Maintenance – Alamo RHINO 95C User Manual
Page 48
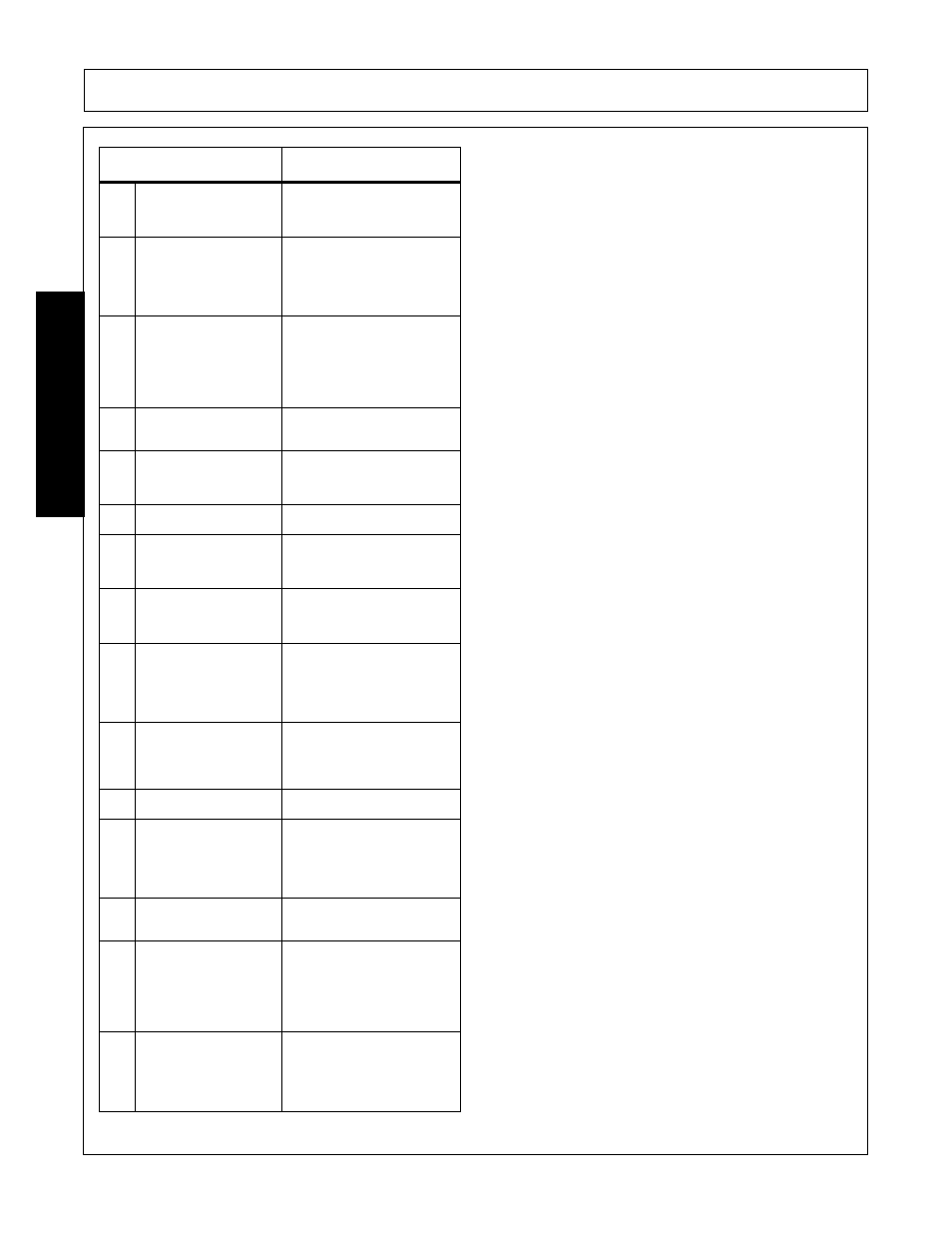
MAINTENANCE
F-4145 01/11
Maintenance Section 5-6
© 2011 Alamo Group Inc.
MAINTENANCE
30. This valve is a precision device and is not intended for
extensive field adjustment or repair. Field replacement
parts are limited to seal kits, cartridges and tie rod ends.
Beyond replacement of these parts, opening of check
cavities and certain relief valve cavities to examine for
trapped dirt, or resetting main relief valve with the use of a
good pressure gauge, valve should be returned for service.
Dirt and shreds of packing material are the usual causes of
valve malfunction. Be sure that oil supply is kept clean. Use
only factory supplied packings in cylinder repair. Fittings
and hoses must be clean before being removed.
NOTE: Pay close attention to all caution warning notes so
valve will not have to be returned to manufacturer for
reconditioning.
Troubleshooting guide is designed to help qualified
individuals, with valve service training, correct minor
problems which may develop. If valve is under warranty do
not attempt disassembly for repairs. Contact your
authorized dealer. Any attempt to disassemble valve during
warranty period will VOID warranty.
15
Excessive back
pressure.
Restriction between “in”
and “out” port and
reservoir.
16
Paint on valve spool.
Sticking valve spool,
or scored valve.
Clean valve spool.
Binding may be caused
by over tightened plug,
mounting bolt, fitting or tie
rod bolt. See Item 30.
17
Oil leakage past
spool seal into spool
cap.
If spool cap contains oil,
replace spool seal o-ring.
If o-ring retainer is
“bellied”, check for
restriction from “out” port
reservoir. See Item 30.
18
Broken return
springs.
Replace broken return
springs.
19
Bent spool.
Return for factory repair
or replace with new spool
section. See Item 30.
20
Foreign particles.
Clean system and valve.
21
Misalignment of
control handle
linkage.
Check linkage for binding
condition.
22
Spool not moved to
full stroke.
Spool travel should be
5/16” either way or 5/8”
total.
23 Relief
valve
setting
in control valve too
low or defective.
Clean or overhaul relief
valve or replace cartridge.
Refer to VALVE
SERVICE section for
proper PSI settings.
24
Overload relief valve
in control valve
stuck open or
malfunctioning.
Clean relief. Do not
disturb pressure setting
or replace cartridge.
25
Worn control valve.
Replace control valve.
26
Check poppet in
control valve not
holding.
Clean check poppet(s)
carefully. Ensure free
movement and proper
seating or replace check
poppet. See Item 30.
27
Damaged or worn
spool seals.
Replace spool end seals.
28
Check ball in anti-
cavitation is stuck or
not seated properly.
Clean anti-cavitation
valve carefully. Assure
that checks move freely
and seat properly or
replace cartridge. See
Item 30.
29
Valve cap and
center return
mechanism binding.
Loosen screws holding
cap on valve (ref. Valve
Service image). Operate
valve spool and retighten
screws.
POSSIBLE CAUSE
CORRECTIVE ACTION