Hydronic piping, Installation & operation manual – Lochinvar KNIGHT 399 - 800 User Manual
Page 40
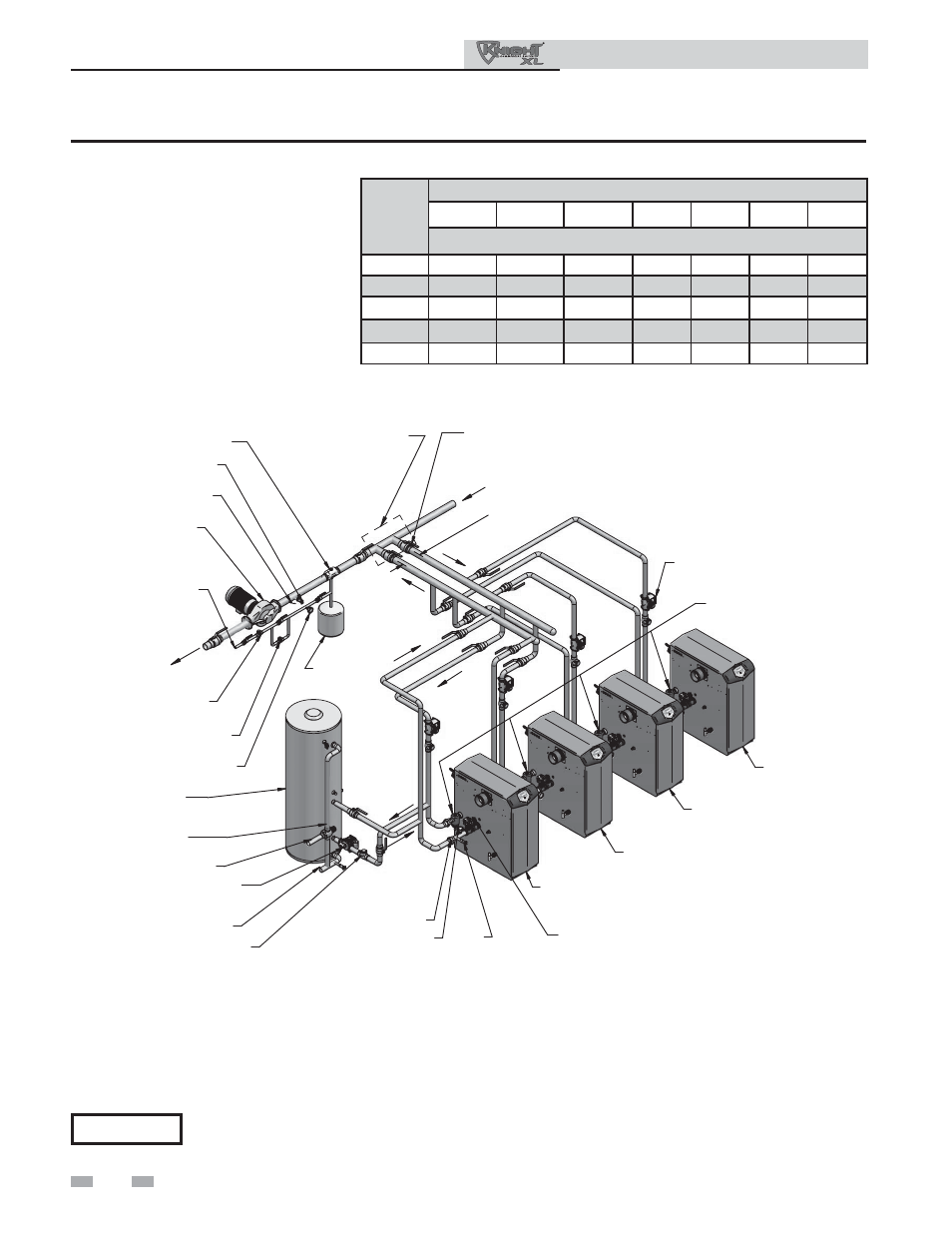
Installation & Operation Manual
40
EXPANSION
TANK
AIR SEPARATOR
PRESSURE REDUCING
VALVE
BACK FLOW
PREVENTER
BALL VALVE
(TYPICAL)
UNION (TYPICAL)
PRESSURE RELIEF
VALVE
FLOW CHECK
VALVE (TYPICAL)
INDIRECT DHW
TANK
BOILER 1
(LEADER)
TEMPERATURE / PRESSURE
GAUGE
PRESSURE GAUGE
DRAIN
DRAIN POINT
(TYPICAL)
BOILER CIRCULATOR
(TYPICAL)
ANTI-SCALD
MIXING VALVE
SYSTEM SUPPLY SENSOR
(WHEN USED)
SYSTEM CIRCULATOR
TO S
YS
TE
M
FROM SYSTEM
BOILER 2
(MEMBER 1)
BOILER 3
(MEMBER 2)
BOILER 4
(MEMBER 3)
DOMESTIC
HOT WATER
CIRCULATOR
COLD WATER IN
HOT WATER OUT
MAKE UP WATER
DIRT SEPARATORS
(RECOMMENDED)
MAY SUBSTITUTE
LOW LOSS HEADER
NO
T T
O EX
CE
ED
4 PIPE DIAMETERS
OR
A MAXIMUM OF 12"
AP
AR
T
Figure 6-8 Multiple Boilers - Primary/Secondary Piping
Model
Number of Units
2
3
4
5
6
7
8
Manifold Pipe Sizes in Inches (mm)
399
2 1/2 (64)
3 (76)
3 1/2 (89) 4 (102) 4 (102) 5 (127) 6 (152)
500
3 (76)
3 1/2 (89) 4 (102)
5 (127) 5 (127) 6 (152) 6 (152)
600
3 1/2 (89) 4 (102)
5 (127)
5 (127) 6 (152) 6 (152) 8 (203)
700
3 1/2 (89) 5 (127)
5 (127)
6 (152) 6 (152) 8 (203) 8 (203)
800
4 (102)
5 (127)
5 (127)
6 (152) 8 (203) 8 (203) 8 (203)
NOTICE
System flow should always remain higher than the required flow for the boiler(s) when the boiler(s) is in operation to
prevent short cycling and high limit issues.
6
Hydronic piping