Lyric d4 specifications – theatre seating – Theatre Solution Lyric D4 User Manual
Page 2
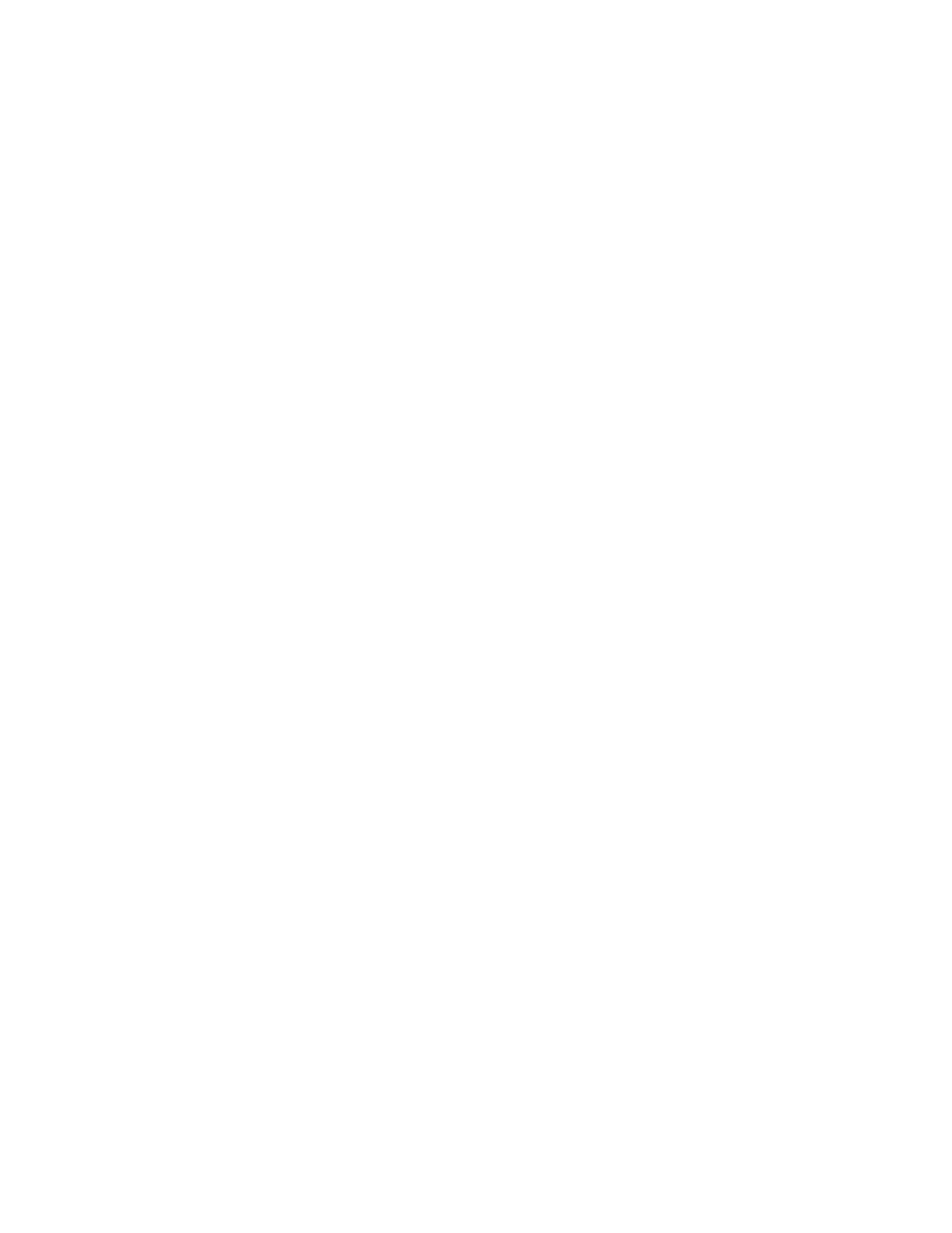
Lyric D4 Specifications – Theatre Seating
Page 2 of 5
2.
Inner upholstered seat and back
3.
Outer injection-molded plastic back cover
4.
Outer injection-molded plastic seat cover
5.
Blow-molded
plastic
armrests
6.
Aisle lights where indicated on the drawings
7.
End panels where indicated on the drawings
B.
Model noted is based on the Theatre Solutions, Inc. Lyric “D4” model with the intent of establishing the
high level of quality required for the project. Other brands submitted for approval will be given
consideration provided that a full seating mock-up, along with a complete list of specification discrepancies
between the proposed substitution and the product specified is received at least 10 working days prior to
the bid date.
1. By offering a quote for this project, the bidder assumes full responsibility for complying with the
specifications for this project and shall be totally responsible for any expenses incurred if the
product quoted does not comply with the specifications.
C.
Failure to comply with the warranty described in Part 4 of these specifications will be cause for
disqualification.
2.2 MATERIALS
A. Padding material shall be high resiliency polyurethane foam which conforms to the standards of the
California Bureau of Home Furnishings 117-75. The back shall be 1 1/4” thick. The seat shall be 1 3/4”
thick.
B.
Seating fabric shall be _______________________________________________ with the color to be
selected from the standard choice of colors. All upholstery shall be first quality without creases, stretch
lines, or wrinkles.
C. The arms shall be blow-molded of high-density polyethylene.
2.3 FABRICATION,
GENERAL
A. Fabricate the theater seating in contoured form for maximum comfort using materials that are carefully
selected to be free from defects, objectionable projections, or irregularities. Insure smooth round corners
and edges to present the least possible snagging and pinching hazards.
2.4 MOUNTING
A. Fabricate seating units for floor attachment, using standards that have been manufactured to conform to
the slope of the floor while maintaining seat and back in same angular relationship to standards
throughout.
2.5 METAL
STANDARDS
A. Frame shall be 3/4” x 2” x 16 gauge cold-rolled welded steel tubing; 1/4” x 3 1/2” hot-rolled steel plate, 1/4”
x 2 1/8” hot-rolled steel plate and 11 gauge formed steel brackets welded into one integral freestanding
structure upon which the seat, back, and arms are assembled. Pivot and stop pins shall be machined from
cold-finished steel to tolerances of +0.000 -0.005. Floor mount plate shall be .100” thick hot-rolled pickled-
in-oil steel formed and embossed for 1/4” mounting anchors. A molded plastic cap shall be fitted into the
embossed mounting area to conceal the anchoring hardware. Exposed floor anchoring hardware will not
be acceptable.
2.6 UPHOLSTERED
CHAIRS
A. General: Fabricate theater seating with padding, fabric covering and injection-molded seat and back
covers. Equip each seat with a gravity self-rising mechanism so that unoccupied seats return to an upright
position perpendicular to the base line of floor of auditorium. Spring compensating mechanism will not be
acceptable. Chair profile with the seat in the upright position and without a tablet arm, cannot exceed 18”.
B.
Seat Construction: Seat construction is comprised of an injection-molded polypropylene cover fastened
securely to an inner upholstered structural steel frame assembly. The outer seat cover shall have a
textured exterior surface and internal molded reinforcing ribs for a solid warp-free construction. The inner
seat frame assembly shall consist of a 7/8” dia. X 16 gauge steel tube formed with a waterfall front edge
and welded into a rigid assembly with (2) 11 gauge X 1” steel brackets and (1) 1/4” diameter steel rod. The
seat frame shall be fitted with a cast iron counterweight to insure automatic self-rising without the aid of
springs. A series of (7) 2” wide elastic suspension straps shall be stretched and woven in place and
fastened to the steel seat frame with 1/8” dia. steel hooks. Arch-spring and/or S-spring construction will not
be acceptable. A layer of 1 3/4” thick molded polyurethane foam shall be applied over the elastic webbing.