High Lifter Outlaw Clutch Kit for Arctic Cat 550 H1 EFI 4x4 (2009) User Manual
Page 2
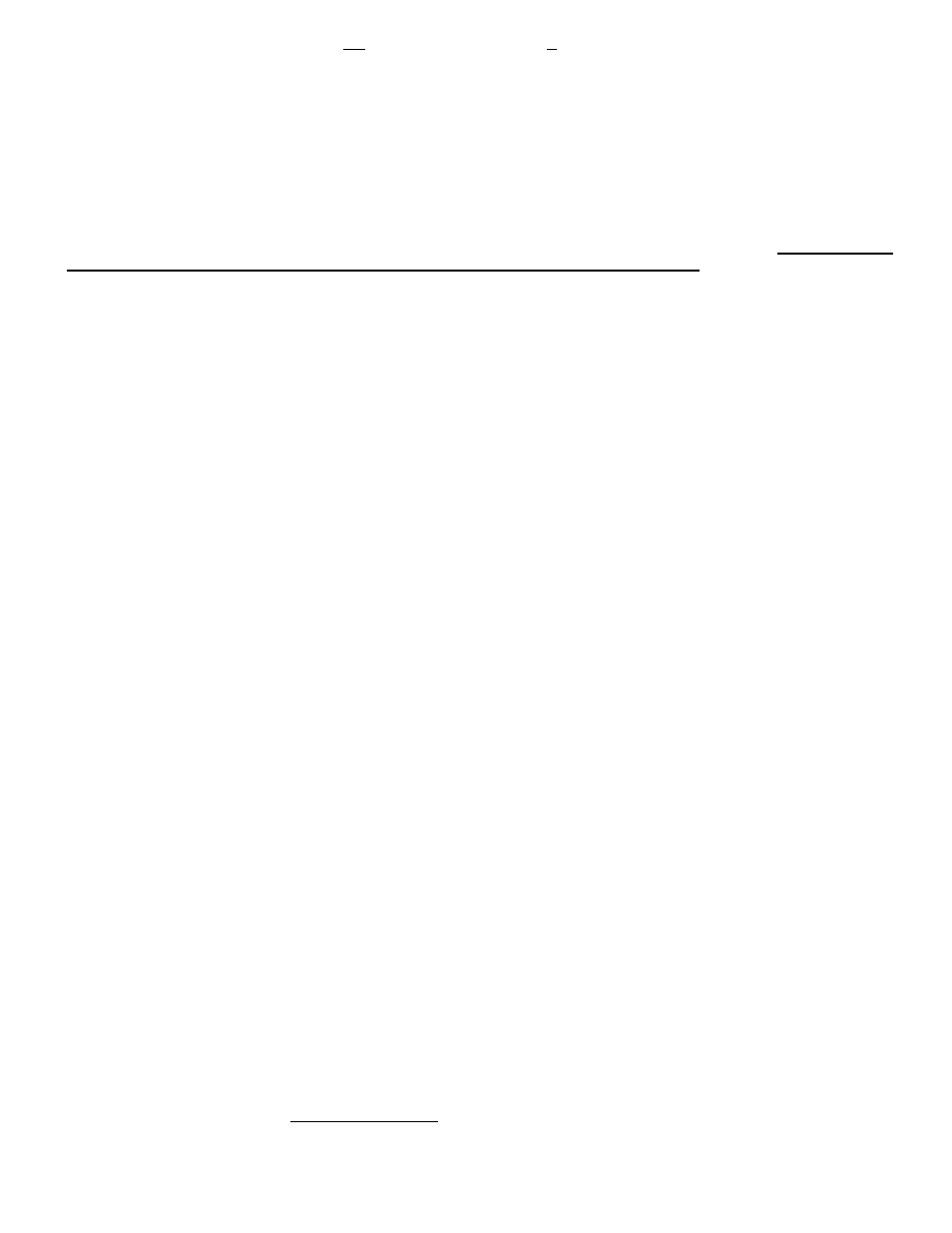
6. Install the EPI secondary spring in the #3 hole in the helix and the B setting in the clutch. Align the helix on the
splined shaft and place the snap ring on the helix. Using the compression tool (EPI part # CCT510) slowly and
carefully compress about halfway down. While holding the helix and the bottom half of the clutch from moving, turn
the top half of the clutch counterclockwise approximately a 1/3 of a turn so the plastic buttons in the clutch rotate
past the next ramp on the helix. Push the helix down and install the key way and the snap ring. Once the snap ring
has been installed you can remove the clutch from the press. Set the clutch aside.
7. Remove the oil drain plug from the motor; if you can carefully drain it into a clean container you should be able to
reuse it. After oil is drained, remove the back half of the clutch housing to gain access to the internal clutch cover.
To remove the back half of the housing, remove the bolts holding it in place and detach the 2 vent hoses. Now you
will be able to see the internal clutch cover. It is an aluminum cover that has the primary clutch shaft sticking out of
it. Remove the bolts and slowly remove the housing, try not to damage the gasket. If gasket is damaged you will
need to install a new one. Some oil may leak from the housing when first removed, this is normal. Note: There is
a directional bearing inside the clutch housing that must be reinstalled correctly. As you remove the
housing, watch for this bearing – it might stay on the shaft or come off and stay inside the housing. Look for it and
confirm that it is in the housing. If it stays on the shaft, carefully remove it and put it in the housing making sure
not to change its direction – it must remain in its correct direction or you will be taking this apart again! To
confirm the direction of this bearing, one side of it will have either an arrow or “this side out” printed on it. You
need to be able to read this side of the bearing when it is installed on the shaft (facing out of the motor towards
you) - not when installed in the housing. If you are unsure – call us to confirm that you have this bearing installed
correctly.
8. Remove the nut (left handed threads) holding the internal clutch on. Slide the clutch basket off; keep track of which
side faces out. Place clutch on a clean work area. Push down slightly on the outside cover and remove the e-clips.
Keeping track of which way they come off remove the three round metal plates one at a time. This will allow you to
see and change the complete spring. Remove the stock sprague springs. Install the EPI springs by inserting the
spring into the outer edge first. Using a spring tool or pliers pull on the spring and insert the end into the hole.
Install the three metal plates and the e-clips. Slide the clutch basket back onto the machine. Install the nut and
torque it to 94 ft/lbs. Confirm that the directional bearing is installed correctly – it must remain in its
correct direction or you will be taking this apart again! To confirm the direction of this bearing, one side of it
will have either an arrow or “this side out” printed on it. You need to be able to read this side of the bearing when it
is installed on the shaft (facing out of the motor towards you) - not when installed in the housing. If you are
unsure – call us to confirm that you have this bearing installed correctly. Install the gasket and install the aluminum
housing. Torque the housing bolts to 7.2 ft/lbs.
9. Bolt on the clutch housing and any other brackets that were removed. Push the back half of the primary clutch back
onto the shaft. Put the secondary clutch on; make sure it slides on all the way. Torque the nut to 72 ft/lbs. Thread
the bolt included in this kit into one of the threaded holes on the side of the secondary clutch. This should spread
the clutch sheaves apart. Put the belt in the clutch. Most belts have an arrow indicating direction of rotation. If
your belt doesn’t, be sure to install it so that you can read the part number. In either case, always run the belt the
same direction as it was new.
10. Grab the primary clutch, push the inner part down with your thumbs and hold down as you pick up the clutch.
While holding the inner part of the clutch from moving, slide the primary clutch onto the shaft. This should keep the
rollers in place. Keep it pushed in until you can install the nut and washer. The clutch should slide all the way back
easily. If the clutch doesn’t seem to go on far enough to tighten the nut properly (it should slide all the way on so
that the splines on the shaft are showing approximately 1/16 of an inch) you might have a roller out of place or the
belt might be blocking it. If needed, move the belt up and down to see if the clutch will slide on farther. If the
rollers seem out of place take the clutch apart and check roller location. Install the large nut and torque it to 83
ft/lbs. Remove the bolt that was threaded into the secondary clutch.
11. Carefully install the clutch cover and gasket to ensure a good seal. Install the foot well including the brake pedal
and metal support bracket if they were removed. Attach the fenders to the foot well.
12. Install oil drain plug. Refill your engine oil to the proper level according to owners manual. You can reuse your oil
if it is clean and was drained into a clean container. You must use NON Friction Modified oil (stock Arctic Cat). DO
NOT use oils with Friction Reducing Agents, this WILL CAUSE SLIPPAGE AND DAMAGE.
13. Go out and ride your machine. If the performance doesn’t seem right double check to make sure everything has
been done properly.
NOTICE: Even with this clutch kit, you should be advised that using substantial throttle when the tires are not able to
spin can cause the belt to slip and damage may occur. EPI recommends that the transmission be shifted into low
range when high load, slower speed situations are encountered. EPI is not responsible for any damage to the drive
belt or any other original equipment component.