Whirlpool EDP/EDN User Manual
Page 31
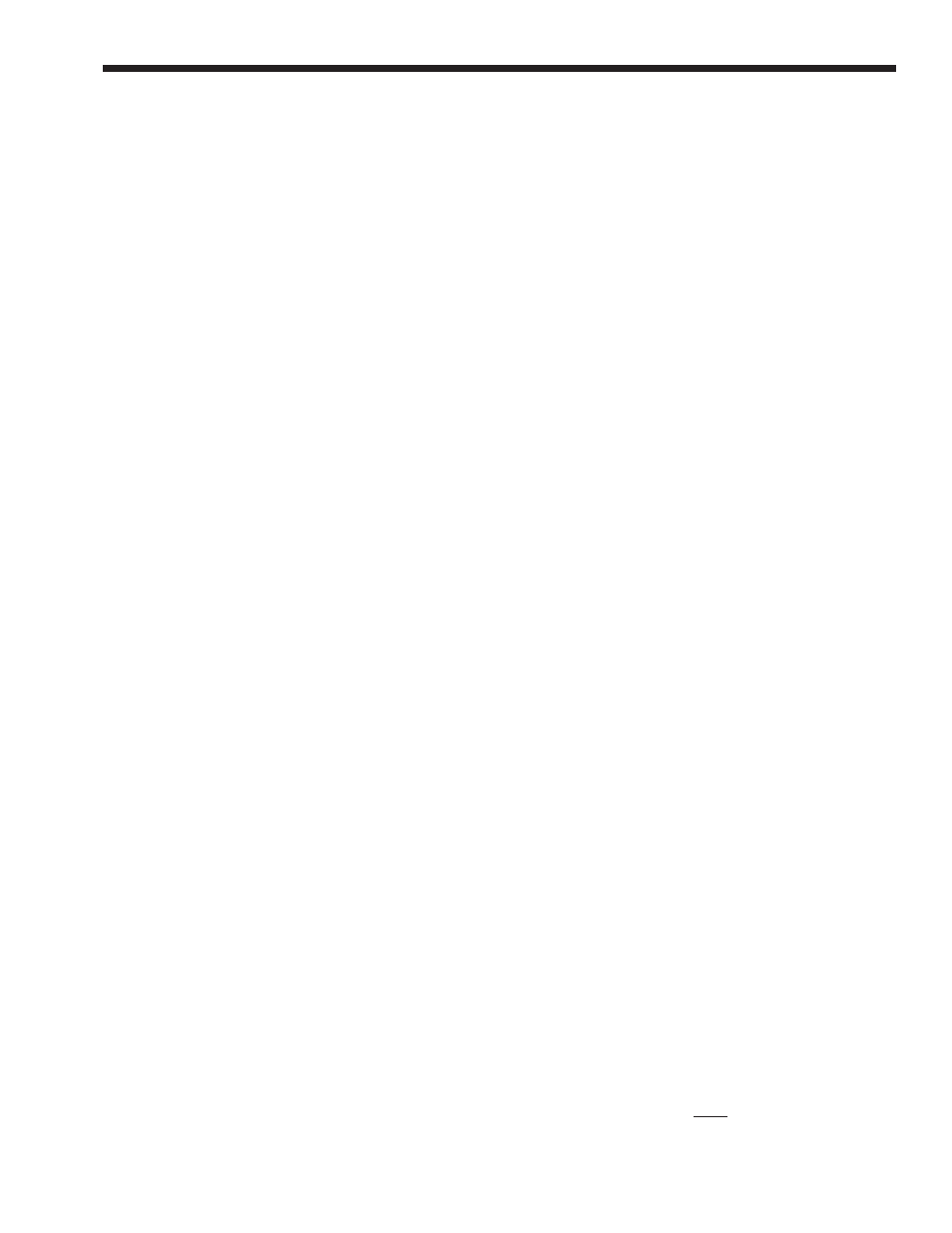
Endurance
Page 31
observe the offset pressure at startup and after 20
seconds. The pressure will be ~ -2 in. w.c. at
startup (during prepurge) and should become
less negative (-0.1 in. w.c.) when the gas valve
opens and gas flow starts. If the pressure remains
at ~ -2 in. w.c. throughout the cycle replace the
gas valve.
4.
Ignitor failure: If the boiler goes through a
normal start cycle but combustion does not
occur, ignitor failure should be suspected.
Check the ignitor by unplugging the ignitor plug
and measuring the ignitor resistance. It should be
50-100 (
W) ohms. If the resistance is not 50-100
ohms (
W), replace the ignitor. If the resistance is
correct, reset the boiler and check for 120 VAC
at the ignitor plug during the start cycle. If there
is no voltage, replace the PCB or faulty ignitor
wires.
5.
Blocked or contaminated air source: Before
proceeding, ensure that the vent terminal (Direct
Vent installations) or the air inlet (Category IV
installations) is not obstructed. In general, only
direct vent installations have the potential for
cross contamination (flue products entering the
combustion air stream) of the combustion air
source. This may be caused by leaky joints in the
3" flue pipe located inside the 5" combustion air
pipe. If this is suspected, remove the front panel
from the appliance, reset the boiler and allow it
to go through a normal cycle. If during this cycle
there is no flue odor, repair the leaky joints in
the flue pipe.
SECTION 9.
Gas Valve Calibration
9A. Gas Valve Calibration
(offset adjustment)
If poor combustion is suspected because of a
strong exhaust smell, pulsation in the exhaust, or
nuisance flame failure lockouts (shown as “LO” on
LED), the gas valve offset pressure and exhaust CO
2
should be checked and adjusted, if required. A
magnehelic pressure gauge (with 0.1 in. w.c.
divisions) and a CO
2
tester are required for this
adjustment.
Note: Direct vent installations may experience
poor combustion that results from cross contamination
of the combustion air source. Check for cross
contamination before attempting offset pressure
adjustment (see Section 8B-3.5).
CO
2
sampling may be taken at the exhaust
terminal or at the sample port on the 3” exhaust
located inside the front panel top cover. See Figure 28
for the location of the offset pressure port and offset
adjustment.
The CO
2
values shown in Table 4 should be
achieved when the unit is in high fire. To manually fix
the unit in high fire, locate the four-pin connector on
the bottom left of the control board, and jumper the
middle two terminals together (see Figure 29). NOTE:
For EBP (combination heat & hot water) units, when
the unit is in “tank charge” mode it will stay in high
fire, whether manually jumpered or not.
Note: During the prepurge cycle, the gauge will
indicate several in. W.C. negative pressure.
Adjust the CO
2
and/or offset pressure to the
values shown in Table 4.
When adjusting the offset pressure, the CO
2
will
reduce as the offset pressure is adjusted more
negative. FINAL ADJUSTMENT OF THE
OFFSET PRESSURE MUST ALWAYS RESULT
IN A NEGATIVE PRESSURE UPON
COMPLETION.
SECTION 10.
Symptom Evaluations
10A. Delayed ignition
Possible Causes
a.
High lockup pressure (LP boilers) - occurs on
start-up.
b.
Gas valve regulation problem - occurs on start-up.
c.
Incorrect gas orifice (Natural gas orifice in an LP
boiler) - occurs on start up
d.
Defective burner - occurs on startup or at burner
shutdown.
High lock up pressure is the most common cause
of delayed ignitions on LP fueled boilers. It may result
from an improper second stage regulator selection or
from a faulty regulator.
Lock up can be detected by measuring the gas
supply pressure to the boiler at the inlet pressure tap
on the gas valve. The gas supply to the boiler must be
shut off before making this connection. Use a water
manometer or pressure gauge with a scale reading of
at least 25 in. w. c. or 15 oz/in
2
. Loosen the screw in
the gas valve pressure port one full turn and install a
hose from the pressure gauge over the pressure port.
Turn on the gas supply. The ENDURANCE boiler is
designed to operate with supply pressures of 4-13 in.
w. c. (2.3 - 7.5 oz/ in²). If the supply pressure exceeds
13 in. w. c. (7.5 oz/ in²) with the boiler not operating it
is possible that this may be the cause of delayed
ignitions and the pressure must be reset to ~ 9 in. w. c.
(5.2 oz/ in2). Restart the boiler and then switch it off
again. Lock up pressures must be measured when the
boiler is not operating and preferably immediately
after boiler shutdown. If the gas pressure again
exceeds the allowable values, correct the lock up
problem.