Danger!! danger!! danger, Relieve all internal pressure before servicing, Line pressure must be 0.0 psi – Fill-Rite TS06 LPG Precision Meter User Manual
Page 10
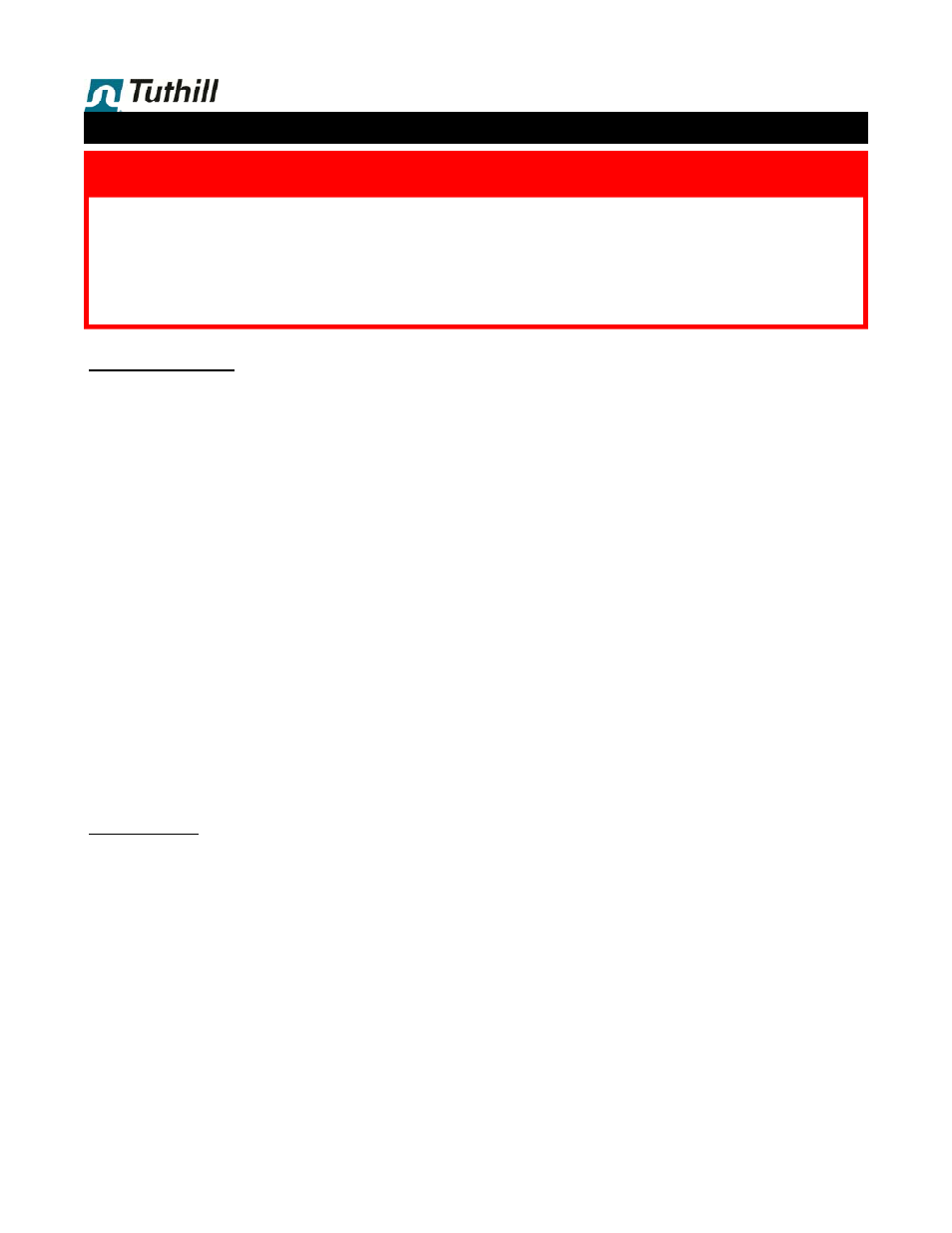
Preparing for Service:
Close the belly valve of the supply tank.
Close the valve on the vapor return line.
Close the manual valve in the supply line on eh inlet
side of the meter. If no manual valve exists on the inlet
side, consult the dispenser manufacturer on installer for
procedures to depressurize the system.
Slowly open the valve/nozzle on the end of the supply
line
After product is bled off, close the valve/nozzle at the
end of the supply line.
Open the bleed valve provided by your installer to re-
lieve the system pressure. Product will drain from the
meter system.
As product is bleeding from the bleed valve, slowly reo-
pen and close the valve/nozzle on the discharge line.
Repeat this step until the product stops draining from
the bleed valve and discharge line valve/nozzle.
Leave the discharge line valve/nozzle open while work-
ing on the system.
General Service:
Do not scratch or mar any of the precision machined
surfaces by prying or sanding parts.
Torque specifications. All fasteners such as screws and
bolts should be torqued to proper specifications. See
the “Torque Chart” in this manual.
Stone the machined surfaces when reassembling the
meter to assure the machined surfaces are free of burrs
and scratches.
Repair pulled threads with threaded insert fasteners.
These can be used in many instances. Contact your full
-service distributor for advice if this occurs.
Coating threads: When removing and replacing bolts
and screws in a meter, always coat the threads with anti
-seize.
Removing flange seals: When removing the flange
assembly, always carefully remove the O-ring seal.
Make sure that the flange surface is clean. Discard and
replace the old O-ring seals if it is nicked or scratched in
any way. It is undamaged, it can be re-used.
Examine all fasteners: make sure fasteners are not
bent, rusted, or have pulled or burred threads. The
threads should all appear evenly placed. If the bolts are
bent, check the housing and cover for flatness. Use a
straight edge to determine flatness. Use a stone to
remove any burrs on the flat surfaces for the housing.
Look for gaps: When disassembling a meter, use a
feeler gauge to check for gaps between the post and
gear plates and housing. If you do find gaps, check the
plates for flatness with a straight edge. Gaps can be
caused by shock problems that must be resolved. Con-
tact your full service distributor, or the Service Depart-
ment at TUTHILL meters for assistance if this occurs.
Check the O-Rings: O-rings should be smooth.
Cracked or worn O-rings should be replaced. However,
a more serious problem of shock my have occurred if
the O-rings are nibbled or extruded. Shock problems
must be verified and resolved. Contact your full service
distributor, or the Service Department at TUTHILL me-
ters for assistance if this occurs.
Check the post and gear plates: Check the plates for
flatness. Use a straight edge. Warped plates can be
caused by hydraulic shock problems that must be re-
solved. Contact your full service distributor, or the Ser-
vice Department at TUTHILL meters for assistance if
this occurs.
Weights & Measures: Check with the regulatory agency
that governs Weights and Measures in your area. Re-
moving a seal wire may require Weight & Measures
recalibration.
Danger!! Danger!! Danger!!
Relieve all internal pressure before servicing.
Line pressure must be 0.0 PSI
Serious injury or death from fire or explosion could result from maintenance of an
improperly de-pressurized and evacuated system.
10
Flow Meter Maintenance