault Output Relay Contact Rating (Amps at 30 Volts DC, 125 Volts AC, 250 Volts AC)
1, 0.5, 0.25
—
Operating Temperature Range (°C / °F)
0 – 45 / 32 – 113
—