Lyric d4 specifications – theatre seating – Theatre Solution Lyric D4 User Manual
Page 3
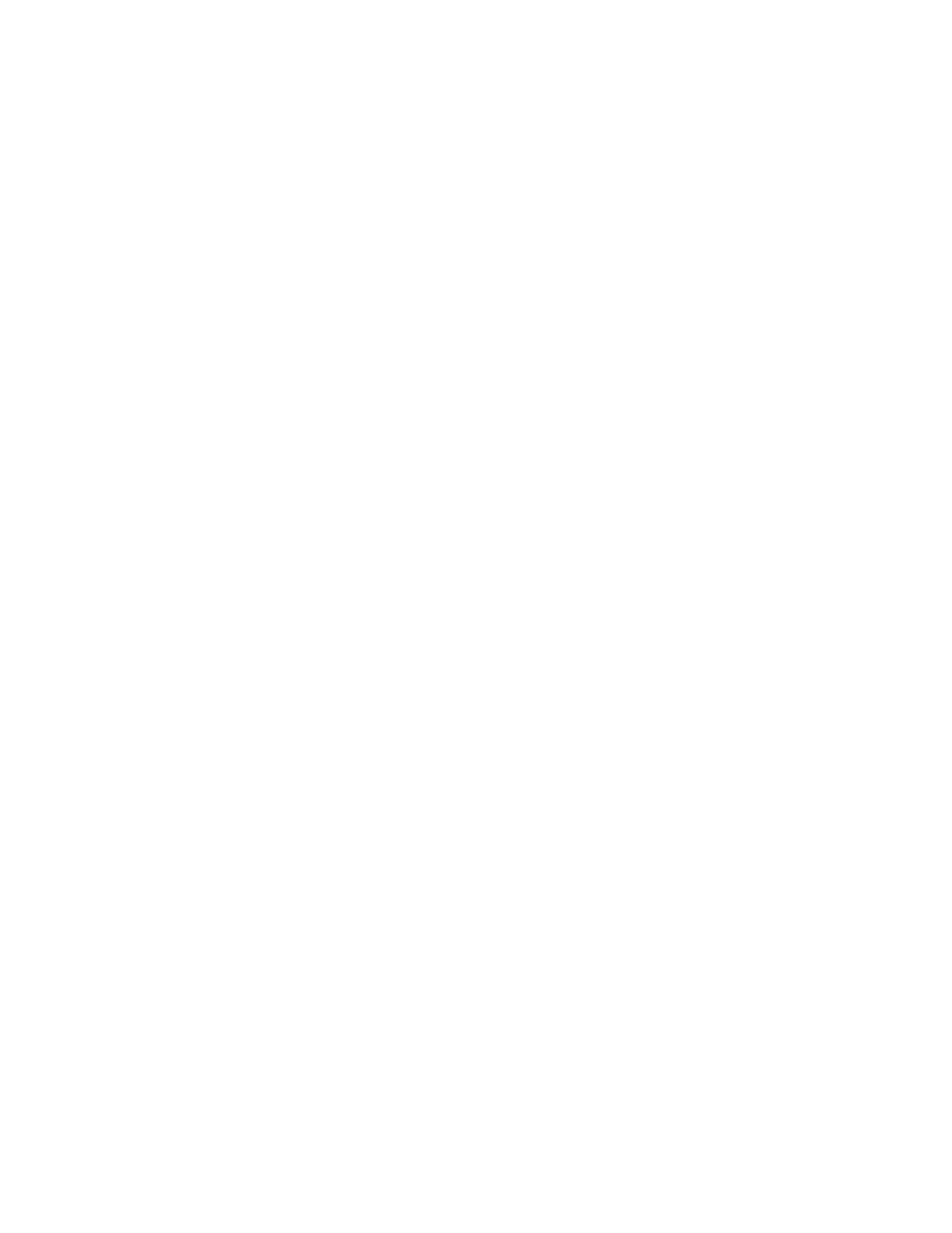
Lyric D4 Specifications – Theatre Seating
Page 3 of 5
Foam shall be fire retardant and conform to the California Bureau of Home Furnishings Technical Bulletin
117. The upholstery cover shall be sewn and fitted to the seat assembly with collapsible assembly rings
and nylon tension cord.
The outer injection-molded seat cover and upholstered inner seat assembly shall be joined together with
cast aluminum mounting brackets. Seat widths of 19” and 21” shall be fitted with narrow style mounting
brackets. Seat widths of 20” and 22” shall be fitted with width-extending mounting brackets. The complete
seat assembly shall be assembled to the seat hinges using (2) special purpose M10 Hinge Bolts and (2)
special purpose M10 Hinge Pins which are specifically designed to accommodate installation tolerances.
C.
Back Construction: Back construction is comprised of an injection-molded polypropylene cover fastened
securely to an inner upholstered structural steel frame assembly. The outer back cover shall have a
textured exterior surface and internal molded reinforcing ribs for a solid warp-free construction. The inner
back frame assembly shall consist of a 7/8” dia. X 16 gauge steel tube formed into an ergonomically
derived radius and welded into a rigid assembly with (2) 11 gauge X 1” steel brackets and (3) 1/4” diameter
steel rods. A series of (5) 2” wide elastic suspension straps shall be stretched and woven in place and
fastened to the steel seat frame with 1/8” dia. steel hooks. Arch-spring and/or S-spring construction will not
be acceptable. A layer of 1 1/4” thick molded polyurethane foam shall be applied over the elastic webbing.
Foam shall be fire retardant and conform to the California Bureau of Home Furnishings Technical Bulletin
117. The upholstery cover shall be sewn and fitted to the seat assembly with collapsible assembly rings
and nylon tension cord.
The outer injection-molded back cover and upholstered inner back assembly shall be joined together with
cast aluminum mounting brackets. Back widths of 19” and 21” shall be fitted with 3/8” thick mounting
brackets. Back widths of 20” and 22” shall be fitted with 7/8” thick mounting brackets. The complete back
assembly shall be supported by two 13 gauge formed steel brackets and two 3/8-16 hex head bolts and
shall be attached to the frame with (2) 1/4-20 machine screws.
D.
Armrests: Shall be blow-molded high density polyethylene and curved to match the leg mounting plate.
The armrest will be fastened to the steel frame arm support with three #8 sheet metal screws.
E.
Hinge: Shall be injection-molded of DuPont™ Zytel
®
801 nylon. The hinge shall be molded with
provisions to provide positive stop locations for the seat in both occupied and unoccupied positions. The
hinge shall be fitted with a plastic cover to eliminate all pinch points and shall include (2) 7/16” thick
urethane rubber pads to dampen noise upon the seat stop in both the vertical and horizontal positions.
Note: Dupont™ and Zytel
®
are registered trademarks of E.I.du Pont de Nemours and Co. or its affiliates
PART 3 – OPTIONS
3.1 VENEER
END
PANEL
A. Provide manufacturer’s standard end panel at the end of the row. The configuration of the panel shall
follow the angle of the frame and back at the rear, and shall be vertical at the front edge. The panel shall
be constructed of 3/4” thick plywood with veneer on both sides and 1/8” thick solid wood on the vertical
edges. The end panel shall be stained to match the outer wood seat, back, and armrests.
3.2 POWDER-COATED END PANEL
A. Provide manufacturer’s standard end panel at the end of the row. The configuration of the panel shall
follow the angle of the frame and back at the rear, and shall be vertical at the front edge. The panel shall
be constructed of 3/4” thick medium density fiberboard with a durable powder-coated black finish.
3.3 AISLE LIGHT
A. Aisle lights shall be provided in accordance to the locations shown on the architectural drawings. The
units shall be of low voltage (24v) type and the light tube shall fit into a recessed area on the underside of
the armrest. The chair frame shall be prepared to accept the power wire. The necessary access holes
and blank cover plates shall be provided. The chair manufacturer shall also provide the necessary
transformers. All wiring and electrical connections shall be conducted at the job site and shall be the
responsibility of others.
3.4 SEAT
IDENTIFICATION
TAGS
A. Provide manufacturer’s standard shape polycarbonate number plates. Font shall be Times Roman. The
number plates shall fit into a recessed area at the top edge of the seat and shall be adhered with high-
strength pressure-sensitive tape.
3.5 ROW IDENTIFICATION AND DONOR TAGS
A. Provide manufacturer’s standard shape polycarbonate letter plates. Font shall be Times Roman.