HONDA Insight User Manual
Page 79
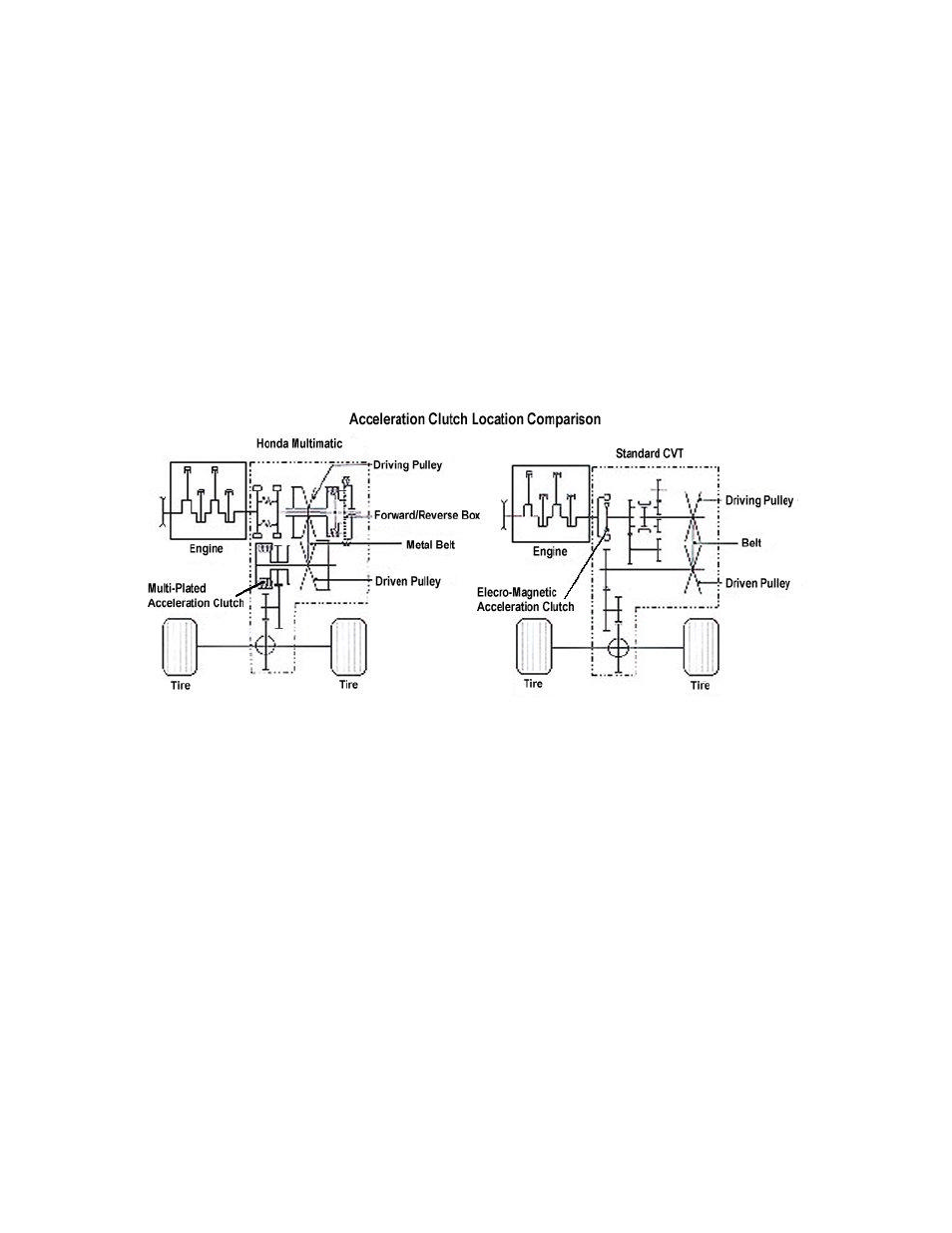
79
1) Driven-Shaft-Placed Acceleration Clutch
The Honda Multimatic differs from previously existing step-less transmissions is that the acceleration
clutch is placed on the driven shaft. The primary reason we took this route was to control torque at the
closest possible place to the axle, allowing for smooth acceleration. In addition, we were able to apply a
modest creep* which most automatic transmission users have grown accustomed to. This gives the standard
advantages of an automatic when parking, as well as starting from a dead-stop on hills. (*creep - you know,
how your car with AT will sneak/creep forward unless you apply the brakes)
Secondly, this allows for controlling the speed in all circumstances. In order to control speed, the
pulley needs to be continually spinning. By placing the clutch on the driven pulley, the pulley can remain
spinning even when the car is stopped. This means that in emergency situations or sudden deceleration, the
transmission can quickly step down to LOW gear.
Lastly, this set-up allows for the transmission to be towed. When the engine is stopped, the input from
the tires is locked out by the final gear and the driven pulley.
2) Proprietary Oil Pressure Control System
The pulley width and speed control is handled by a high/low pressure regulator. The four-way valve
releases oil pressure evenly to the pulleys. Additionally, the force that pinches the metal belt between the
pulleys is also controlled by the lower pressure regulator. As a result, the two pulley pistons are of the same
design - allowing for a more simple design, yet allowing high power output as needed.
3) Slim Design
The Front/Reverse switching mechanism was placed on the driving shaft, while the acceleration clutch
was placed on the driven shaft. Because of this opposing setup, the transmission is very compact, making it
ideal for a FF layout. Additionally, the input shaft from the engine is inserted into the driving shaft,
allowing for the number of bearings to be decreased - which ultimately means less power lost to friction.
4) Dual Flywheels
We removed the torque converter, and instead sandwiched two flywheels - resulting in a dual-mass
flywheel. Also, the harmonic resonance frequency was lowered to that of below idle - allowing us to shut
out the unwanted vibrations often caused by the twisting force generated by the engine during torque rate