Discharge lines – Gorman-Rupp Pumps 04B3-F4L 1242057 thru 1316965 User Manual
Page 12
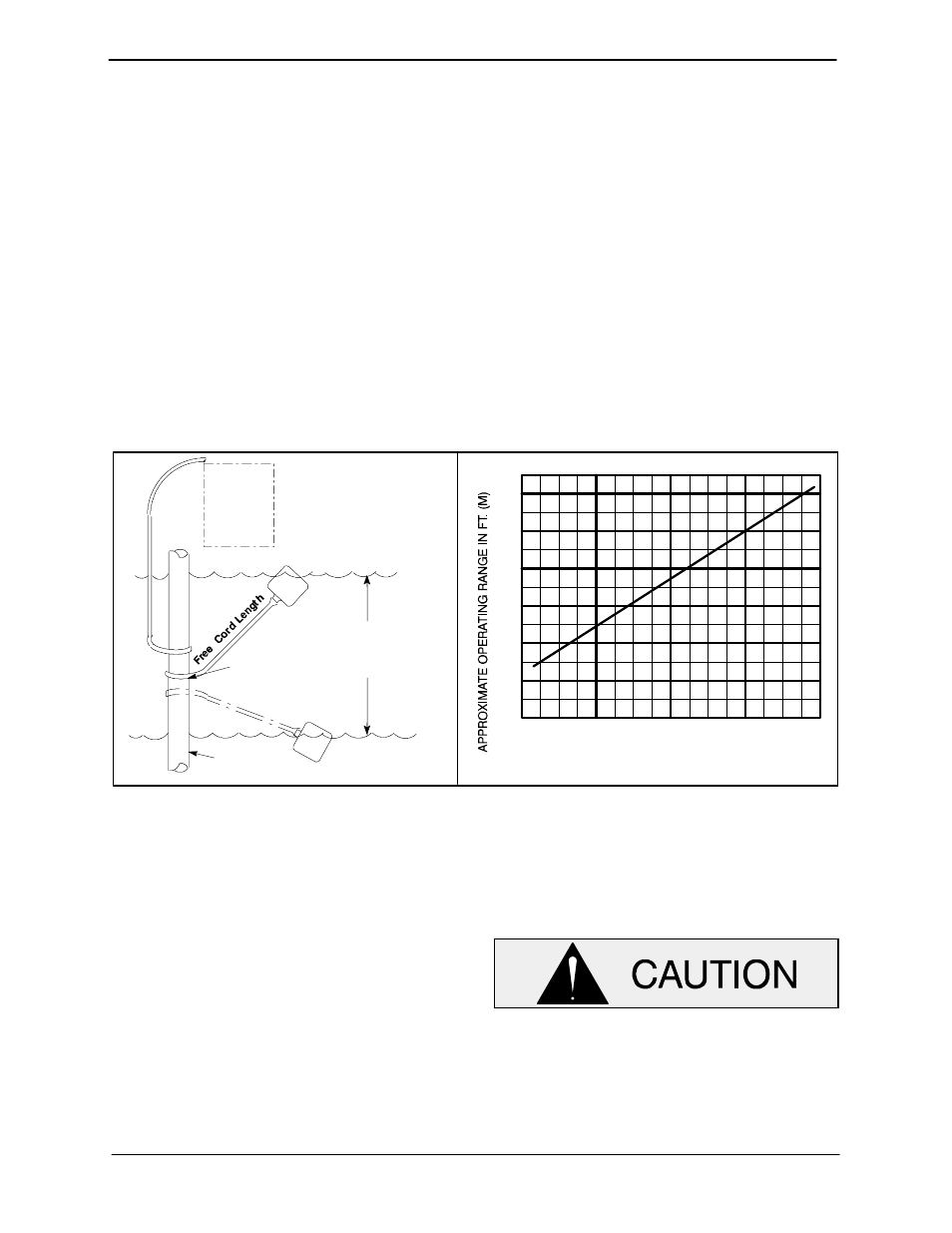
0 SERIES
OM--01216
PAGE B -- 5
INSTALLATION
Standard floats are equipped with 50 feet (15,2 m)
of cable.
When installing the floats, note the following:
a.
Be sure to provide sufficient room in the wet
well or sump so that floats do not get ob-
structed or drawn into the suction line. If a flex-
ible suction hose is used, it may be extended
to lay along the bottom of the wet well or sump
and the float can be attached to the hose
above the point where it bends along the bot-
tom. Direct the suction line toward the flow,
and the float(s) away from the flow. If a stand-
pipe is available, attach the float switch cable
to the standpipe in the sump at the approxi-
mate desired liquid level.
b. In a single float system, the cable can be teth-
ered to the suction line or standpipe approxi-
mately 6 inches (152 mm) above the float.
This setting allows approximately 9 inches
(229 mm) of liquid rise between pump start/
stop. The start/stop interval may be increased
by extending the float end of the cable. The
liquid level in the sump will increase approxi-
mately 8 inches (203 mm) between start/stop
intervals for every 6 inches (152 mm) of cable
increase.
c. If a double float switch system is used, posi-
tion the “Start” float at the desired high water
level in the sump, and the “Stop” float at the
desired low water level in the pump.
d. Refer to Figure 3 for additional float switch
data.
OPERATING
RANGE
(See Table Below)
CABLE
TETHER
POINT
OFF
(Emptying)
ON
(Filling)
ON
(Emptying)
OFF
(Filling)
1.25” Pipe
(Not Furnished)
ENGINE
CONTROL
BOX
1.0
(0.3)
APPROXIMATE FREE CORD LENGTH IN FT. (M)
0.5
(.15)
1.0
(0.3)
1.5
(.46)
2.0
(0.6)
2.5
(.76)
3.0
(0.9)
2.0
(0.6)
3.0
(0.9)
4.0
(1.2)
Figure 3. Float Switch Data
DISCHARGE LINES
Siphoning
Do not terminate the discharge line at a level lower
than that of the liquid being pumped unless a si-
phon breaker is used in the line. Otherwise, a si-
phoning action causing damage to the pump
could result.
Valves
If a throttling valve is desired in the discharge line,
use a valve as large as the largest pipe to minimize
friction losses. Never install a throttling valve in a
suction line.
With high discharge heads, it is recommended that
a throttling valve and a system check valve be in-
stalled in the discharge line to protect the pump
from excessive shock pressure and reverse rota-
tion when it is stopped.
If the application involves a high discharge
head, gradually close the discharge
throttling valve before stopping the pump.
Bypass Lines
If a system check valve is used due to high dis-
charge head, it may be necessary to vent trapped