File | setup | input tables, File | setup | output – MoTeC SDC3 User Manual
Page 12
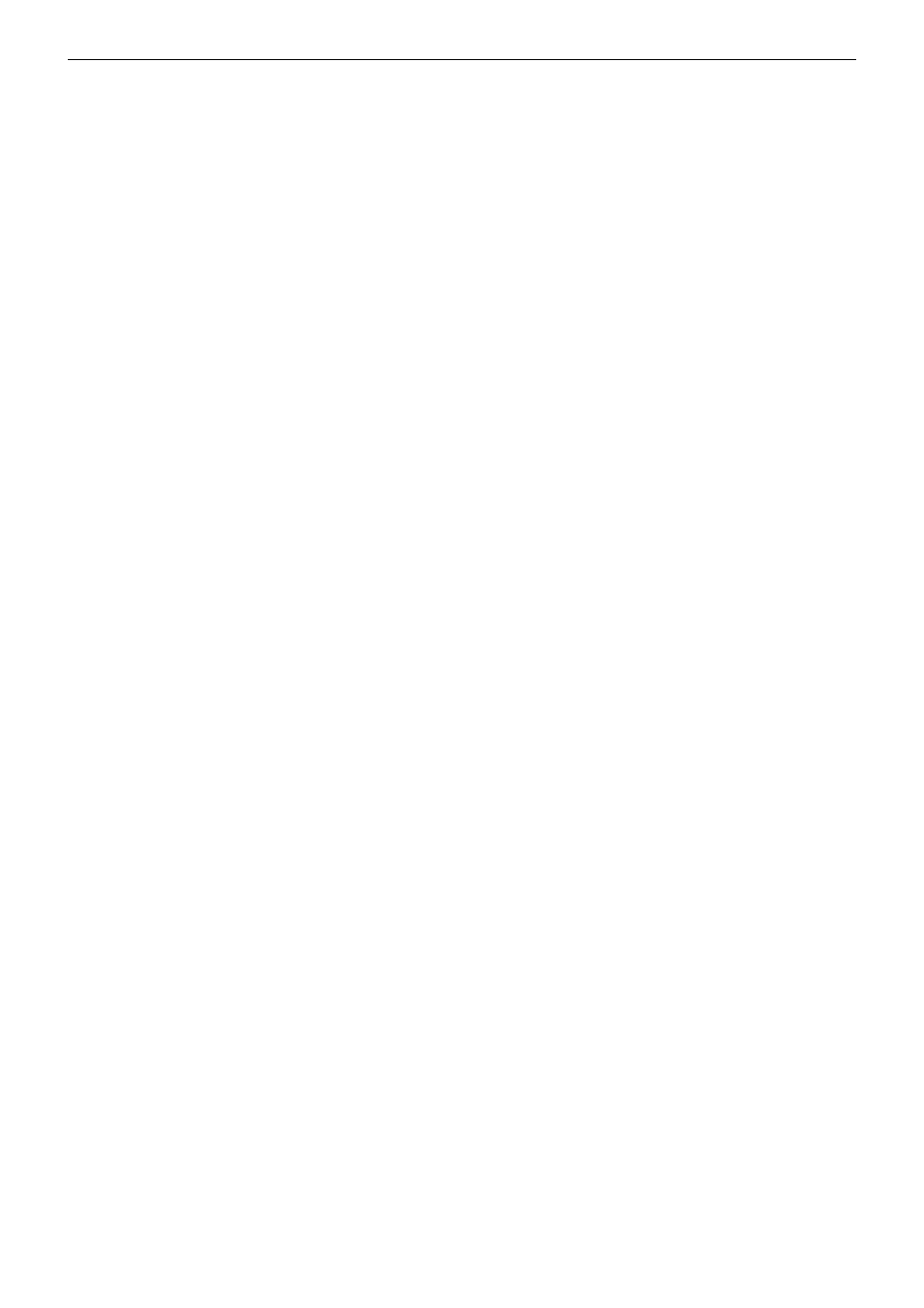
MoTeC SDC3
10
Setup
Speed Sensor
For Wheel Speed speed measurement method.
Hall/Magnetic:
If the speed sensor type is hall effect (or equivalent), a hall switching threshold must be specified. If the
speed sensor type is magnetic, the Magnetic Levels table (File | Setup | Input Tables) must be configured.
Factory default is Hall.
Hall threshold:
The switching threshold for hall effect speed sensor inputs. Factory default is 2.2V.
Enable ABS Active Detection
If the ABS Active Detection is enabled then the ABS active status from the ABS computer is used as described in
the diff control strategy in the SDC3 Functionality section.
File | Setup | Input Tables
Magnetic Levels
For Wheel Speed speed measurement method.
If magnetic wheel speed sensors are used, the sensor thresholds must be specified in the magnetic levels table.
Thresholds are configured separately for front and rear sensors.
Up to 11 ascending speeds can be specified in the table and linear interpolation is used between points.
Throttle Position
The Throttle Position table allows the throttle position sensor to be calibrated in up to 11 steps, with linear
interpolation between points. The table specifies the throttle position characteristic between the TP Low voltage
(0%in) and the TP High voltage (100%in).
The Read buttons for the throttle sensor high and low voltages can be used to calibrate the sensor if the SDC3 is
powered and connected to the PC. To calibrate, press the TP High Read button with the throttle pedal fully
depressed, then press the TP Low Read button with the throttle pedal fully released.
File | Setup | Output
Output Control
The output control method can be configured as Duty cycle or Current control, as discussed under Diff Control
Methods
in the SDC3 Functionality section. The default output control parameters should only be changed by
advanced users.
Duty Cycle control is not recommended as the effective diff lock will change with diff temperature.
Full Lock Frequency:
Open Lock Frequency:
If duty cycle diff control is used, the diff drive frequency varies between the Open Lock Frequency at 0% diff
lock and Full Lock Frequency at 100% diff lock.
Full Lock Current:
The full lock current is the target diff current for a desired 100% diff lock. The target diff current varies
linearly between 0A for 0% lock and Full Lock Current for 100% lock. The factory default is 5.0A.
This parameter should only be changed by advanced users.
Min Pulse Width:
Max Pulse Width: