Feeding wire electrode, Idle roll pressure setting, Making a weld – Lincoln Electric POWER MIG SVM157-A User Manual
Page 17: Operation, Warning
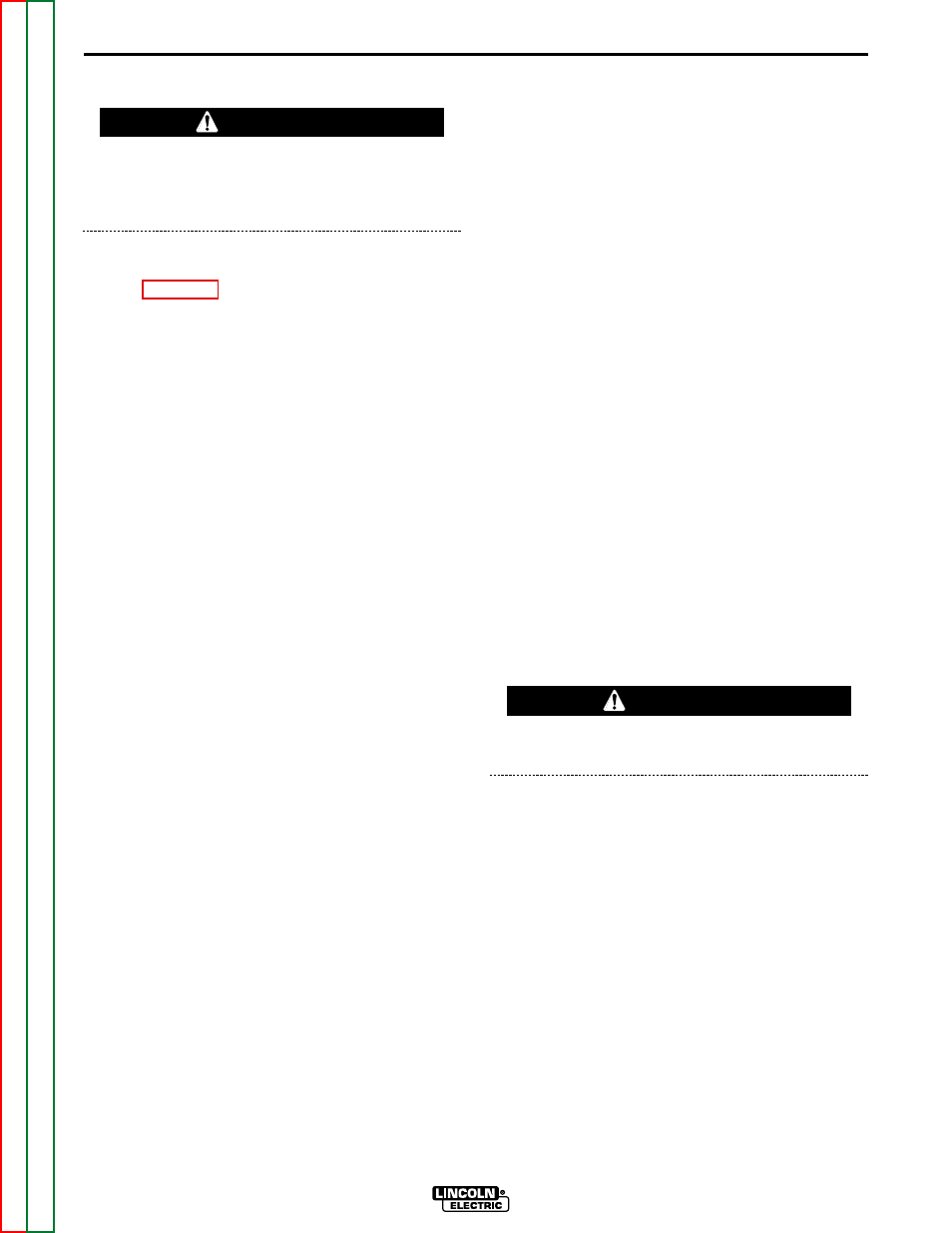
OPERATION
B-5
B-5
POWER MIG 200
FEEDING WIRE ELECTRODE
When triggering, the electrode and drive mecha-
nism are electrically “hot” relative to work and
ground and remain “hot” several seconds after the
gun trigger is released.
NOTE: Check that drive rolls, guide plates and gun
parts are proper for the wire size and type being used.
Refer to Table C.1 in Accessories section.
1. Turn the Readi-Reel or spool until the free end of the
electrode is accessible.
2. While securely holding the electrode, cut off the bent
end and straighten the first six inches. (If the elec-
trode is not properly straightened, it may not feed
properly through the wire drive system).
3. Release the pressure on the idle roll by swinging the
adjustable pressure arm down toward the back of
the machine. Lift the cast idle roll assembly and
allow it to sit in an upright position. Leave the outer
wire guide plate installed. Manually feed the wire
through the incoming guide bushing and through the
guide plates (over the drive roll groove). Push a suf-
ficient wire length to assure that the wire has fed into
the gun and cable assembly without restriction.
Reposition the adjustable pressure arm to its origi-
nal position to apply pressure to the wire.
4. Press gun trigger to feed the electrode wire through
the gun.
IDLE ROLL PRESSURE SETTING
The optimum idle roll pressure varies with type of wire,
wire diameter, surface conditions, lubrication, and
hardness. As a general rule, hard wires may require
greater pressure, and soft, or aluminum wire, may
require less pressure than the factory setting. The opti-
mum idle roll setting can be determined as follows:
1. Press end of gun against a solid object that is elec-
trically isolated from the welder output and press the
gun trigger for several seconds.
2. If the wire “birdnests”, jams or breaks at the drive
roll, the idle roll pressure is too great. Back the
adjustment knob out 1/2 turn, run new wire through
gun, and repeat above steps.
3. If the only result was drive roll slippage, loosen the
adjustment knob on the conductor plate and pull the
gun cable forward about 6" (15 cm). There should
be a slight waviness in the expose wire. If there is
not waviness, the pressure is too low. Tighten the
adjustment knob 1/4 turn, reinstall the gun cable and
repeat the above steps.
MAKING A WELD
1. Check that the electrode polarity is correct for the
process being used, then turn the power switch
ON.
2. Set desired arc voltage tap and wire speed for the
particular electrode wire, material type and thick-
ness, and gas (for GMAW) being used. Use the
Application Chart on the door inside the wire com-
partment as a quick reference for some common
welding procedures.
3. Press the trigger to feed the wire electrode through
the gun and cable and then cut the electrode within
approximately 3/8" (10 mm) of the end of the con-
tact tip [3/4" (20 mm) Outershield®].
4. If welding gas is to be used, turn on the gas supply
and set the required flow rate (typically 25-35 CFH;
12-16 liters/min).
5. When using Innershield electrode, the gas nozzle
may be removed from the insulation on the end of
the gun and replaced with the gasless nozzle. This
will give improved visibility and eliminate the possi-
bility of the gas nozzle overheating.
6. Connect work cable to metal to be welded. Work
clamp must make good electrical contact to the
work. The work must also be grounded as stated in
“Arc Welding Safety Precautions”.
When using an open arc process, it is necessary
to use correct eye, head, and body protection.
7.
Position electrode over joint. End of electrode may
be lightly touching the work.
8.
Lower welding helmet, close gun trigger, and begin
welding. Hold the gun so the contact tip to work
distance is about 3/8" (10 mm) [3/4" (20 mm) for
Outershield].
9.
To stop welding, release the gun trigger and then
pull the gun away from the work after the arc goes
out.
10. When no more welding is to be done, close valve
on gas cylinder (if used), momentarily operate gun
trigger to release gas pressure, and turn off
POWER MIG 200.
WARNING
WARNING