Hydronic piping – Lochinvar 400 User Manual
Page 38
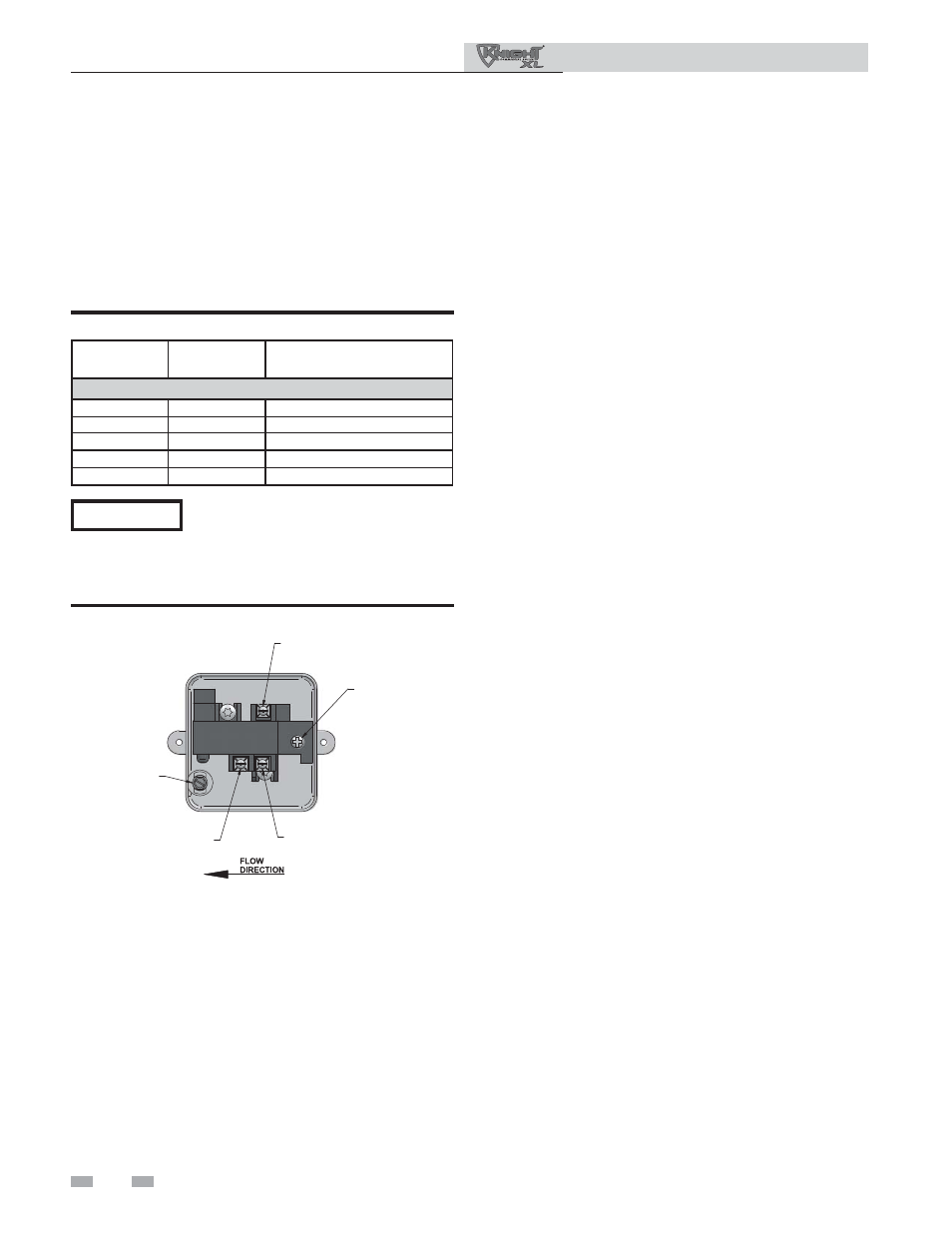
Installation & Operation Manual
6
Hydronic piping
Figure 6-3 Flow Switch Adjustment
Flow switch adjustment
Refer to Table 6A for the proper setting of the sensitivity
screw. For reference, the position of the screw prior to setting
should be turned clockwise with a Phillips driver until it stops
(FIG. 6-3). Proceed to turn the screw counterclockwise the
amount of turns listed in Table 6A based on the model.
Consult the manufacturer’s instructions for wiring the flow
switch to your system.
NORMALLY
OPEN
SENSITIVITY
ADJUSTMENT
NORMALLY
CLOSED
COMMON
GROUND
NOTICE
Turn the sensitivity screw clockwise to
increase the flow rate required to activate
the switch. Turn the sensitivity screw
counterclockwise to decrease the flow rate
required to activate the switch.
MODEL
PADDLE SIZE
SENSITIVITY SCREW
ADJUSTMENT
Note: Paddles are included with the flow switch.
400
#3
7½ turns
501
#3
5½ turns
601
#3
7¼ turns
701
#3
5¼ turns
801
#3
3¼ turns
Table 6A Paddle Size / Sensitivity Screw Adjustment
Near boiler piping components
1.
Boiler system piping:
Boiler system piping MUST be sized per the pipe
requirements listed in Table 6B. Reducing the pipe size
can restrict the flow rate through the boiler, causing
inadvertent high limit shutdowns and poor system
performance. Flow rates are based on 20 feet (6 m) of
piping, 4 - 90° elbows, and 2 - fully ported ball valves.
2.
Boiler system circulating pump:
Field supplied. The boiler circulating pump should be
based on 20 feet (6 m) of piping, 4 - 90° elbows, and
2 - fully ported ball valves.
3.
Domestic hot water circulating pump:
Field supplied. The pump MUST be sized to meet
the specified minimum flow requirements listed in
FIG.’s 6-5 and 6-6. Consult the indirect water heater
operating guide to determine flow characteristics for the
selected product used.
4.
Variable speed boiler system circulator:
Knight boilers are capable of controlling a variable
speed boiler system circulator. Variable speed circulators
MUST be sized to meet the specified minimum flow
requirements listed in FIG.’s 6-5 and 6-6 on page 40 at
full speed.
5.
Boiler isolation valves:
Field supplied. Full port ball valves are required. Failure
to use full port ball valves could result in a restricted flow
rate through the boiler.
6.
Check valves:
Field supplied. Check valves are recommended for
installation as shown in FIG.’s 6-7 through 6-11. Failure
to install check valves could result in a reverse flow
condition during pump(s) off cycle.
7.
Domestic indirect hot water isolation valves:
Field supplied. Full port ball valves are
required. Failure to use full port ball valves could
result in a restricted flow rate through the boiler.
8.
Anti-scald mixing valve:
Field supplied. An anti-scald mixing valve is
recommended when storing domestic hot water above
115°F (46°C).
9.
Unions:
Field supplied. Recommended for unit serviceability.
10. Temperature and pressure gauge:
Factory supplied. The temperature and pressure gauge is
shipped loose. It is the responsibility of the contractor to
install the temperature and pressure gauge on the boiler
water outlet.
11. Pressure relief valve:
Factory supplied. The pressure relief valve is sized to
ASME specifications.
38