Ironwood Electronics SG-MLF User Manual User Manual
Page 3
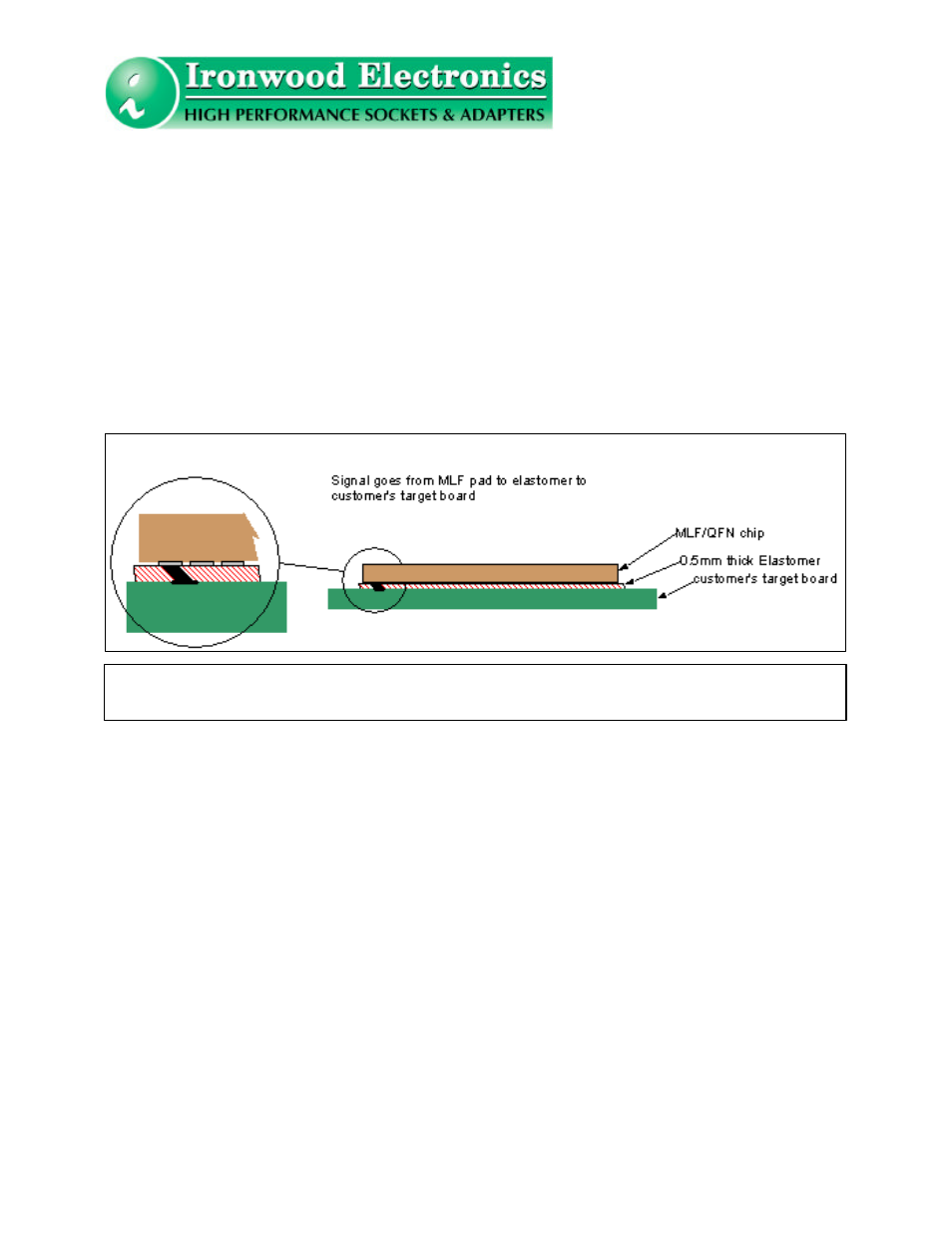
Rev A, JC, 5/12/03 Rev. C, JG, 5/25/07
Tel: (800) 404-0204 • (651) 452-8100
Fax: (651) 452-8400
PO Box 21151 • St. Paul, MN 55121 • USA
www.ironwoodelectronics.com
application consists of ultra fine pitch matrix (0.05mm x 0.05mm) of gold plated wires (20 micron
diameter), which are embedded at a 63-degree angle in a soft insulating sheet of silicone rubber.
The insulation resistance between connections with 500V DC is 1000 M
Ω
. It is ideal for high-
current (50mA per filament) applications where a thin, high-density anisotropic connector is
required. The gold-plated brass filaments protrude several microns from the top and bottom
surfaces of the silicone sheet. The operating temperature range for the elastomer is -35
°
to 85
°
C.
The solder pads from the IC package come in contact with the top end of the elastomer wire. The
bottom end of the elastomer wire contacts the PCB pad and thereby makes an electrical path for
the signal. Depending upon the solder pad and PCB pad dimensions, multiple wires can make
contact between them. Figure 3 shows the cross-sectional side view of the elastomer with an
example IC. The socket mechanism can be summarized as a downward force applied on the IC
which compresses solder pads onto the elastomer which in turn compresses onto the PCB and
thereby making the electrical connection.
PCB Requirements:
Please refer to page 2 of the socket drawing for all PCB recommendations.
GHz socket needs four mounting holes.
Two alignment holes are used in all sockets. One is 2.54mm (in most cases) below the upper right
mounting hole, and the other is 5.08mm (in most cases) above the lower left mounting hole. QFN
pattern is not symmetrical to those mounting holes and it is shifted half the elastomer
thickness (0.25mm in most cases) in the positive x-direction.
Thickness: 1.6mm minimum. This will change as per customer's application, environment and
usage.
Finish: SnPb plating or Immersion Au or Immersion Ag. Other plating may be used, but testing
may be required. Ideally pad surface is flush or higher than the solder mask, although solder mask
of 0.002” above pad surface is acceptable.
Cleanliness: Isopropyl Alcohol or similar should be used to clean the board surface prior to
attaching socket.
Figure 3: Elastomer cross-sectional side view