Applications information – Rainbow Electronics MAX15040 User Manual
Page 11
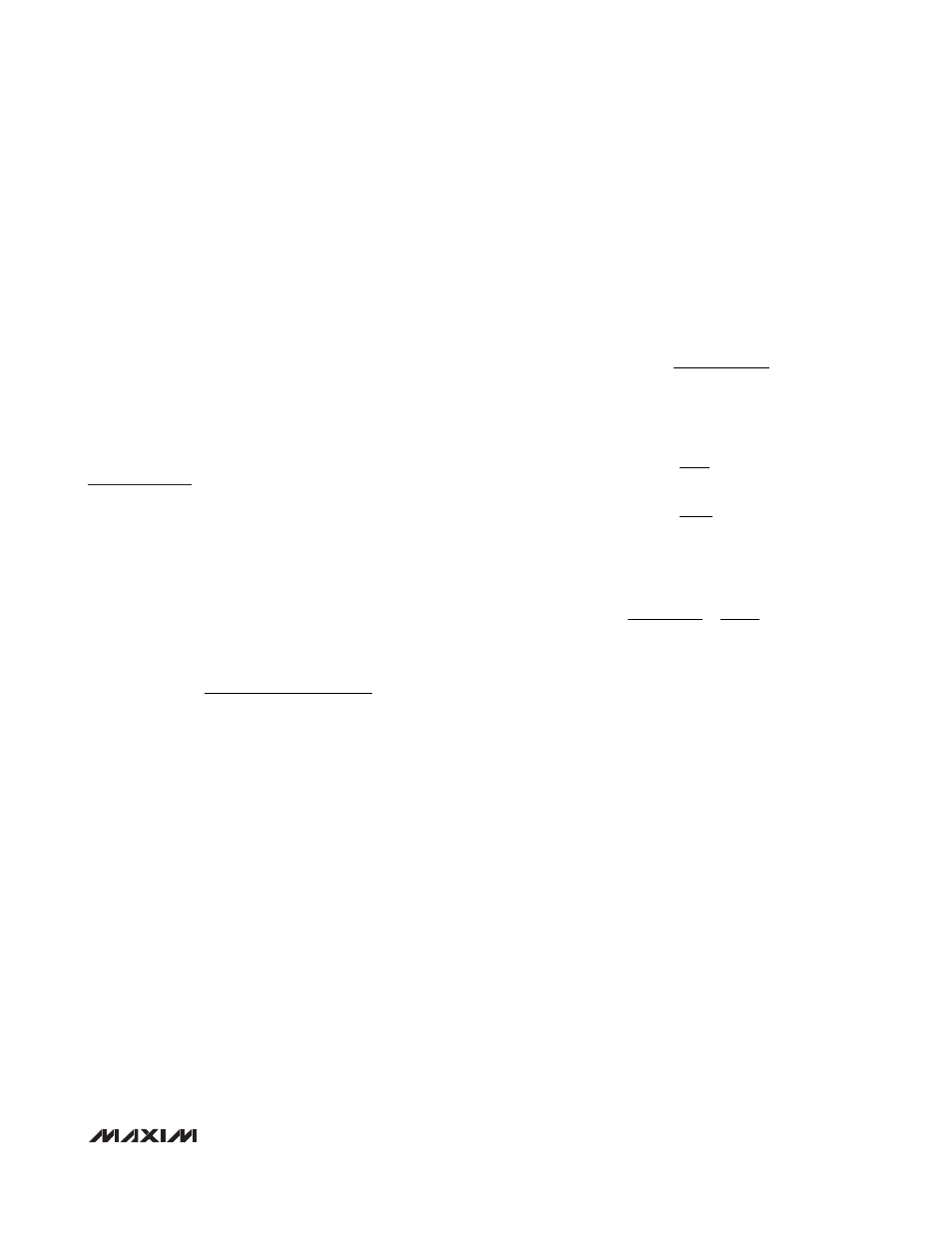
MAX15040
High-Efficiency, 4A, Step-Down Regulator with
Integrated Switches in 2mm x 2mm Package
______________________________________________________________________________________
11
Shutdown Mode
Drive EN to GND to shut down the device and reduce
quiescent current to less than 0.1µA. During shutdown,
LX is high impedance. Drive EN high to enable the
MAX15040.
Thermal Protection
Thermal-overload protection limits total power dissipation
in the device. When the junction temperature exceeds T
J
= +165°C, a thermal sensor forces the device into shut-
down, allowing the die to cool. The thermal sensor turns
the device on again after the junction temperature cools
by 20°C, causing a pulsed output during continuous
overload conditions. The soft-start sequence begins after
recovery from a thermal-shutdown condition.
Applications Information
IN and V
DD
Decoupling
To decrease the noise effects due to the high switching
frequency and maximize the output accuracy of
the MAX15040, decouple V
IN
with a 22µF capacitor in
parallel with a 0.1µF capacitor from V
IN
to GND. Also
decouple V
DD
with a 1µF capacitor from V
DD
to GND.
Place these capacitors as close as possible to the device.
Inductor Selection
Choose an inductor with the following equation:
where LIR is the ratio of the inductor ripple current to full
load current at the minimum duty cycle and f
S
is the
switching frequency (1MHz). Choose LIR between 20%
to 40% for best performance and stability.
Use an inductor with the lowest possible DC resistance
that fits in the allotted dimensions. Powdered iron or ferrite
core types are often the best choice for performance.
With any core material, the core must be large enough
not to saturate at the current limit of the MAX15040.
Output-Capacitor Selection
The key selection parameters for the output capacitor are
capacitance, ESR, ESL, and voltage-rating requirements.
These affect the overall stability, output ripple voltage,
and transient response of the DC-DC converter. The out-
put ripple occurs due to variations in the charge stored
in the output capacitor, the voltage drop due to the
capacitor’s ESR, and the voltage drop due to the
capacitor’s ESL. Estimate the output voltage ripple due
to the output capacitance, ESR, and ESL as follows:
where the output ripple due to output capacitance,
ESR, and ESL is:
or whichever is higher.
The peak-to-peak inductor current (I
P-P
) is:
Use these equations for initial output capacitor selec-
tion. Determine final values by testing a prototype or an
evaluation circuit. A smaller ripple current results in less
output voltage ripple. Since the inductor ripple current
is a factor of the inductor value, the output voltage rip-
ple decreases with larger inductance. Use ceramic
capacitors for low ESR and low ESL at the switching
frequency of the converter. The ripple voltage due to
ESL is negligible when using ceramic capacitors.
Load-transient response depends on the selected out-
put capacitance. During a load transient, the output
instantly changes by ESR x
∆I
LOAD
. Before the con-
troller can respond, the output deviates further,
depending on the inductor and output capacitor val-
ues. After a short time, the controller responds by regu-
lating the output voltage back to its predetermined
value. The controller response time depends on the
closed-loop bandwidth. A higher bandwidth yields a
faster response time, preventing the output from deviat-
ing further from its regulating value. See the
Compen-
sation Design
section for more details.
I
V
V
f
L
x
V
V
P P
IN
OUT
S
OUT
IN
−
=
−
×
V
RIPPLE ESL
(
))
=
−
I
t
x ESL
P P
OFF
V
I
t
x ESL or
RIPPLE ESL
P P
ON
(
)
=
−
V
I
x
RIPPLE ESR
P P
(
)
=
−
E
ESR
V
I
x C
x f
RIPPLE C
P P
OUT
S
( )
=
−
8
V
V
V
V
RIPPLE
RIPPLE C
RIPPLE ESR
RIPPLE ESL
=
+
+
( )
(
)
(
)
L
V
V
V
f
V
LIR I
OUT
IN
OUT
S
IN
OUT MAX
=
Ч
−
Ч
Ч
Ч
(
)
(
)