Operation & maintenance – AAON V3-E User Manual
Page 18
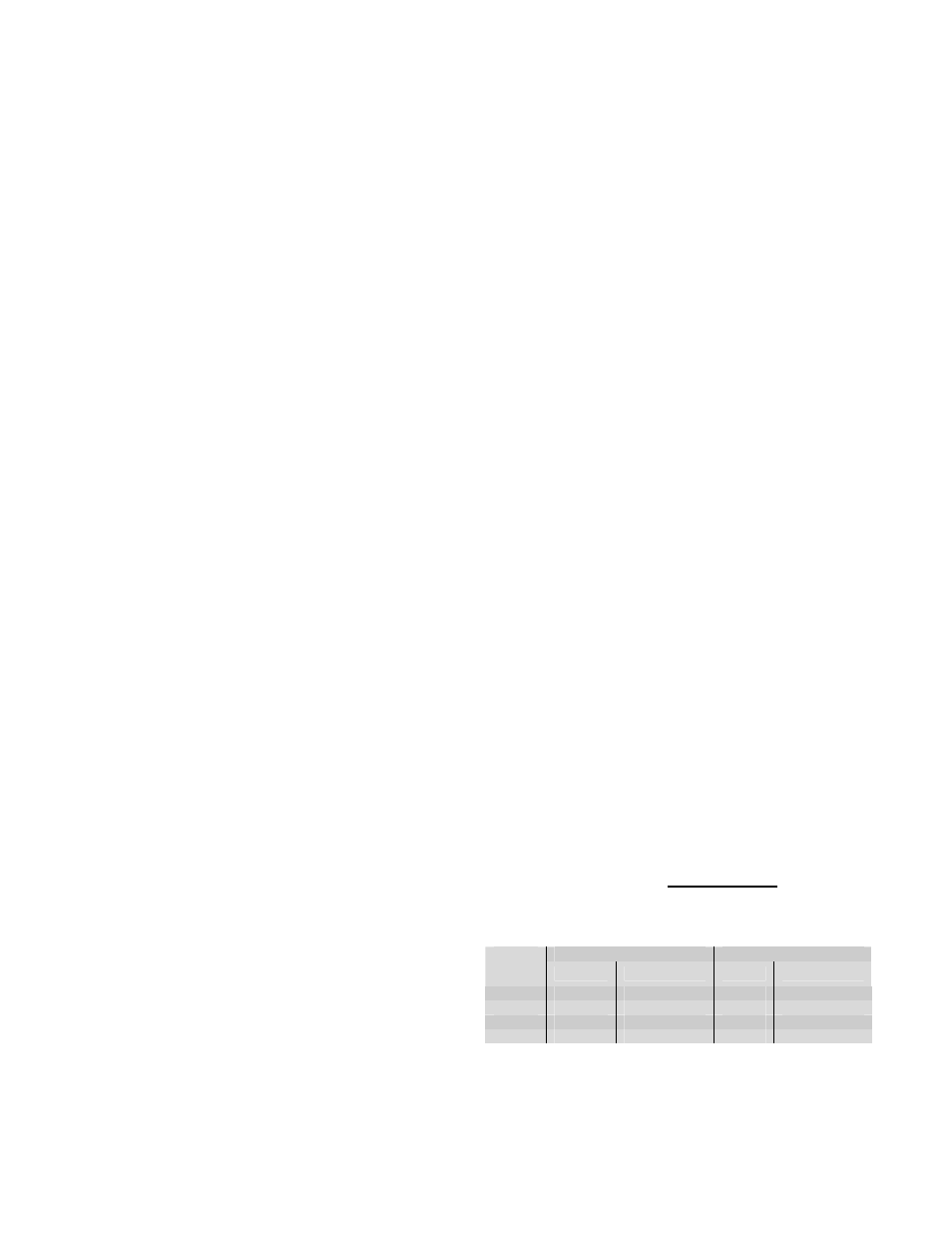
www.aaon.com
18
5. Operation & Maintenance
General
Immediately following building occupancy, the air
conditioning system requires a maintenance schedule
to assure continued successful operation. A
maintenance program similar to the example given
below should be scheduled for routine maintenance of
this equipment in order to provide continued efficient,
and reliable operation for the owner.
Maintenance Schedule
One week after start-up:
− Check refrigerant charge. Evacuate and repair
coil if leaking.
− Adjust belt tension on all fan drives.
− Check filters for cleanliness. Measure pressure
loss if applicable. Replace if necessary.
− Check cycling of compressors, fans, and valves.
Correct unusual cycling.
Monthly:
− Lubricate bearings if operating continuously at
1500 rpm, or higher, or in other extreme
conditions.
− Check cleanliness of filters, and replace if
necessary.
− Check cooling coil drain pan to assure proper
drainage.
− Inspect evaporator, and condenser coils. Clean if
dirty, or obstructed in any way.
Quarterly:
− Lubricate bearings if operating at 1000 rpm, or
less, and in temperatures less than 150
°F, or other
extreme conditions.
− Check damper operation for freedom of
movement. Correct any binding that may occur.
− Check belts, and pulleys on all fan drives for
tension, and unusual wear.
− Check operation of heating, and cooling section if
seasonal.
− Check inlet, and outlet air temperatures.
Determine cause for abnormal changes.
Annually:
− Clean the condenser, and evaporator coils with
steam, or a non-corrosive coil cleaner.
− Clean the drain line, “P” trap, and condensate pan.
− Check refrigerant pressures, and temperatures
every Spring, and correct unusual operation.
− Check heating section every Fall. Check all
electrical connections for tightness, and check
heater elements for indications of overheating.
Determine cause and replace elements if
necessary.
Blower Assembly
H2/V2 air handlers use backward inclined airfoil blower
wheels* that are non-overloading, very efficient, and
very easy to clean. Clean blower wheels are
necessary to reduce electrical use, maintain capacity
and reduce stress on the unit. The blower wheel, and
blower section need to be inspected periodically, and
cleaned of dust, or debris.
To inspect and clean the blower; set thermostat to the
“OFF” position; turn the electrical power to the unit to
the “OFF” position at the disconnect switch. Clean the
assembly, check the bearings for looseness, inspect
the belt condition and tightness, check screws for
tightness, rotate blower wheel while listening close to
each bearing to check for noise or roughness in the
bearing, which indicates a failing bearing.
Bearings
AAON uses pre-lubricated bearings, and bearings that
have been sized for an average failure rate of 50%
after 200,000 hours, or 22.8 years, of operation (see
heading “Lubrication” in this section for more
information). The bearing sizing tables below are
based on rotational speeds, and radial loading.
However, the alignment of the bearing to the shaft,
and the security of the bearing inner race to the shaft
will greatly affect bearing life. Even though the
manufacturer is responsible for bearing tolerances,
and mounting design, the installer or start-up
technician is advised to check the security of the
bearing locking system before start-up.
Table 18.1, Bearing Setscrew Torque Recommendations
Setscrew Locking
Skewzloc Locking
Shaft
Size
(In.)
Thread
Torque
(In-Lbs)
Thread
Torque
(In-Lbs)
1
1/4 - 28
66 - 85
8 - 32
63 - 70
1 3/16
1/4 - 28
66 - 85
8 - 32
63 - 70
1 7/16
5/16 - 24
126 - 164
10 - 24
81 - 90
1 7/8
3/8 - 24
228 - 296
1/4 - 20
162 - 180
*Exception – Size A1 H2/V2 uses 10” forward curved fan