Commissioning & set up procedures, Caution – Magnum Venus Plastech Megaject MKIV Revision 1_2 User Manual
Page 11
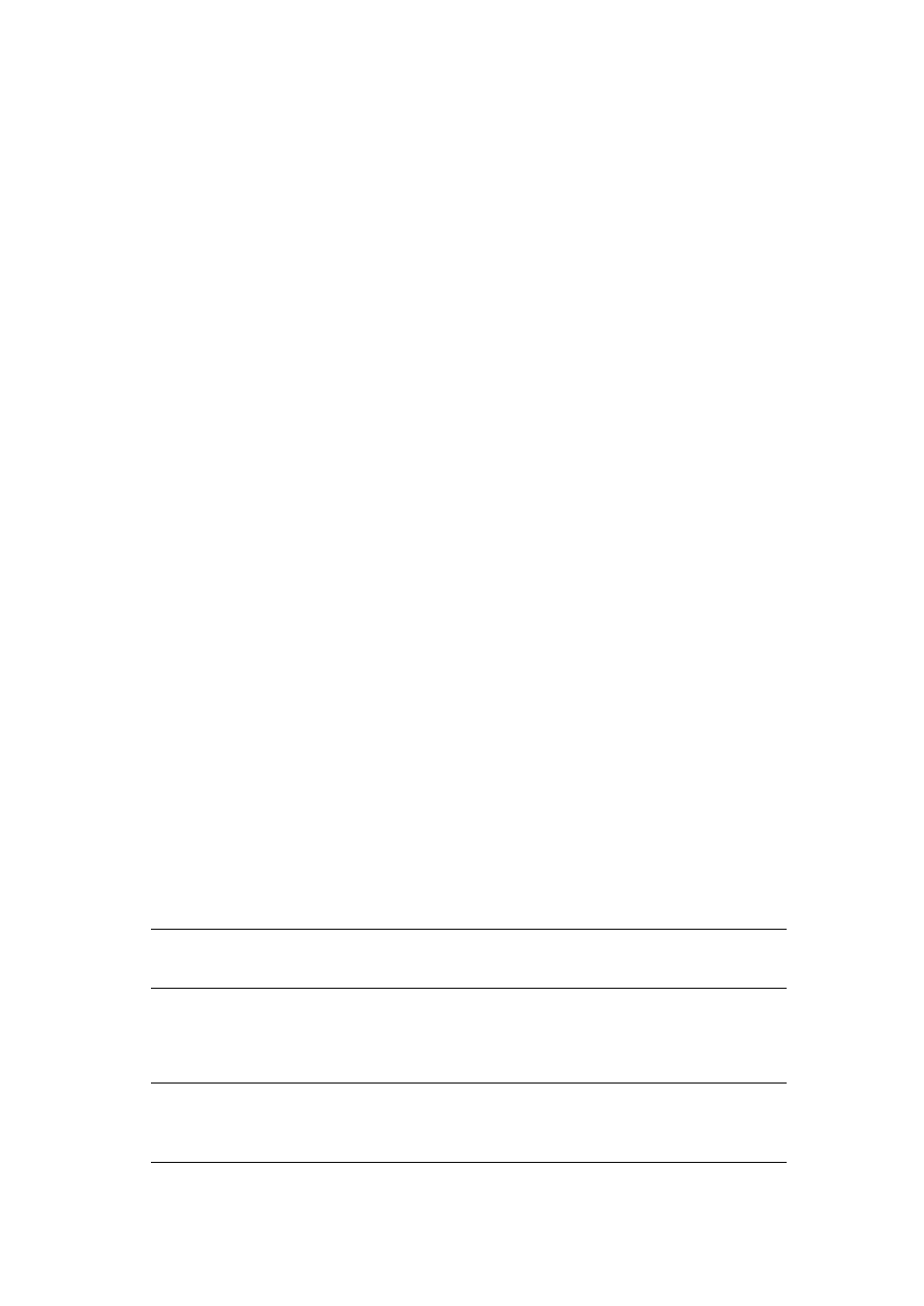
Megaject MK IV Issue 1_2 25/11/2003
Page 11 of 31
Commissioning & Set Up Procedures
CAUTION
Overalls and eye protection must be worn at all times during operation of the
machine.
CAUTION
Do not adjust the catalyst overpressure valve. If in any doubt about operation or
adjustment of any part of this machine please contact Plastech TT.
IMPORTANT NOTE
The resin pump upper collar must be filled with Plastech Pump Lubricant (supplied) to
clean and lubricate pump seals. Remove rear guard window and fill to approximately
10mm below top lip.
An oiler/lubricator must NOT be used in the air supply to the machine. Air must be
filterd and dry at 6-8 bar (85-115 psi).
The Megaject MK IV is tested and secured against leaks prior to despatch. It is
essential that the inlet tube connected to the resin pick up pipe and filter remain tight
and sealed at all times to prevent air ingress into the resin system.
We recommend the use of Acetone as the primary choice of cleaning solvent. If a
different solvent system is to be used please contact Plastech for details of changes
required.
Procedure
1. Connect earth lead from solvent tank to a suitable earth point. Ensure recirculation
switch is off. Connect 10mm air line (supplied) to workshop air supply. Pull the ON
switch down to the ON position. Observe incoming air pressure gauge reads a
minimum 6 bar at all times.
2. Place resin pick up pipe and resin recirculation pipe in resin container. Securely
anchor both pipes.
Note: If the machine is to be fed directly from a resin tank it may not be possible to use
the resin pick up pipe and filter supplied. A suitable in-line filtering system is
available from Plastech TT
3. Using the funnel provided, fill catalyst container to approx 3/4 full. For polyester
resin systems we recommend Acetyl Acetone Peroxide (AAP) catalyst (e.g.
Luperox 224).
Note: The use of MEKP is not recommended for RTM as product de-mould time is
significantly longer than with AAP. MEKP may also cause ‘gassing’ in the catalyst
system resulting in inaccurate catalyst flow and potential ‘wet spots’ in the
moulded part.