Theatre Solution Prima Auditorium Seating User Manual
Page 21
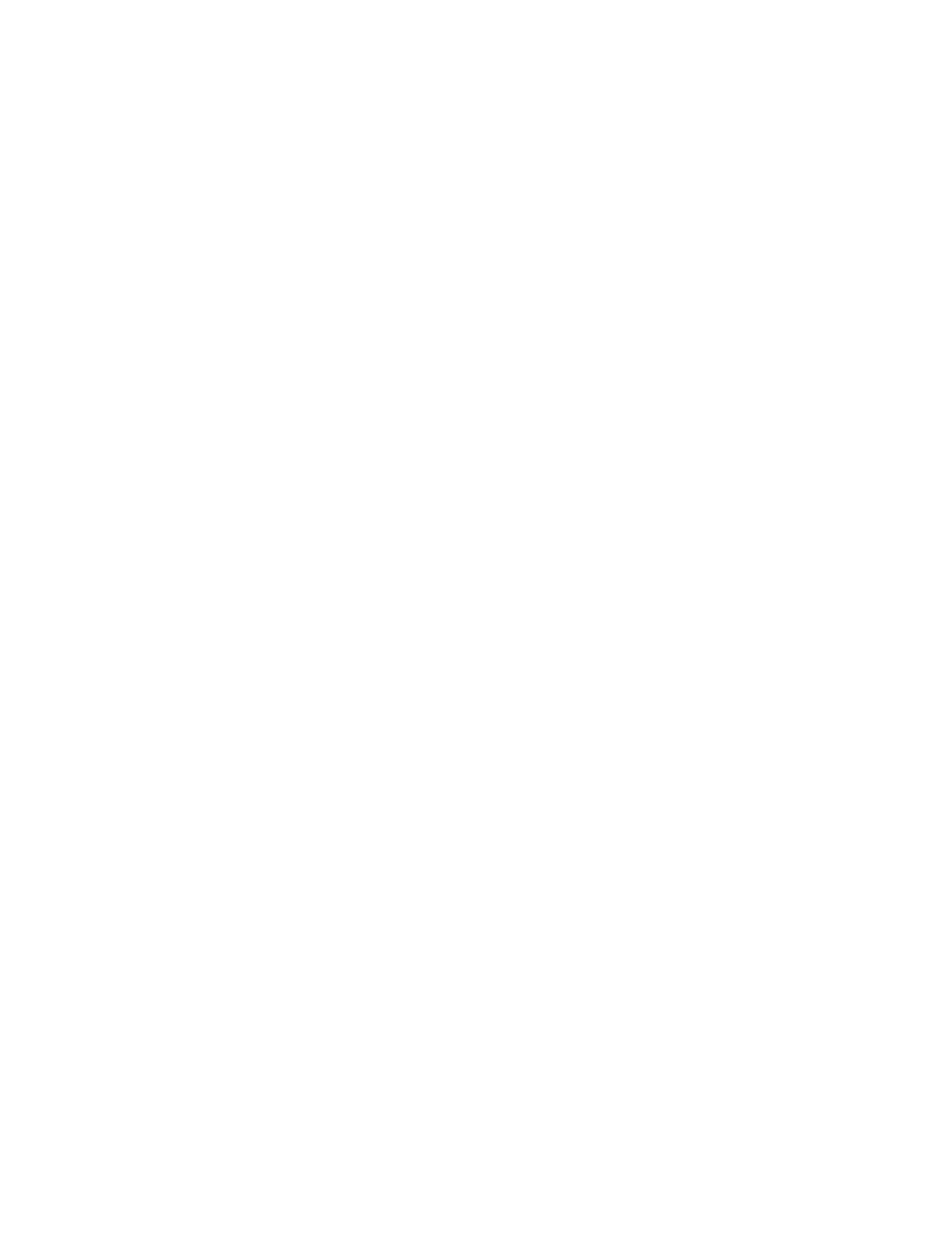
20
Specifications Prima Auditorium Seating
D. All leg panels shall include a plinth base of seasoned maple hardwood fitted with 1/4-20 threaded inserts
for assembly of floor attachment hardware.
2.6 UPHOLSTERED SEATS/BACKS
A. General: Fabricate theater seating with padding and fabric covering. Equip each seat with a gravity self-
rising mechanism so that unoccupied seats return to an upright position perpendicular to the base line of
floor of auditorium. Spring compensating mechanism will not be acceptable. Chair profile with the seat in
the upright position cannot exceed 20-13/16”.
B. Seat Construction: Solid seat bottom construction comprised of a plywood veneer outer panel fastened
solidly and without voids to an inner structural plywood panel. The outer panel shall be 3/4” thick, faced
one side with Grade A veneer centered across the width of the panel, and exposed plywood laminations
along all edges. The inner panel shall be 3/4” thick. Both shall be electronically glued hardwood plywood
and shall be fastened together with bayonet hanging brackets at the top and two steel angles at the bottom,
resulting in a rigid connection with no visible fasteners. The veneer face and edges of the outer panel shall
be stained to match the architect’s sample. The polyurethane foam padding material shall be two-ply and
shall consist of 2” thick 55 lb. ILD and 1” thick 45 lb. ILD, shall be glued to the inner panel, and shall
conform to the California Bureau of Home Furnishings Technical Bulletin 117. The complete seat
assembly shall be supported by two 7 gauge formed steel mounting brackets which will attach the seat
assembly to the hinges on the leg panels. The seat shall have a built-in counterweight to insure automatic
self-rising without the aid of springs. Arch-spring seat construction will not be acceptable.
C. Back Construction: Solid back construction comprised of a plywood veneer outer panel, one inner lumbar
plywood panel, and one inner shoulder plywood panel. The outer panel shall be 3/4” thick, faced one side
with Grade A veneer centered across the width of the panel, and exposed plywood laminations along all
edges. The inner panels shall be 1/2” thick. Plywood panels shall be electronically glued hardwood
plywood. Inner panels shall be fastened to the outer panel with four bayonet hanging brackets at the top
and four 16 gauge flat steel brackets using four #8 x 1/2” pan head sheet metal screws at the bottom,
resulting in a rigid connection with no visible fasteners. The veneer face and edges of the outer panel shall
be stained to match the architect’s sample. The padding material on the shoulder cushion shall be 1-1/2”
thick polyurethane foam; the padding material on the lumbar cushion shall be 2” thick. All padding shall be
glued to the inner panel, and shall conform to the California Bureau of Home Furnishings Technical Bulletin
117. The outer panel shall contain six 1/4-20 threaded inserts and shall be assembled to the leg panels
with two 11 gauge steel angle brackets.
D. Hinge: The seat hinge shall be a weldment consisting of a 7 gauge hot-rolled pickled-in-oil steel component
and shall be formed and punched to receive a 0.56” id x 0.75” od x 0.5” long steel bushing. A self-
lubricating nylon sleeve shall be fitted between the seat hinge and the standard seat hinge pin. The hinge
shall be machined to provide a positive stop location for the seat in both occupied and unoccupied
positions. The hinge shall be fitted with a plastic cover to eliminate all pinch points and shall include a
3/16” thick urethane rubber pad to dampen noise upon the seat return to the vertical position.