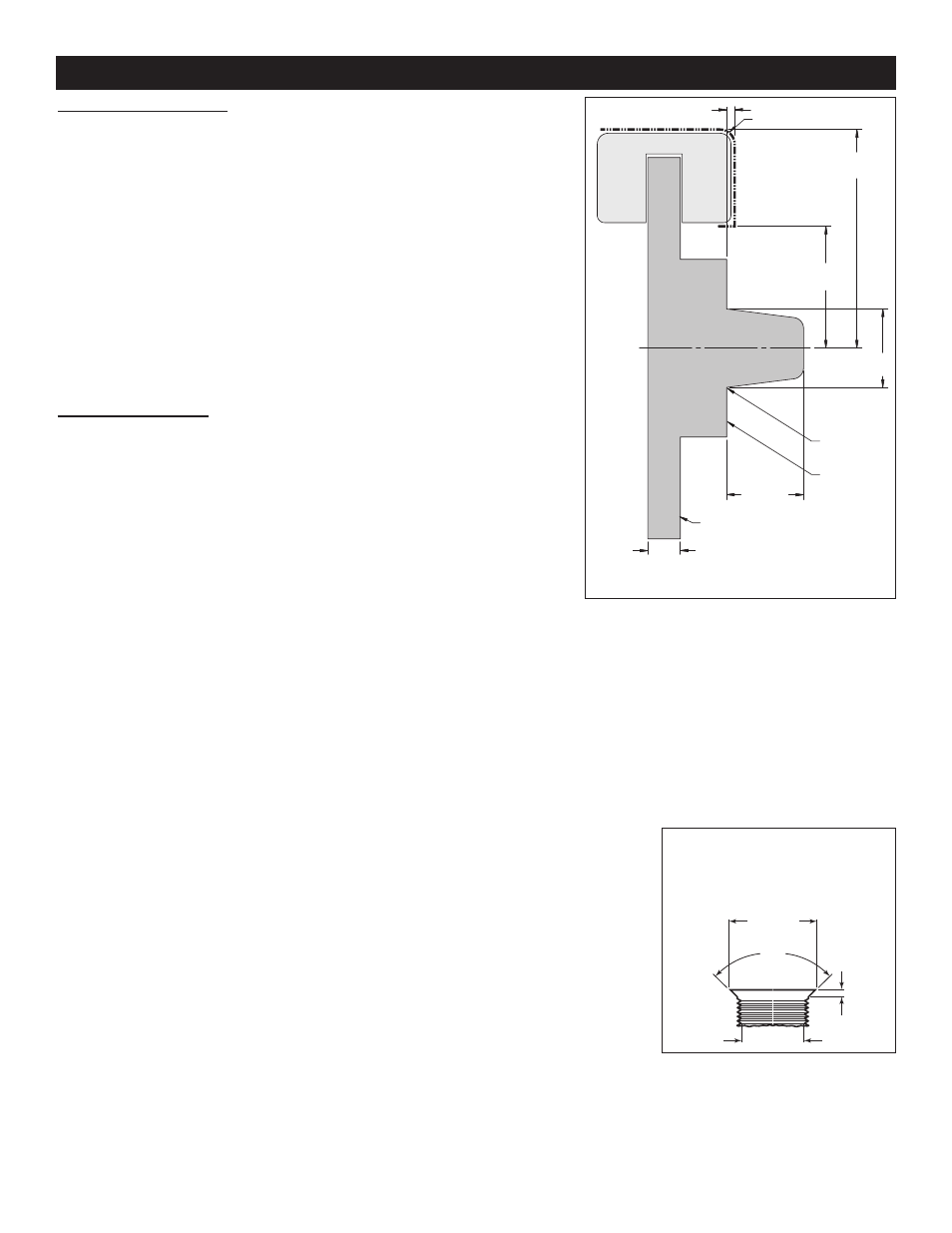
Disassembly and Assembly Instructions
Disassembly Instructions
•Disassemble the original equipment front brakes:
Raise the front wheels off the ground and support the front suspension according
to the vehicle manufacturer’s instructions.
•Remove the front wheels and completely disassemble the stock brake system
down to the bare spindles. Save the original equipment manufacturer’s (OEM)
spindle nuts and nut locks (if any). Reinstall the front steering arm bolt, do not
tighten at this time.
•Remove any nicks or burrs on the spindle mount faces that may interfere with the
installation of the new brake components.
•Clean and de-grease the spindles and saved components.
Assembly Instructions (numbers in parenthesis refer to the parts list on the
preceding page, and Figure 1):
•NOTE: 1964-66 spindles may require the following modifications (reference figure
1 and 3): Top anchor pin hole (Z) must be drilled and tapped to the dimensions as
outlined in Figure 3. Bottom rear steering arm bolt hole (Y) in the spindle and
steering arm must be enlarged to .50” by drilling. A 1/2-20 backing nut (not
supplied in kit) will need to be acquired to torque bracket / steering arm bolt
(supplied in kit).
•Disc Application: The caliper mount bracket (1) should be installed first with
clean, dry threads on the mounting bolts. Orient the bracket as shown in Figure 1,
and install using bottom bolt (5), washer (6), and washer (7, Heidts spindle kit
only). Install the upper bolt (2A), spacer (3) and washer (4, Heidts spindle kit only),
finger tighten only. NOTE: The bracket must fit squarely against the mount bosses
on the upright.
Inspect for interference from casting irregularities, machining
ridges, burrs, etc. If needed to align the bracket parallel to the spindle, add shim
washer (8) between bracket and spindle as shown in Figure 1. Once the bracket
alignment is correct, remove the mounting bolts one at a time and apply red
Loctite
®
271 to the threads, and torque bolt (2A) to 140 ft-lbs and bolt (5) to 77 ft-
lb.
•Drum Application: The caliper mount bracket assembly (1) should be installed first with clean,
dry threads on the mounting bolts. Orient bracket as shown in Figure 1, and install using the
bottom bolt (5), washer (6), and washer (8). Install the upper bolt (2), finger tighten only.
NOTE: The bracket must fit squarely against the mount bosses on the upright. Inspect for
interference from casting irregularities, machining ridges, burrs, etc. Once the bracket
alignment is correct, remove the mounting bolts one at a time and apply red Loctite
®
271 to the
threads, and torque bolt (2) to 140 ft-lbs and bolt (5) to 77 ft-lb.
•Install wheel studs (9) into the hub (10), Photo 1. Torque to 77 ft-lb. NOTE: There are two five
lug patterns in the hub (5 x 4.50 and 5 x 4.75). Ensure the correct hub stud pattern is being
used to fit the wheel application.
•Pack the large inner bearing cone (11) with high temperature disc brake bearing grease
(available from your local auto parts store) and install into the backside of the hub (10), Photo 2.
•Install the grease seal (12) by pressing into the backside of the hub (10), flush with the end of
the hub, Photo 2.
CENTER
LINE OF
WHEEL
.50 (12,7) RADIUS
.02 (0,5)
4.13
(104,9)
2.41
(61,2)
7.40
(188,0)
CALIPER
WILWOOD ROTOR
WHEEL MOUNT
SURFACE
.00 (0,0) RADIUS
NOTE: A MINIMUM OF .080” CLEARANCE MUST BE MAINTAINED
BETWEEN THE WHEEL AND CALIPER IN ALL AREAS
1.10 (27,9) ROTOR THICKNESS
1.67 (42,4)
Figure 2. Wheel Clearance Diagram
90°
.578 DIA
.032
.642 DIA
Drill a .578" diameter hole 1.25" deep
and tap 5/8-18 (fine thread).
Countersink .642" x 90°
Figure 3. Drill and Tap Detail
Page 4