Setting spindle speed, Calculating spindle speed – Grizzly G0695 User Manual
Page 30
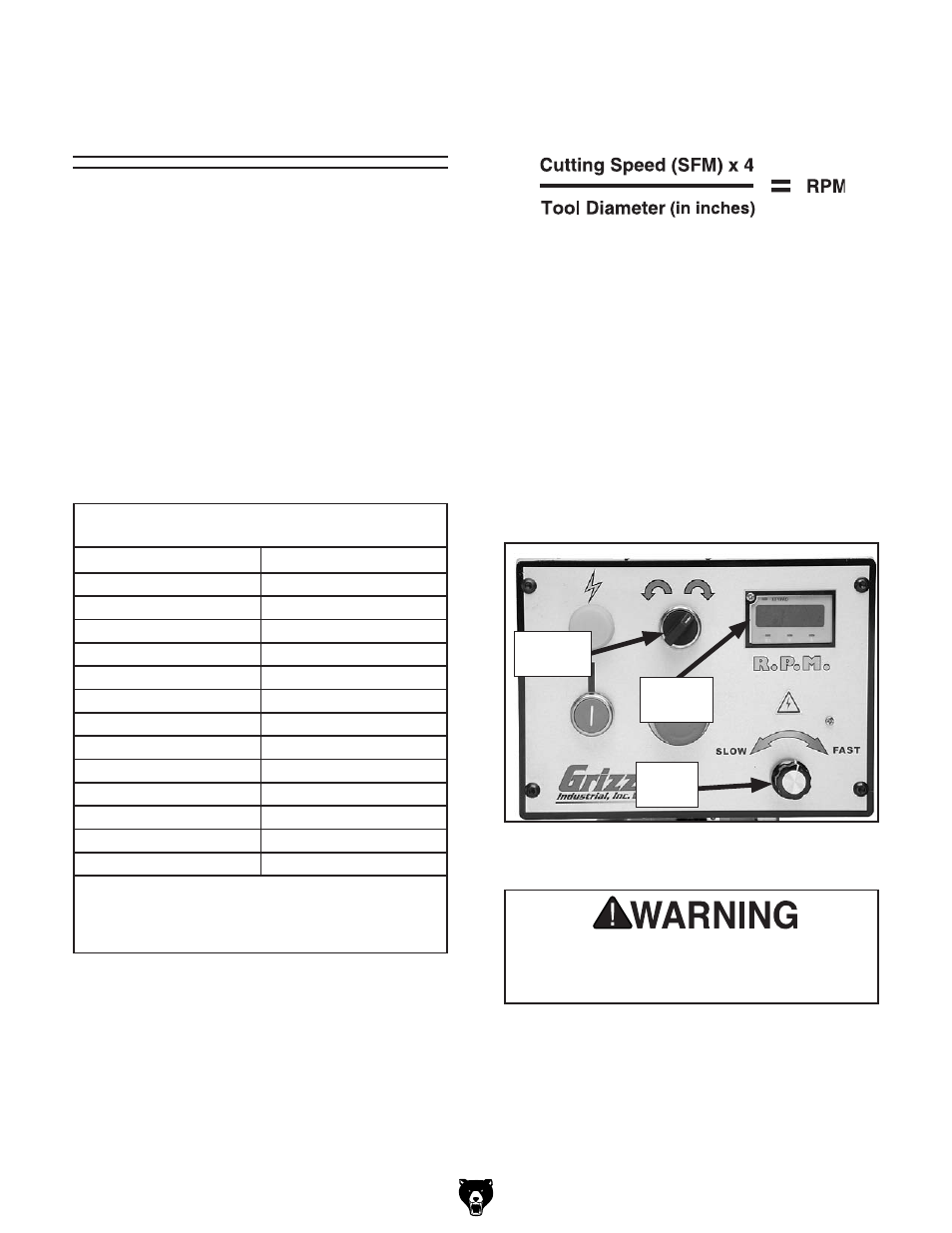
-28-
model g0695 (mfg. since 9/10)
Setting Spindle
Speed
to select the correct spindle speed (rpm) for your
milling operation, you will need to: 1) determine
the spindle speed needed for your workpiece, and
2) set the speed dial for the calculated speed.
this mill is designed to use most end mills, drill
bits, and face cutters that are 3" in diameter
or less. the milling table has a coolant system
trough with drain for an optional fluid system.
Calculating Spindle Speed
1. Use the table in figure 29 to determine the
cutting speed or surface feet per minute
(sFm) required for your workpiece material.
Cutting Speeds for High Speed Steel (HSS)
Cutting Tools
Workpiece material
Cutting speed (sFm)
aluminum & alloys
300
Brass & Bronze
150
Copper
100
Cast iron, soft
80
Cast iron, hard
50
mild steel
90
Cast steel
80
alloy steel, hard
40
tool steel
50
stainless steel
60
titanium
50
plastics
300-800
Wood
300-500
Note: For carbide cutting tools, double the cutting
speed. These values are a guideline only. Refer to
the MACHINERY'S HANDBOOK for more detailed
information.
figure 29. Cutting speed table for hss cutting
tools.
3. Use the following formula to calculate the
required spindle speed (rpm) for your opera-
tion:
Setting Spindle Speed
1. rotate the speed dial all the way to the left,
setting the startup spindle speed close to
zero.
Note: This precaution avoids unexpected
high speed startup of the spindle.
2. Use the direction switch to select the direc-
tion of spindle rotation, turn the spindle
ON,
then rotate the speed dial until the calculated
spindle speed is displayed at the digital read-
out on the control panel (see
figure 30).
figure 30. spindle direction switch, speed dial,
and digital readout.
digital
readout
direction
switch
speed
dial
2. measure the diameter of your cutting tool in
decimal inches.
failure to follow spindle speed and feed rate
guidelines may threaten operator safety
from ejected parts or ejected tools.
Remember: Milling with the quill fully extended
can cause tool chatter. For maximum spindle
rigidity, keep the spindle retracted into the head-
stock as far as possible with the quill lock lever
locked and the downfeed selector tightened.