Texas Instruments SLVU013 User Manual
Page 36
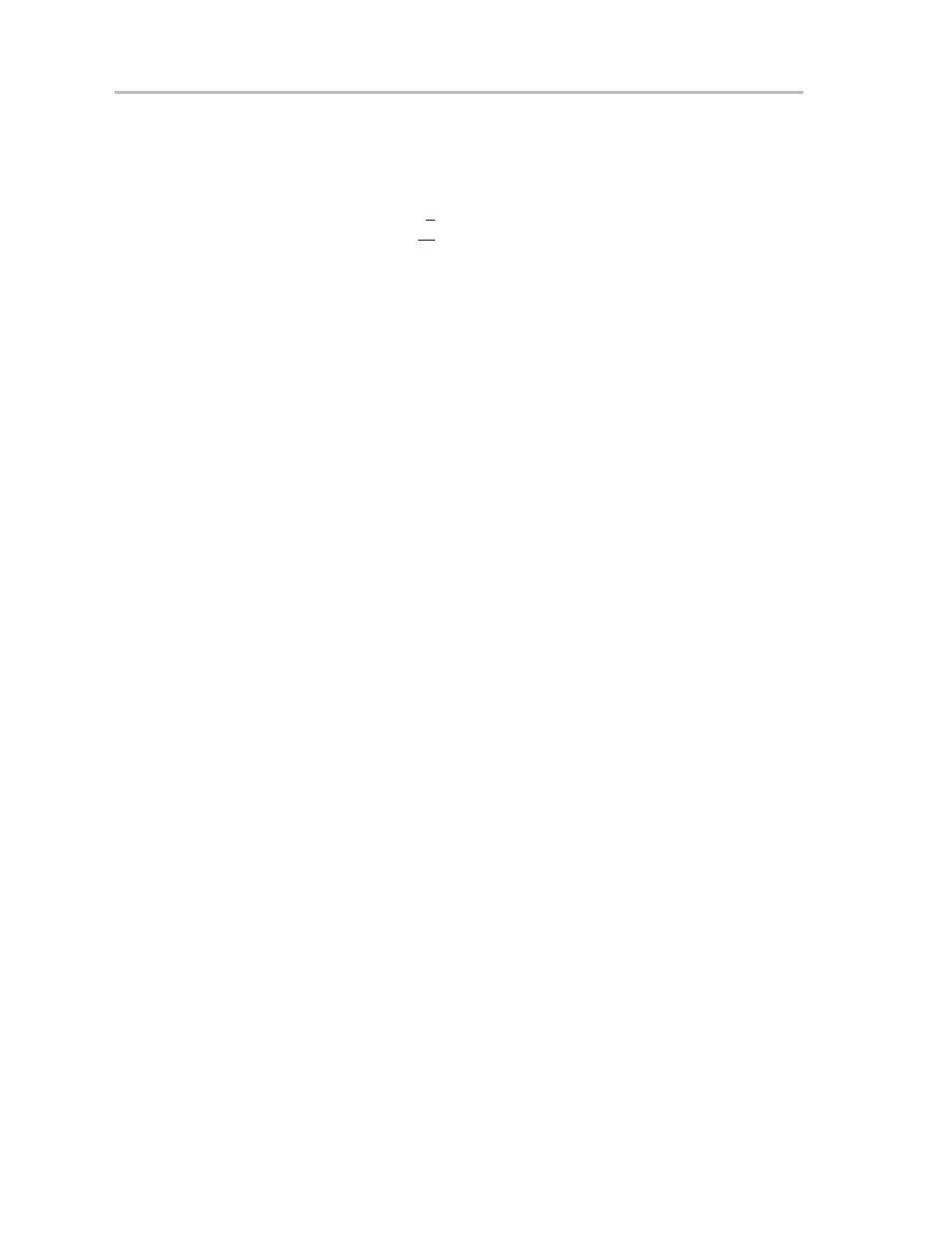
External Component Selection
2-16
for the particular application. In addition, the capacitor(s) must have an ample
ripple current rating to handle the applied ripple current. This ripple current is
dependent on the ripple current in the output inductance that is calculated in
the next section. The RMS current in the output capacitance is calculated as
follows for 3.3 V output:
I
CRMS
+ D
I
L
3
Ǹ
6
+ D
I
L
0.289
+
7.3
A
0.289
+
2.1
A
RMS
Where
∆
I
L
is the peak-to-peak ripple current in the output inductor.
The ripple current rating for one of these capacitors is 1.7 A RMS at 45
°
C. The
total ripple current rating for the output capacitance is 4
×
1.7 = 6.8 A RMS as-
suming that each cap shares equally. Poor layout may cause one or more of
the caps to take an unequal share.
2.2.3.2
Output Inductance
The output filter inductance is the next quantity to be determined. Like the out-
put capacitance selection, the primary consideration is providing satisfactory
response to a fast load transient.
The inductance affects the output voltage response to transient loads by
governing the rate at which its current can increase (or decrease). For
example, during a load transient where the output current increases from no
load to full load, the output capacitor supplies all of the output current until the
inductor current has time to increase to full load. So, a relatively small
inductance is desired.
On the other hand, the inductance also plays a part in the power supply
switching frequency, because the inductance limits how fast the output voltage
traverses through the hysteresis band. As the inductance decreases, the
output voltage changes faster, giving rise to higher switching frequencies.
Therefore, the inductor value is fairly critical and should be stable over the
expected load and temperature range. Care should be exercised in the
inductance selection because design requirements for hysteretic regulators
are different from PWM controlled converters. Recall that for a fixed frequency
PWM controlled buck converter, for a given operating point, the output
inductance governs the peak-to-peak amplitude and the slope (di/dt) of the
inductor current. In a hysteretic regulator, the ripple current is set by the output
voltage ripple setting and the output capacitance impedance.
Other important factors to be considered when designing or selecting the
inductor are current capability, allowable operating frequency, and dc
resistance.
After choosing an initial inductance value, the power supply switching
frequency must be estimated to insure that it is within the desired range. The
switching frequency for the example design given in Figure 1–3 is nominally
135 kHz for 5-V input and a 3.3-V output. A detailed analysis of the switching
frequency and an equation to predict it is given later.
To calculate the maximum inductance allowed for a given response time, load
step, and operating point, the following simple relationship is used: