Pi stability settings, Maximum trim, Inertia compensation – Cleveland Motion Controls WebPro Winder Tension ControllerMWP-12664 REV BA User Manual
Page 21: Controller tuning - surface winder, Webpro winder tension controller
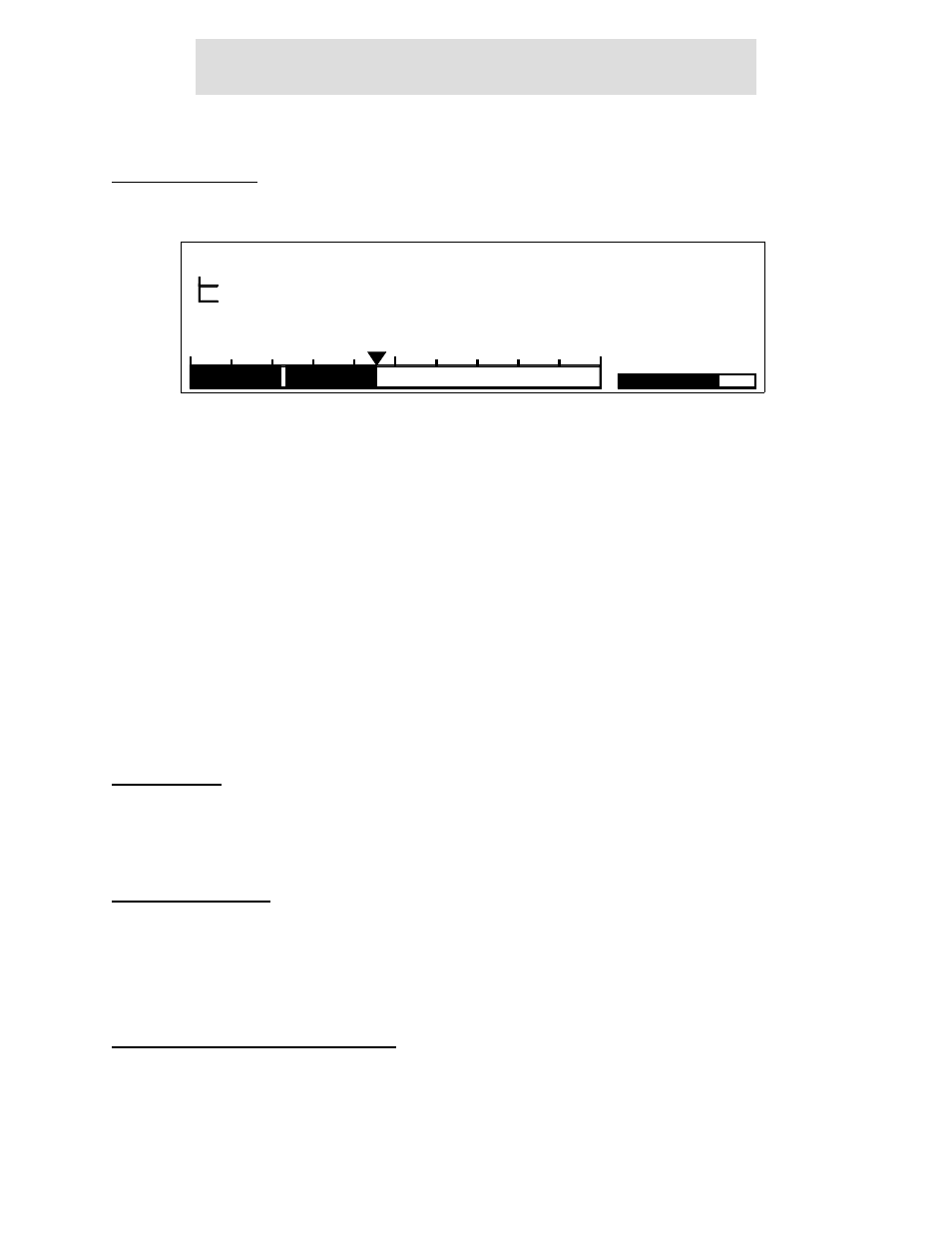
AO-70171
20
Revision BA
WebPro Winder Tension Controller
near maximum and briefly allow the machine and tension to settle. If the measured tension at high speed
is lower than that at low speed, increase the Dynamic Friction value to compensate for losses.
PI Stability Settings
There are two methods of setting the PI stability; through the Product Parameter menu with the machine
at rest or through the Adjust PI stability menu with the machine running.
Access the Adjust PI stability menu from the Commissioning menu. Run the machine with the Controller
in Auto at a Tension Set Point of approximately 50%. Use the SCROLL keys to select the parameter to be
changed and adjust the parameter using the numeric keys or the +/- keys. Press the CONFIRM key to
implement and save the change. An asterisk alongside the Product Number indicates that a parameter
has been changed and that the CONFIRM key must be pressed to implement and save the change.
When the best performance is achieved stop the machine, remember to press CONFIRM and then press
SET UP to return to the Commissioning menu.
To simplify the tuning there are five factory set PI values. One of these values should be suitable for most
applications. If it is found necessary to apply different PI values, select Custom and starting from PI
values that gave stable but sluggish operation, reduce the P band % value and reduce the I time value
until the desired performance is achieved. Remember to press the CONFIRM key before exiting the
Product Parameter or the Adjust PI stability menus in order to implement and save any changes.
The five preset PI values are:
very slow
slow
medium
fast
very fast
Proportional
band
2000%
1200%
800%
500%
200%
Integral time
20 sec
12 sec
8 sec
5 sec
2 sec
Maximum Trim
Set this item to a value which gives best overall performance. Too large a value may apply too much
correction and make the system unstable. The value should be sufficient to compensate for tension
disturbances, diameter calculator errors and any other errors. Extensible materials may require a trim
value higher than more rigid materials. As a guide set this value to 10%.
Inertia Compensation
While accelerating or decelerating the machine at the normal maximum rate observe the measured
tension bar graph and the desired tension set point triangle. If these differ by more than 10% adjust the
Inertia Time Constant and the Coefficient to compensate for any increase in tension while accelerating or
decrease in tension while decelerating. The Inertia Time Constant determines the rate of correction, the
Coefficient determines the amount of correction.
Controller Tuning - Surface Winder
It is essential that all motor drives are correctly set in accordance with the suppliers instructions BEFORE
the Controller is commissioned. The Controller will not compensate for incorrectly set drives.
PRODUCT NUMBER
PI STABILITY
INERTIA TIME CONSTANT
INERTIA COEFFICIENT
MAX TRIM
PROPORTIONAL BAND
INTEGRAL REPEAT
1
*
MEDIUM
800%
8S
2S
0.0%
10%
TENSION S.P.
OUTPUT %
45 N