Vii. trouble shooting guide sec tion vii – Cashco SCV-S User Manual
Page 10
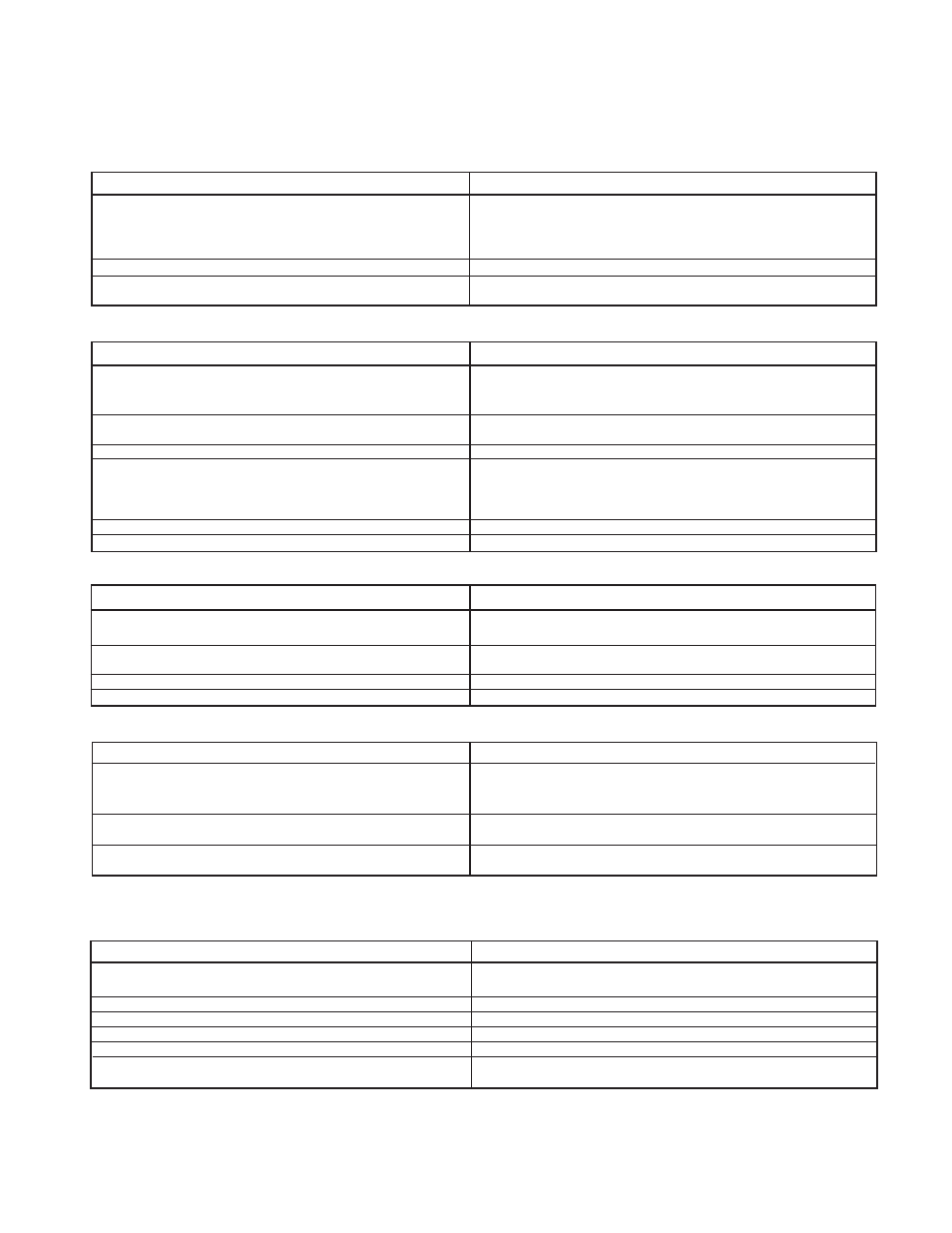
IOM-SCV-S
10
5. Inadequate valve shutoff.
Possible Cause
Remedy
A. Permanent "tracks" where seating occurs.
A1. Relap body seat and plug (metal seat).
A2. Replace body and plug or comp. seat disc.
B. Excess valve pressure drop.
B. Reduce valve's shutoff pressure drop.
C.
Insuffi cient IAS pressure.
C. Provide required level of IAS pressure.
D. Obstruction at seat.
D. Remove body and inspect for obstruction.
E. Improper calibration.
E. Recalibrate positioner and valve stroke.
F. Improper actuator bench set range.
F. Disassemble actuator and change to stiffer range springs.
Reinstall and increase IAS to proper level.
1. Unit can not pass enough fl ow.
Possible Cause
Remedy
A. Sizing data not correct; valve undersized.
A1. Check actual pressures, temperature, and fl ow rates against
the variables used for sizing.
Recalculate
Cv
Required.
A2. Replace unit with larger body size.
B. Obstruction at inlet.
B. Remove valve and inspect line for blockage.
C.
Insuffi cient valve travel.
C1. Verify full travel.
C2. Verify correct IAS pressure.
2. Unit can not control steadily at low fl ow rates.
Possible Cause
Remedy
A. Sizing data not correct; valve oversized.
A1. Check actual pressures, temperature and fl ow rates against
the
variables
used.
A2. Replace full port body with reduced port body.
B. Obstruction at inlet.
B. Remove valve from line and inspect for something
causing
blockage.
C. Too short of “stroke”.
C. Remove unit and calibrate.
D. Excess pressure drop.
D1. Check actuator bench setting; re-calibrate as required.
D2. Check design pressures against actual pressures. Replace
“low” bench set range springs with higher bench set
range
springs.
E.
Insuffi cient IAS pressure.
E. Provide required level of IAS pressure.
F.
Incorrect
fl ow direction.
F. Verify fl ow with arrow cast on body; FTO
3. Valve body leaking at clamped end connection joints.
Possible Cause
Remedy
A. Excess pressure levels.
A. Check actual pressures against those indicated in Technical
Bulletin.
Reduce
pressures
as
necessary.
B. Loose clamp.
B. Remove valve from service. Disassemble and clean.
Reassemble and properly tighten all clamps at reinstallation.
C. Excessive piping stress.
C. Place hanger on control valve unit.
D. Improper pipe alignment.
D. Re-do piping properly.
4. Fluid leakage at bonnet or at upper stem seal ring.
Possible Cause
Remedy
A. Gasket failure.
A1. Remove body, disassemble, remove old gasket Install new
gasket,new stem seals, reassemble and reinstall.
A2.
Seal
ring
failure.
B. Overheating
B. Ensure that max. operating temperature of
366°F
(186°C)
is
not
exceeded.)
C. Stem seal failure
C1. Worn stem seals. Replace seals and gasket.
C2. Pitted stem, worn stem. Replace plug/stem, seals and gasket.
VII. TROUBLE SHOOTING GUIDE
SEC TION VII