Gorman-Rupp Pumps SE2C3 115V 1P 1483930 and up User Manual
Page 28
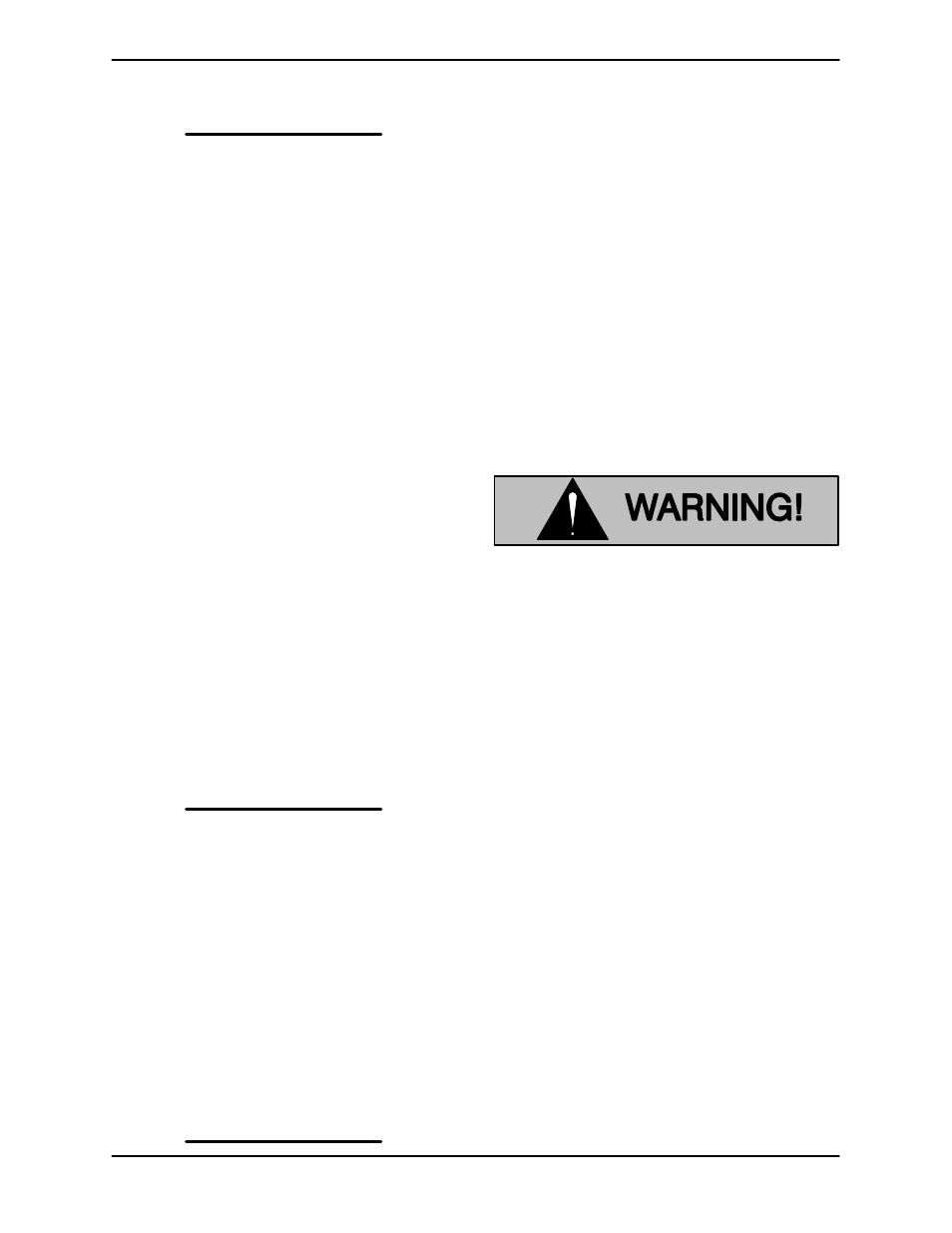
OM−06492
SE SERIES
MAINTENANCE & REPAIR
PAGE E − 6
when the seal chamber is removed. It may be nec-
essary to heat the sleeve and tap it off the shaft.
Remove the pump casing O-ring (59).
The lower stationary seal seat and element will re-
main in the pump casing bore when removed. To
remove the stationary portion of the seal, place the
pump casing on a clean cloth with the seal bore
side down. Use a drift pin or dowel to press on al-
ternate sides of the stationary seat until the station-
ary element and seat are forced out of the bore.
Inspect the dust seal (52) and, if replacement is re-
quired, use a drift pin or dowel to press the dust
seal out of the pump casing bore.
Lubricate the rotor shaft (53) adjacent to the bel-
lows assembly, and pull the rotating portion of the
seal from the shaft.
Slide a pair of stiff wires with hooked ends along
the shaft and use the wires to pull the upper sta-
tionary seal seat and element from the motor hous-
ing (10).
NOTE
Do not disassemble the motor unless it is neces-
sary and a clean, well-equipped shop is available. If
the motor housing components are to be serviced,
see MOTOR DISASSEMBLY in this section. Do not
reassemble the pump end components at this time.
If no further disassembly is required, proceed to
the appropriate areas in PUMP END REASSEMB-
LY.
PUMP END REASSEMBLY
NOTE
Reuse of old O-rings, gaskets, or shaft seal parts
will result in premature leakage or reduced pump
performance. It is strongly recommended that new
gaskets and shaft seal assemblies be used during
reassembly (see the parts lists for numbers).
Cleaning And Inspection Of Pump Parts
With the pump inverted, stuff a clean tissue into the
stationary seal seat bore of the motor housing (10)
or wrap a small rag around the shaft to prevent for-
eign material from entering the motor cavity.
Carefully inspect any O-rings or gaskets before re-
moval and cleaning to determine if a proper seal
and compression existed prior to disassembly. If
sealing was faulty or questionable, the cause must
be determined and corrected before reassembly.
Replace any parts as required.
Thoroughly clean all reuseable parts with a soft
cloth soaked in cleaning solvent. Remove all O-
rings and gaskets, and clean the sealing surfaces
of dirt or gasket material. Be careful not to scratch
gasket surfaces.
Most cleaning solvents are toxic and
flammable. Use them only in a well ven-
tilated area free from excessive heat,
sparks, and flame. Read and follow all
precautions printed on solvent contain-
ers.
Inspect the rotor shaft (53) for damaged threads,
scoring, or nicks. Remove nicks and burrs with a
fine file or emery cloth to restore original contours.
If the shaft is bent or severely damaged, the rotor
and shaft must be replaced as an assembly (see
MOTOR DISASSEMBLY).
Seal Installation
(Figures E-1 and E-2)
The shaft seal assembly (3) should not be reused
because wear patterns on the finished faces can-
not be realigned during reassembly. This could re-
sult in premature failure. If necessary to reuse an
old seal in an emergency, carefully wash all me-
tallic parts in fresh cleaning solvent and allow to dry
thoroughly.
Handle the seal parts with extreme care to prevent
damage. Be careful not to contaminate the preci-
sion finished faces; even fingerprints on the faces
can shorten seal life. If necessary, clean the faces