Gorman-Rupp Pumps 06C1-GHH 1071445 and up User Manual
Page 46
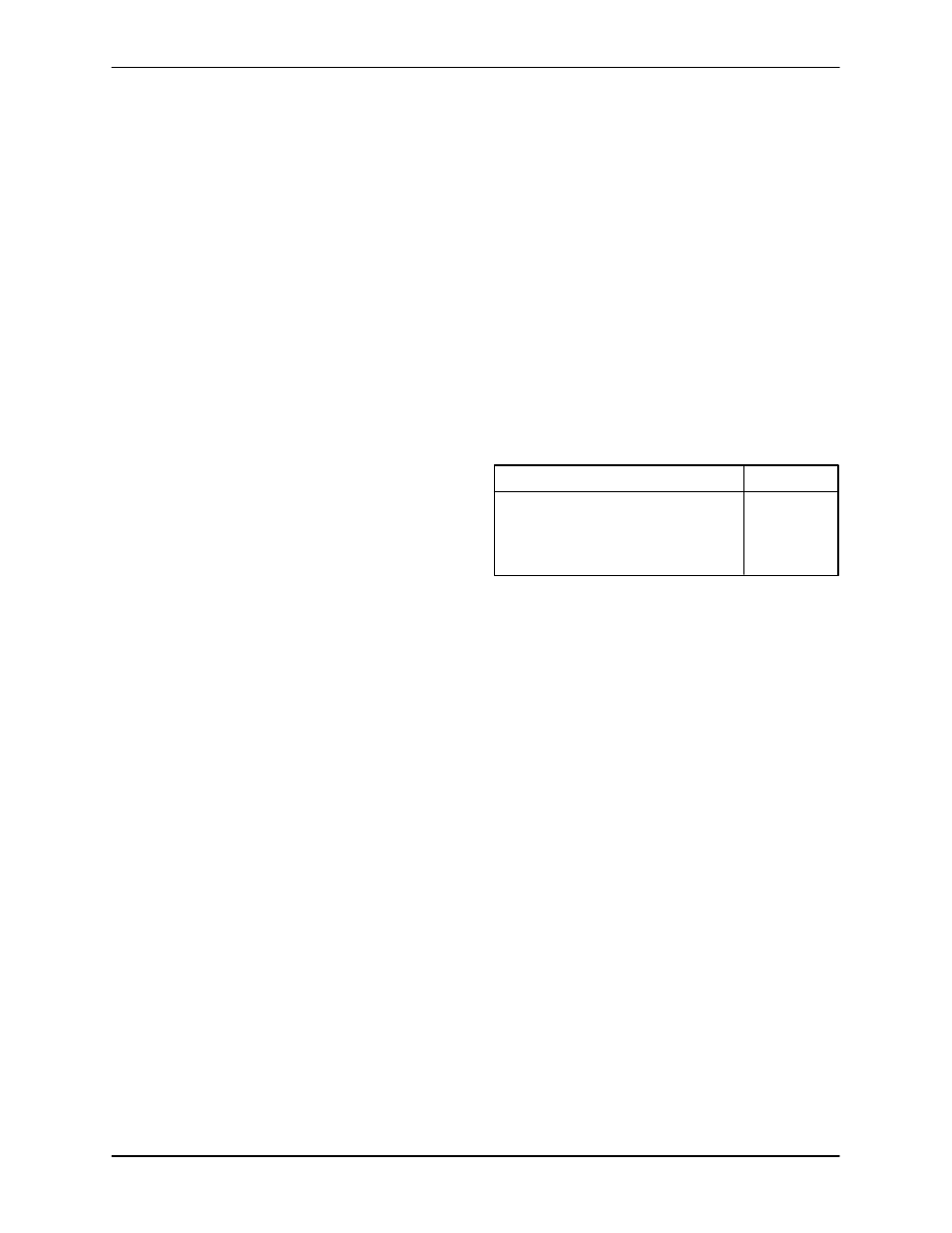
OM-03179
0 SERIES
MAINTENANCE & REPAIR
PAGE E - 21
Use filtered compressed air to pressurize the gear
box until it stabilizes at 6 psi (0,4 kg/cm
@), then shut
off the air flow and observe the pressure gauge. If
the pressure drops more than 1 psi (0,07 kg/cm
@)
in 15 seconds, an unacceptable air leak exists at
one of the sealing surfaces.
To find the leak, repressurize the gearbox, and ap
ply a liberal amount of commercially available win
dow cleaner or liquid detergent to each sealing
surface. Watch for air bubbles to appear indicating
a leak. Correct any leaks that are found, and retest
the gearbox.
Drive Flange Installation
The shaft splines are designed to produce a slight
interference fit with the drive flanges. This fit is re
quired to prevent fretting corrosion.
Coat the input and output shaft splines with light
oil. Apply oil to the leading area of the drive flanges
where the oil seal lips seat. Position the input and
output flanges on their respective shafts.
It is recommended that a sleeve be used to drive
the flanges onto the shaft until fully seated. The
sleeve must be sized to fit over the shaft and into
the flange counterbore.
After the flanges have been installed, secure them
to the shafts with the capscrews and lockplate
washers; torque the capscrews to 90 ft. lbs. (1080
in. lbs. or 12,4 m. kg.).
Lubricate the gearbox as indicated in LUBRICA
TION at the end of this section. Install the pump
and gearbox assembly onto the vehicle as de
scribed in Installing Pump and Gearbox at the
end of PUMP AND SEAL REASSEMBLY.
LUBRICATION
Seal Assembly
The seal assembly is lubricated by the liquid being
pumped. No additional lubrication is required.
Trunnion Bracket
(Figure 1)
To lubricate the trunnion (11) and bearing retainer,
add SAE No. 2 lithium‐based pressure gun grease
through the lubrication fitting (12) until grease es
capes from the trunnion area.
Gearbox Assembly
(Figure 2A)
The gearbox was shipped from the factory dry of
lubrication, except for a residual coating from the
testing process of 90 weight gear oil and Dow
Corning “Molykote
R M Gear Guard” (an anti‐wear
additive consisting of molybdenum disulphide sol
id lubricants suspended in petroleum oil). For initial
lubrication of the gearbox, remove the oil level plug
(67), and add approximately 68 U.S. ounces (2011
ml) of premium quality, multi‐purpose, extreme
pressure gear lubricant with an SAE rating per the
following ambient temperatures.
Table 1. Lubrication Specifications
Temperature Range
Lubricant
-40
_
F (-53
_
C) to 0
_
F (-018
_
C)
Delvac I
-10
_
F (-23
_
C) to +40
_
F (+4
_
C)
80 W 90
+32
_
F (0
_
C) and above
80 W 140
Fill the gearbox to the bottom of the fill plug hole as
indicated on the oil level plate. If the gearbox is ov
er‐filled, foaming may occur with oil loss through
the breather vent during continuous duty opera
tion. Under‐filling can result in loss of lubrication to
the tailshaft bearing, resulting in premature bear
ing failure. Check the lubricant level regularly, and
maintain it at the recommended level. Reinstall the
oil level plug.
Intermittent (Normal Refueler) Duty Cycle
Change the lubricant in a new gearbox after an ini
tial break‐in period of 24 hours, and before 100
hours of operation. The lubricant should be
changed while the pump is at operating tempera
ture.
To change the lubricant, remove the magnetic
drain plug and gasket (65 and 66), and drain the
gearbox. If operating conditions require changing
grades of oil to Delvac I, it is recommended that the
gearbox be thoroughly flushed with flushing oil
prior to refilling. Always clean the magnetic plug
thoroughly before reinstalling it. Add 6 ounces (18
ml) of Dow Corning “Molykote
R M Gear Guard”,
and “top off” with approximately 68 U.S. ounces (2
liters) of oil as previously described.