Gorman-Rupp Pumps 62 1/2D1-CH23 S/G 1211015 and up User Manual
Page 16
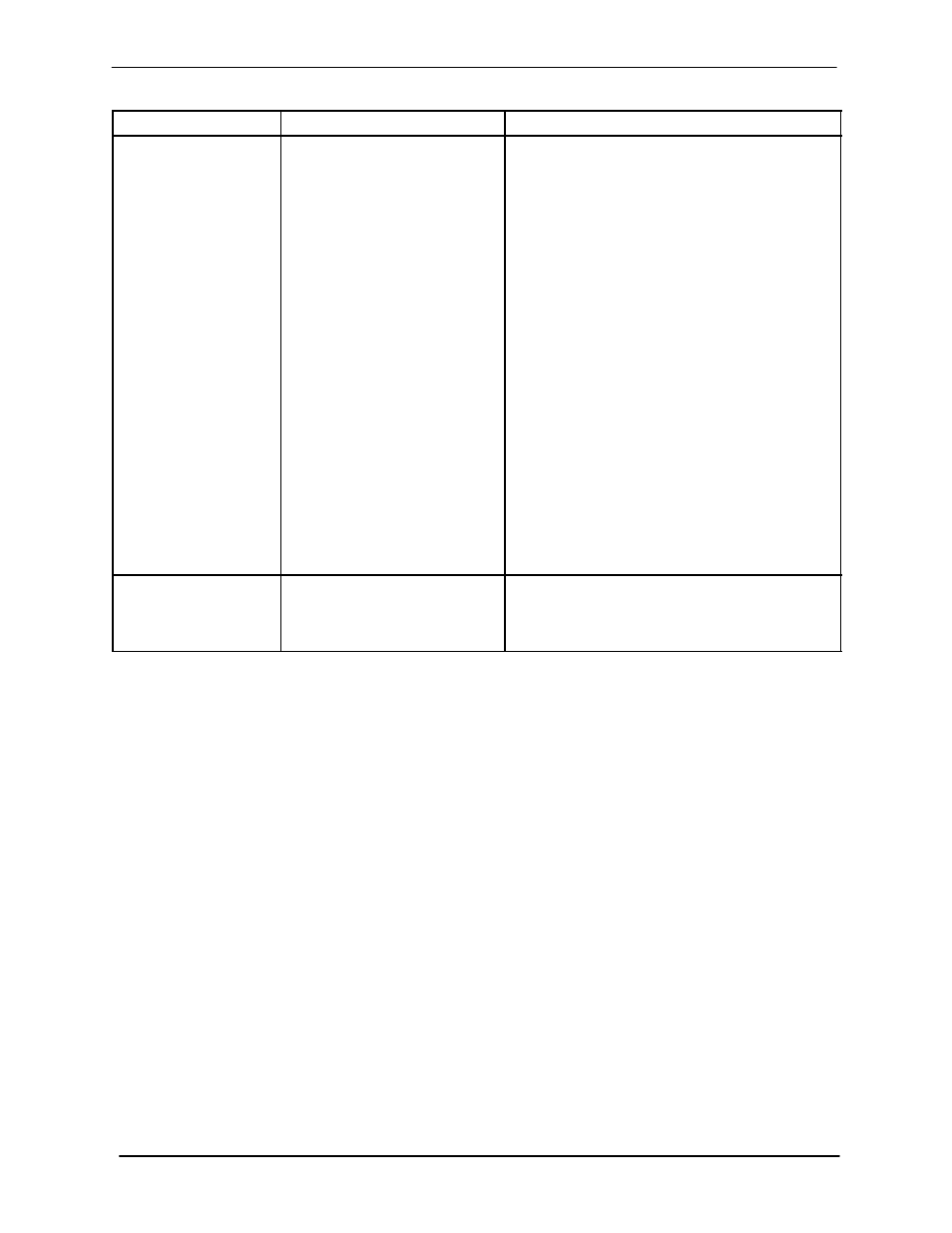
OM--05171
60 SERIES
TROUBLESHOOTING
PAGE D -- 2
Table B-1 Troubleshooting Chart (continued)
TROUBLE
CAUSE
REMEDY
PUMP STOPS OR
FAILS TO DELIVER
RATED FLOW OR
PRESSURE
Air leak in suction line.
Suction intake not submerged
at proper level or sump too
small.
Lining of suction hose col-
lapsed.
Discharge line clogged or re-
stricted; hose kinked.
Impeller or other wearing parts
worn or damaged.
Impeller clogged.
Pump speed too slow.
Suction lift or discharge head
to high.
Leaking or worn seal or pump
gasket.
Correct leak.
Check installation and correct submergence as
needed.
Replace suction hose.
Check discharge lines; straighten hose.
Replace worn or damaged parts. Check that
impeller is properly centered and rotates freely.
Free impeller of debris.
Check engine output; consult engine operation
manual.
Check piping installation and reduce suction lift
and/or discharge head.
Check pump vacuum. Replace leaking or worn
seal or gasket.
PUMP REQUIRES
TOO MUCH POWER
Exceeding operating limits.
Liquid solution too thick.
See performance curve in Pump Maintenance
And Repair.
Dilute if possible.
PREVENTIVE MAINTENANCE
Since pump applications are seldom identical, and
pump wear is directly affected by such things as
the abrasive qualities, pressure and temperature
of the liquid being pumped, this section is intended
only to provide general recommendations and
practices for preventive maintenance. Regardless
of the application however, following a routine pre-
ventive maintenance schedule will help assure
trouble-free performance and long life from your
Gorman-Rupp pump. For specific questions con-
cerning your application, contact your Gorman-
Rupp distributor or the Gorman-Rupp Company.
Record keeping is an essential component of a
good preventive maintenance program. Changes
in suction and discharge gauge readings (if so
equipped) between regularly scheduled inspec-
tions can indicate problems that can be corrected
before system damage or catastrophic failure oc-
curs. The appearance of wearing parts should also
be documented at each inspection for comparison
as well. Also, if records indicate that a certain part
(such as the seal) fails at approximately the same
duty cycle, the part can be checked and replaced
before failure occurs, reducing unscheduled down
time.
For new applications, a first inspection of wearing
parts at 250 hours will give insight into the wear rate
for your particular application. Subsequent inspec-
tions should be performed at the intervals shown
on the chart below. Critical applications should be
inspected more frequently.