Rainbow Electronics MAX5081 User Manual
Page 12
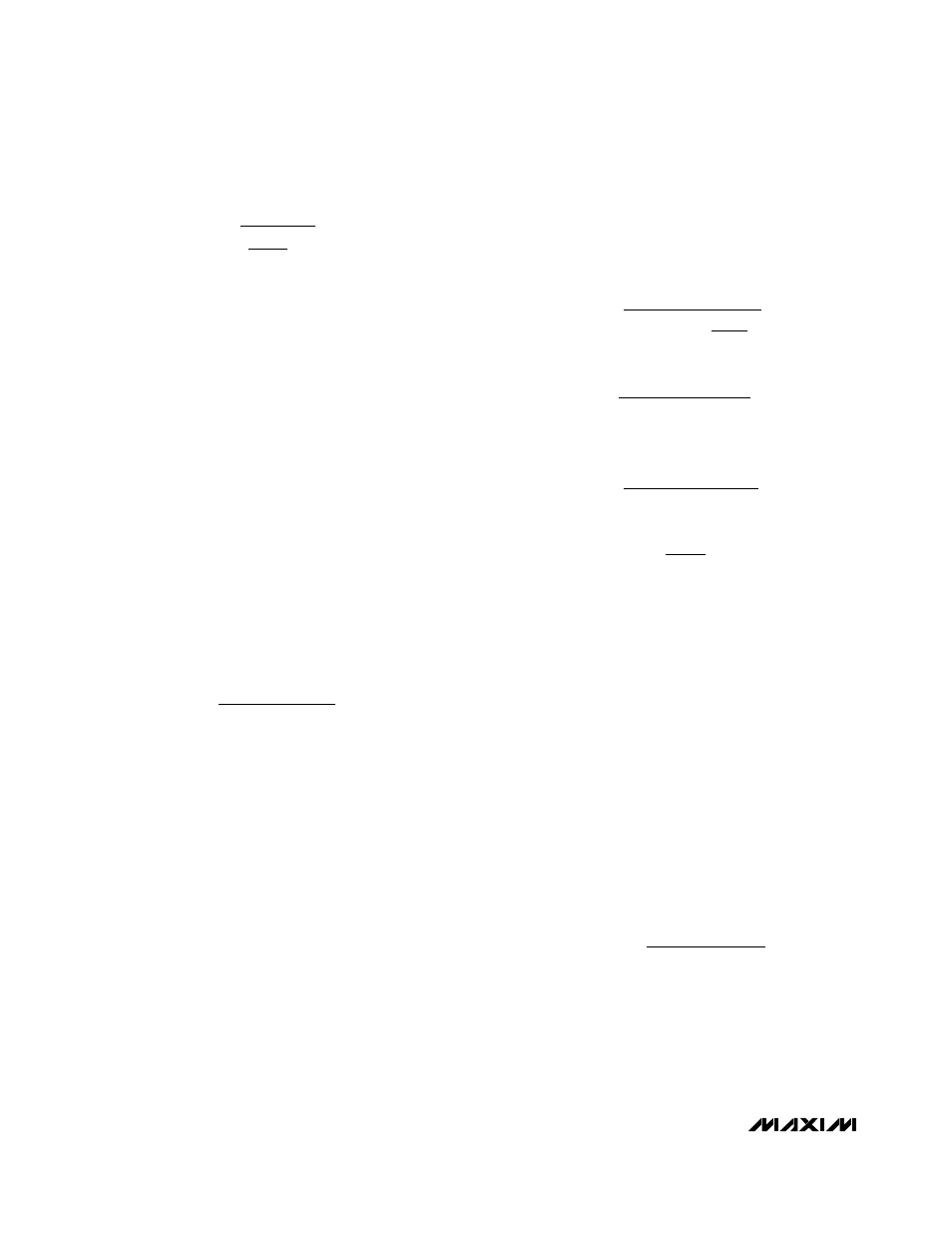
MAX5080/MAX5081
1A, 40V, MAXPower Step-Down
DC-DC Converters
12
______________________________________________________________________________________
where V
FB
= 1.23V.
Inductor Selection
Three key inductor parameters must be specified for
operation with the MAX5080/MAX5081: inductance
value (L), peak inductor current (I
PEAK
), and inductor
saturation current (I
SAT
). The minimum required induc-
tance is a function of operating frequency, input-to-out-
put voltage differential, and the peak-to-peak inductor
current (
∆I
P-P
). Higher
∆I
P-P
allows for a lower inductor
value while a lower
∆I
P-P
requires a higher inductor
value. A lower inductor value minimizes size and cost
and improves large-signal and transient response, but
reduces efficiency due to higher peak currents and
higher peak-to-peak output voltage ripple for the same
output capacitor. On the other hand, higher inductance
increases efficiency by reducing the ripple current.
Resistive losses due to extra wire turns can exceed the
benefit gained from lower ripple current levels especial-
ly when the inductance is increased without also allow-
ing for larger inductor dimensions. A good compromise
is to choose
∆I
P-P
equal to 40% of the full load current.
Calculate the inductor using the following equation:
V
IN
and V
OUT
are typical values so that efficiency is opti-
mum for typical conditions. The switching frequency (f
SW
)
is fixed at 250kHz or can vary between 150kHz and
350kHz when synchronized to an external clock (see the
Oscillator/Synchronization Input (SYNC) section). The
peak-to-peak inductor current, which reflects the peak-to-
peak output ripple, is worst at the maximum input voltage.
See the Output Capacitor Selection section to verify that
the worst-case output ripple is acceptable. The inductor
saturating current (I
SAT
) is also important to avoid run-
away current during continuous output short circuit.
Select an inductor with an I
SAT
specification higher than
the maximum peak current limit of 2.6A.
Input Capacitor Selection
The discontinuous input current of the buck converter
causes large input ripple currents and therefore the
input capacitor must be carefully chosen to keep the
input voltage ripple within design requirements. The
input voltage ripple is comprised of
∆V
Q
(caused by the
capacitor discharge) and
∆V
ESR
(caused by the ESR of
the input capacitor). The total voltage ripple is the sum
of
∆V
Q
and
∆V
ESR
. Calculate the input capacitance and
ESR required for a specified ripple using the following
equations:
where
I
OUT_MAX
is the maximum output current, D is the duty
cycle, and f
SW
is the switching frequency.
The MAX5080/MAX5081 includes internal and external
UVLO hysteresis and soft-start to avoid possible unin-
tentional chattering during turn-on. However, use a bulk
capacitor if the input source impedance is high. Use
enough input capacitance at lower input voltages to
avoid possible undershoot below the undervoltage
lockout threshold during transient loading.
Output Capacitor Selection
The allowable output voltage ripple and the maximum
deviation of the output voltage during load steps deter-
mine the output capacitance and its ESR. The output
ripple is mainly composed of
∆V
Q
(caused by the
capacitor discharge) and
∆V
ESR
(caused by the volt-
age drop across the equivalent series resistance of the
output capacitor). The equations for calculating the
peak-to-peak output voltage ripple are:
Normally, a good approximation of the output voltage
ripple is
∆V
RIPPLE
≈ ∆V
ESR
+
∆V
Q
. If using ceramic
capacitors, assume the contribution to the output volt-
age ripple from ESR and the capacitor discharge to be
∆
∆
∆
∆
V
I
1
V
I
Q
PP
OUT
SW
ESR
P-P
=
Ч
Ч
=
Ч
6
C
f
ESR
(
)
∆I
V
V
V
V
L
D
V
V
P-P
IN
OUT
OUT
IN
SW
OUT
IN
=
Ч
Ч
Ч
=
−
f
and
ESR
V
I
I
D
D
f
=
+
⎛
⎝⎜
⎞
⎠⎟
=
Ч
Ч
−
∆
∆
∆
ESR
OUT_MAX
P-P
IN
OUT_MAX
Q
SW
I
C
1
V
2
(
)
(
)
L
f
=
Ч
Ч
−
V
V
V
V
I
OUT
IN
OUT
IN
SW
P-P
∆
R
R
V
V
4
3
1
=
⎡
⎣
⎢
⎤
⎦
⎥
−
OUT
FB