Pam2804, Application information – Diodes PAM2804 User Manual
Page 6
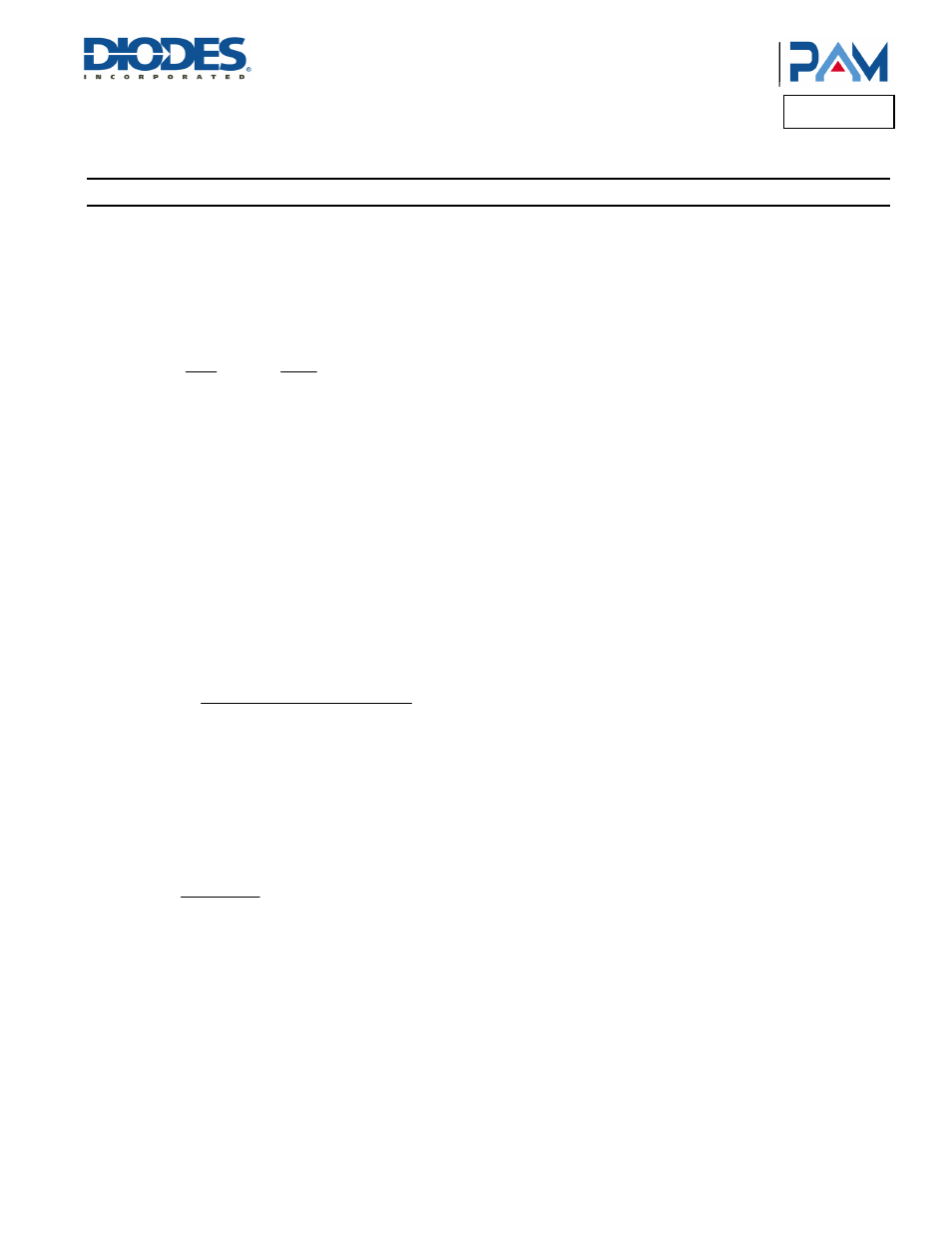
PAM2804
Document number: DSxxxxx Rev. 2 - 0
6 of 10
January 2013
© Diodes Incorporated
PAM2804
A Product Line of
Diodes Incorporated
Application Information
The basic PAM2804 application circuit is shown in Page 1. External component selection is determined by the load requirement, selecting L first
and then C
IN
and C
OUT
.
Inductor Selection
For most applications, the value of the inductor will fall in the range of 1μH to 4.7μH. Its value is chosen based on the desired ripple current.
Large value inductors lower ripple current and small value inductors result in higher ripple currents. Higher V
IN
or V
OUT
also increases the ripple
current as shown in equation 1. A reasonable starting point for setting ripple current is ΔI
L
= 400mA (40% of 1A).
( )( )
⎟⎟
⎠
⎞
⎜⎜
⎝
⎛
−
=
Δ
V
V
1
V
L
f
1
I
IN
OUT
OUT
L
Equation (1)
The DC current rating of the inductor should be at least equal to the maximum load current plus half the ripple current to prevent core saturation.
Thus, a 1.4A rated inductor should be enough for most applications (1A + 400mA). For better efficiency, choose a low DC-resistance inductor.
Using Ceramic Input Output Capacitors
Higher values, lower cost ceramic capacitors are now becoming available in smaller case sizes. Their high ripple current, high voltage rating and
low ESR make them ideal for switching regulator applications. Using ceramic capacitors can achieve very low output ripple and small circuit size.
When choosing the input and output ceramic capacitors, choose the X5R or X7R dielectric formulations. These dielectrics have the best
temperature and voltage characteristics of all the ceramics for a given value and size.
Thermal Consideration
Thermal protection limits power dissipation in the PAM2804. When the junction temperature exceeds +150°C, the OTP (Over Temperature
Protection) starts the thermal shutdown and turns the pass transistor off. The pass transistor resumes operation after the junction temperature
drops below +120°C.
For continuous operation, the junction temperature should be maintained below +125°C. The power dissipation is defined as:
(
)
(
)
V
I
I
F
t
V
R
V
V
R
V
I
P
IN
Q
O
S
SW
IN
L
)
ON
(
DS
O
IN
H
)
ON
(
DS
O
2
O
D
+
+
−
+
=
I
Q
is the step-down converter quiescent current. The term tsw is used to estimate the full load step-down converter switching losses.
For the condition where the step-down converter is in dropout at 100% duty cycle, the total device dissipation reduces to:
V
I
R
I
P
IN
Q
H
)
ON
(
DS
2
O
D
+
=
Since R
DS(ON)
, quiescent current, and switching losses all vary with input voltage, the total losses should be investigated over the complete input
voltage range. The maximum power dissipation depends on the thermal resistance of IC package, PCB layout, the rate of surrounding airflow
and temperature difference between junction and ambient. The maximum power dissipation can be calculated by the following formula:
θ
−
=
JA
A
)
MAX
(
J
D
T
T
P
Where T
J(MAX)
is the maximum allowable junction temperature +125°C. T
A
is the ambient temperature and θ
JA
is the thermal resistance from the
junction to the ambient. Based on the standard JEDEC for a two layers thermal test board, the thermal resistance θ
JA
of TSOT25 package is
250°C/W. The maximum power dissipation at T
A
= +25°C can be calculated by following formula:
(
)
W
4
.
0
W
/
C
250
/
C
25
C
125
P
D
=
°
°
−
°
=