Actron GM Code Scanner CP9001 User Manual
Page 34
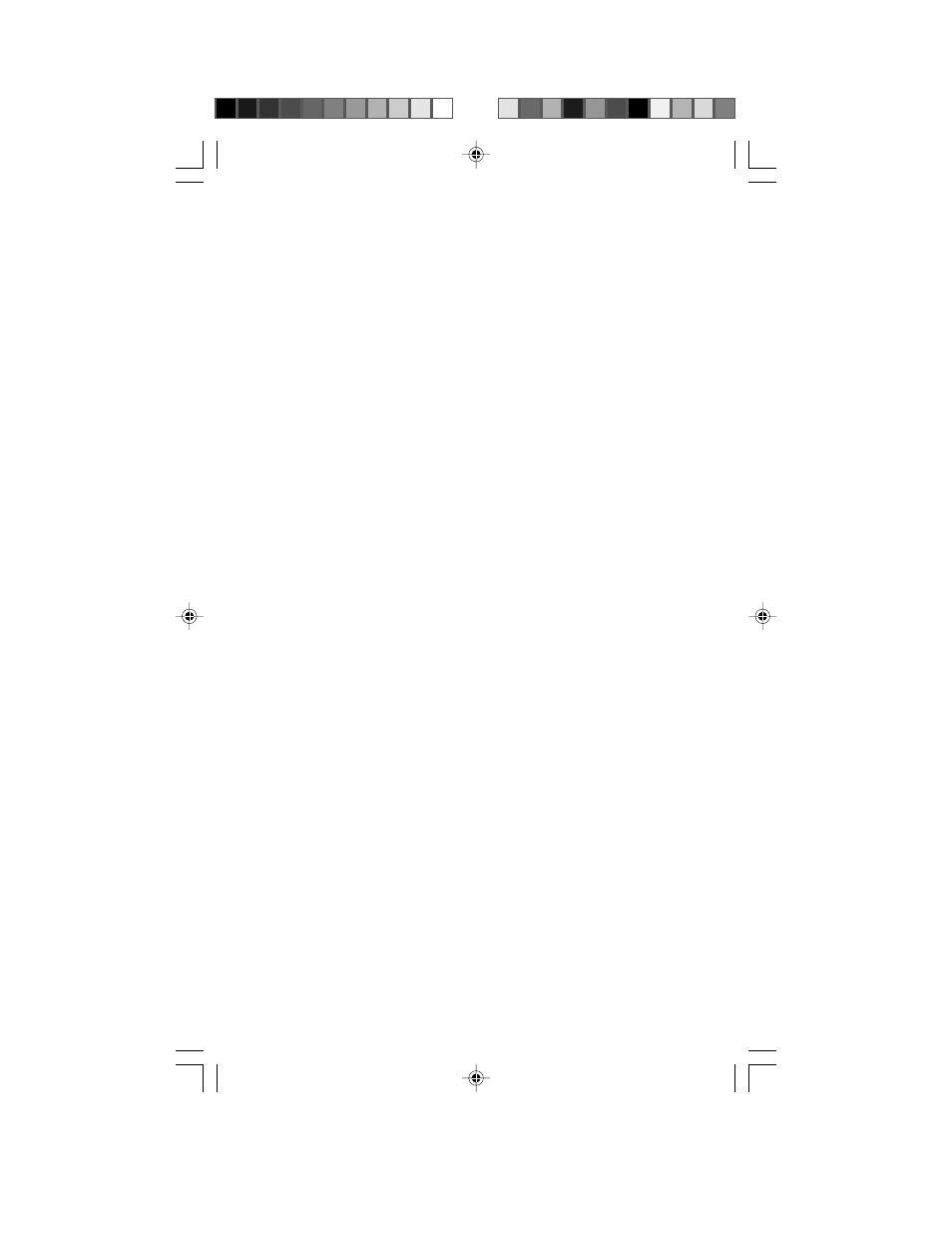
34
C3
Computer Command
Control. The name for the
GM electronic engine
control system used on
most vehicles built since
1982.
CALPAK
A “spare tire” for the ECM.
It is circuitry which can
operate the vehicle fuel
injectors in a limited
fashion should the ECM
malfunction. The CALPAK
is hidden behind an
access door on the ECM.
The replaceable CALPAK
module is only used on
certain ECM’s.
CAM
Camshaft Position Sensor.
This sensor sends a
frequency signal to the
ECM. Vehicles with
sequential fuel injection
(SFI) use this signal to
synchronize the injector
firing order. Some DIS
type ignition systems use
this signal to synchronize
spark plug firing.
Closed Loop (C/L)
This is when a control
system performs an action
(expecting a certain
result), then checks the
results and corrects its
actions (if necessary) until
the desired results are
achieved. Example: Fuel
delivery. The ECM
operates a fuel injector in
a way which should deliver
an optimum air/fuel
mixture - if everything in
the fuel system is
operating as expected! In
closed loop operation, the
ECM uses the oxygen
sensor to check the
results. (Fuel delivery may
be different than expected
because of variations in
fuel pressure or injector
operation.) If the oxygen
sensor indicates a “rich”
condition, the ECM will
compensate by reducing
fuel delivery until the
oxygen sensor signals an
optimum air/fuel ratio.
Likewise, the ECM will
compensate for a “lean”
condition by adding fuel
until the oxygen sensor
once again signals an
optimum air/fuel mixture.
Thus, closed loop operation
means the ECM can “fine
tune” control of a system to
get an exact result providing
the ECM has a sensor (or
other means) to check
results.
Continuity
An unbroken, continuous
circuit through which an
electric current can flow.
CPS
Crankshaft Position
Sensor. This sensor sends
a frequency signal to the
ECM. It is used to
reference fuel injector
operation and synchronize
spark plug firing on
distributorless ignition
systems (DIS).
CTS
Coolant Temperature
Sensor. This sensor is a
thermistor - a resistor
whose resistance
decreases with increases
in temperature. The sensor
is threaded into the engine
block and contacts the
engine coolant. The ECM
uses this signal for control
of fuel delivery, spark
advance and EGR flow.
Digital Signal
An electronic signal which
has only two (2) voltage
values: a “low” value (close
to zero) and a “high” value
(usually 5 volts or greater).
Sometimes the low voltage
condition is called “Off” and
the high voltage condition
is called “On”. Signals
which can have any
voltage value are called
“analog” signals.
DIS
Distributorless Ignition
System or Direct Ignition
System. A system which
produces the ignition spark
without the use of a
distributor.
Driver
A transistor “switch” inside
the ECM used to apply
power to an external
device. This allows the
ECM to control relays,
solenoids and small
motors.
Duty Cycle
A term applied to
frequency signals - those
which are constantly
switching between a small
voltage value (close to
zero) and a larger value
(usually 5 volts or greater).
Duty cycle is the
percentage of time the
signal has a large voltage
value. For example, if the
signal is “high” (large
voltage) half of the time
then the duty cycle is 50%.
If the signal is “high” only
one fourth of the time, then
the duty cycle is 25%. A
duty cycle of 0% means
the signal is always at a
“low” value and not
changing. A duty cycle of
100% means the signal is
always at a “high” value
and not changing. The
engine control computer
uses duty cycle type
signals when it wants more
than just “on-off” control of
an actuator. This is how it
works: A 50% duty cycle
signal going to a vacuum
switching solenoid means
the solenoid will be “on”
(passing full vacuum) half
the time and “off” (passing
no vacuum) half the time.
The average amount of
vacuum passing through
the solenoid will be one
half the full value because
the solenoid is only “on” for
one half the time. (The
signal switches at a rapid
rate, such as ten times a
second.) Thus, the
computer can get a
vacuum controlled actuator
to move half way between
“no vacuum” position and
“full vacuum” position.
Other positions can be
achieved by changing the
duty cycle of the control
signal which in turn
changes the average
amount of control vacuum.
DVM
Digital Volt Meter. An
instrument using a numeric
readout to display
measured voltage values
as opposed to a moving
needle on a gauge face.
Usually the instrument has
other measuring
capabilities, such as
resistance and current,
and may be called a DMM