5 accuracy considerations, Ccuracy, Onsiderations – Cleveland Motion Controls Classic Series DIN Rail Amplifier Non-Isolated MWI-13466 REV CA User Manual
Page 19
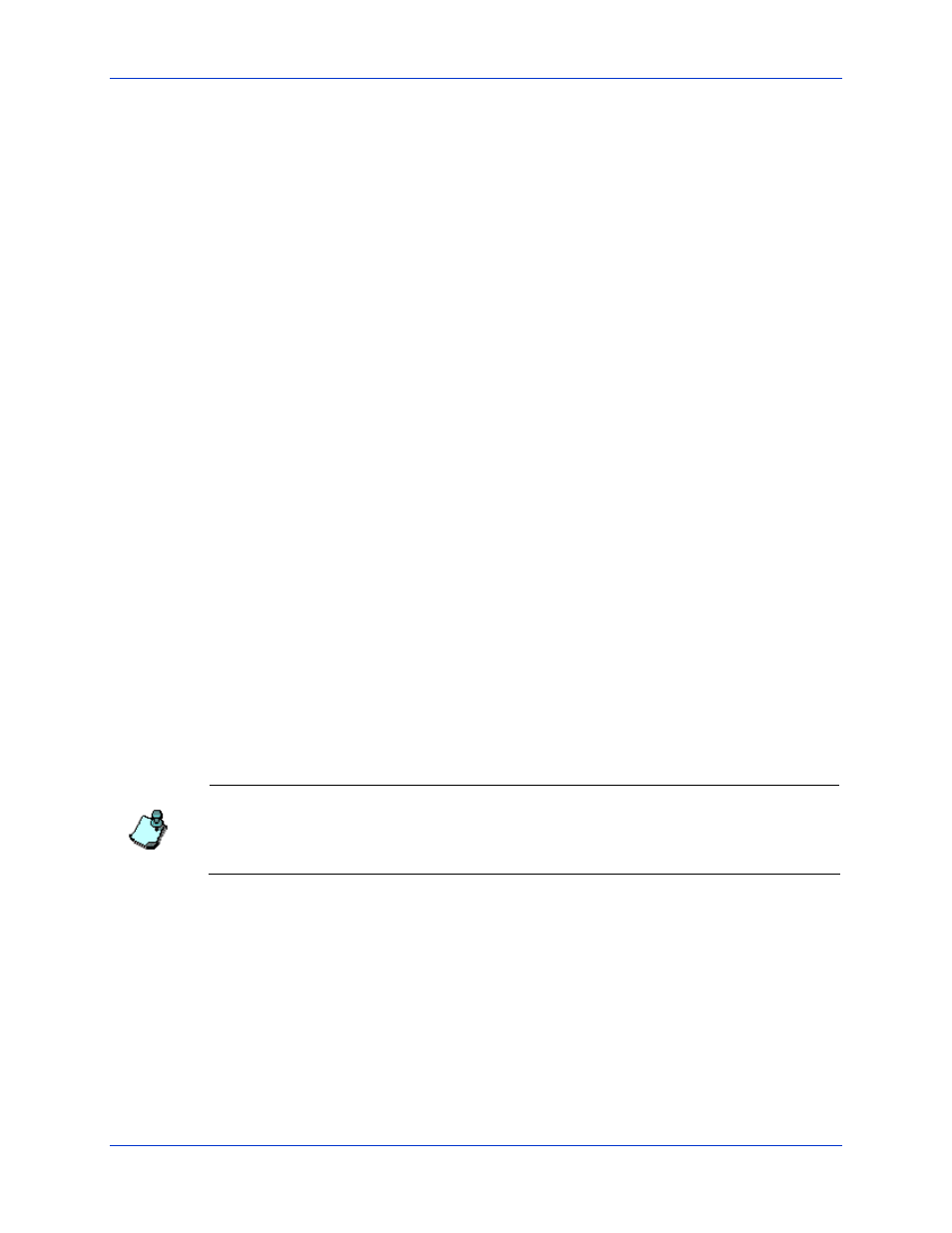
MAN-13466
R
EV
CA C
LASSIC
S
ERIES
N
ON
-I
SOLATED
A
MPLIFIER
P
AGE
19
OF
26
3.5 A
CCURACY
C
ONSIDERATIONS
The application of an accurate calibration force requires careful attention to minimizing the non-ideal affects of the
real world. Keep the following points in mind:
•
Allow the transducer and amplifier to reach thermal equilibrium before conducting calibration. Ideally, the
temperature should reflect the expected operating conditions.
•
The test force should be a moderate percentage of the intended working force of the transducer, and never
over 100% of the transducer’s Maximum Working Force (MWF) or, you risk calibrating with an
overloaded (“clipped”) transducer signal.
•
Cycle the load on the transducer a number of times with the test force to pre-condition or “set” the
transducer prior to calibration. Repeat this procedure again before calibrating if the transducer has been
disturbed (i.e. bolts re-torqued).
•
With very low force transducers consider that connecting a test mass involves some finite cord mass.
•
When all else is done correctly, the largest remaining contributor to error is friction. If friction cannot be
reduced, consider determining the magnitude of the friction through measurement and then making first
order corrections numerically.
•
Passing a cord over a roll on its way to the transducer will cause some amount of friction. The worst case
scenario is in passing the working part of a cord over a roll that does not readily freewheel. A test was
conducted to determine the loss on a stationary 4” diameter anodized roll with a 90 degree wrap angle. It
exhibited a 25 to 30% loss in force due to friction!
•
Always apply and remove the test load in a continuously increasing or decreasing manner, so that the force
changes are monotonic. This helps to avoid disturbing any hysteresis component of the transducers force
signal.
•
When calibrating for a particularly wide roll that will always have a narrower product tracking to one side,
consider applying the calibration force at the roll position that represents the center of the product. This
will automatically cancel some of the affects of transducer gain imbalance without the need to actually re-
balance the transducers gains within the amplifier.
•
It is a good practice to verify linear operation of the transducer and amplifier by applying a final test force
that falls somewhere between the zero and full-scale endpoints. The intent is not to conduct calibration, but
to confirm the hardware’s ability to accurately report a measured force.
When conducting a calibration that involves a large mass, it is often practical to use a series of smaller masses
added in succession. Consider performing an initial Zero and Gain adjustment when the first 20% of the
weights have been applied. By performing the calibration using this method, the Zero and Gain adjustments
can be made approximately correct earlier in the calibration effort (before many weights have been handled).
When the full calibration load is applied, there is a better chance that only minor adjustments will be needed.