Vii. maintenance, Viii. operation – Xylem IM226R02 CP-Series Submersible Motors User Manual
Page 15
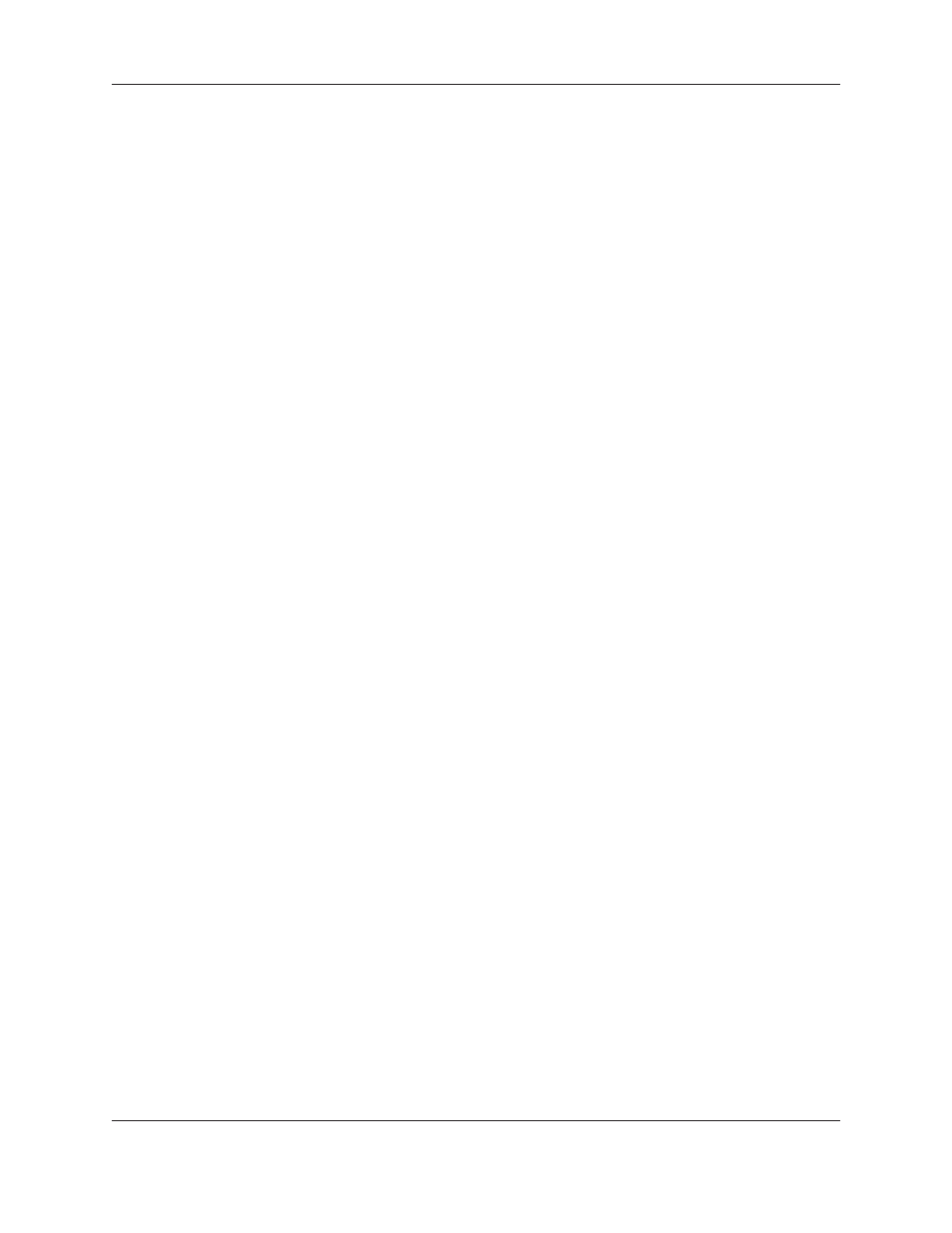
CP-Series Submersible Motors Installation, Operation and Maintenance Manual
13
D. The lead arrangement of the motor is acceptable with the proposed starter load connections.
E. Verify that if any time delay relays are used in switching contactors in and out, that the time settings are
not too long; this could damage the motor.
F. If a manual auto transformer starter is used, don't wait too long to go into the "Run" condition and don't
"tease" the contacts. Double check Tables 1 - 4 for correct protection.
17. Do not expose motor leads to air. Leads must be submerged for cooling.
VII. Maintenance
There are no bearings that need oil or grease. The motor, being inaccessible, should be monitored through its
electrical connections.
1. Measure and record operating current and voltage.
2. Measure and record the motor insulation resistance. Any resistance of less than 5 megohm (5,000,000) for a
new motor should be evaluated or checked further by a qualified service shop.
3. Lightning arrestors and/or surge capacitors will help prevent damage to the control box, cables and motor.
4. Single phase protection will help in preventing motor failure due to adverse incoming primary power.
5. Based on the values obtained in 1 and 2 above and the output flow rates and pressures of the pump, a
complete picture of total performance can be obtained. This can be used to determine any pump and motor
maintenance and overhauling which might be required.
6. If the motor is to be stored, protect the unit from freezing by storing in an area with a temperature
higher than -30º C (-22º F).
VIII. Operation
1. After energizing the motor, check the flow and pressure of the pump to make sure that the motor is
rotating in the correct direction. To correct a wrong rotation, switch any two of the three cable connections.
(Three phase motor only.)
2. When starting the pump for the first time, inspect the water for sand. If sand appears, then continue to
pump until the water clears up; otherwise, sand will accumulate in the pump stages and will bind or freeze
the moving parts if water is allowed to flow back down the well.
3. During testing or checking rotation (such as "bumping" or "inching") the number of "starts" should be
limited to 3, followed by a full 15 minute cooling-off period before any additional "starts" are attempted.
Depending on the depth of the well and/or method of checking, these rotational checks or "starts" may
actually be full-fledged starts. If this is the case, then a full cooling-off
period of 15 minutes is required between this type of start.
4. For automatic (pilot device) operation, the motor should be allowed to cool for 15 minutes
between starts.
5. Input voltage, current and insulation resistance values should be recorded throughout the life of the
installation and should be used as a form of preventive maintenance.
6. Maximum number of starts per hour:
6”: 15 starts/hour
8”: 10 starts/hour
10”: 8 starts/hour
12”: 4 starts/hour
Pre-Installation (continued), Maintenance and Operation