Installation, Manual operation, Maintenance – Marwin Valve 10000 Series Soft Seated Ball Valve User Manual
Page 2
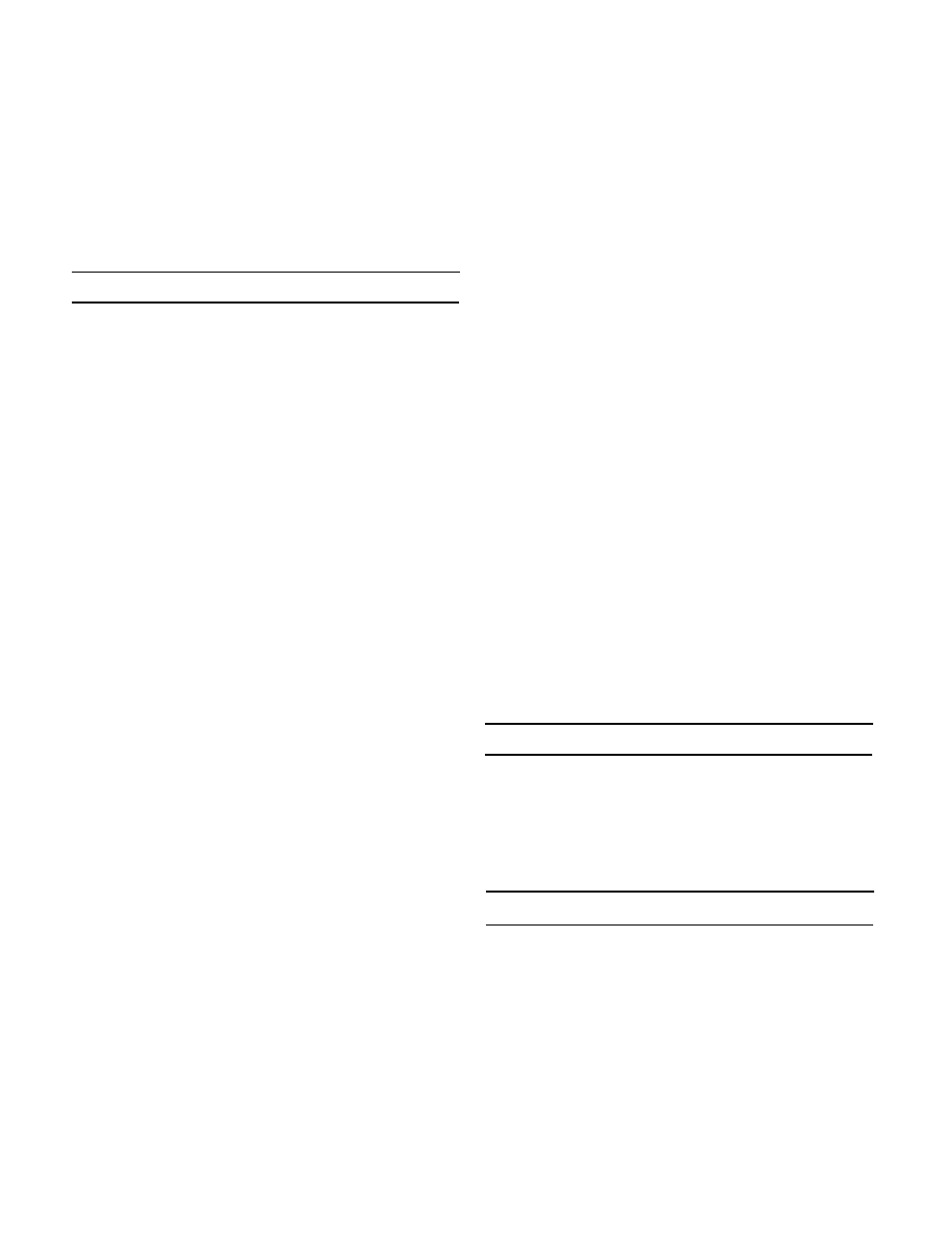
Maintenance During Storage Period
Internal surface should be inspected to check for
•
dust or other foreign objects.
Rust or dust must be removed by cleaning with
•
proper solvent.
After cleaning, ball valves must be lubricated with
•
an adequate lubricant.
Ball valves should be operated for at least two
•
complete cycles before installing or returning to
storage.
Installation
The ball valves may be installed in any position using
standard pipe fitting practices.
Caution: Before installation of the valve:
Pipe must be free of tension both during and
1.
after installation.
Pipe must be flushed to clean dirt, welding
2.
residues, etc. which would damage ball or
seats.
The valve should be kept in OPEN POSITION
3.
during installation and protective plastic
covers must be removed only at the moment of
installation.
Before shipment, the ball is lubricated with a
4.
pure Vaseline oil. This can be easily removed
with an application compatible solvent if
required.
If the valve was specified to be tested per ASTM
5.
16.34, there may be some trapped water be-
tween the ball and the body cavity. This can be
removed by partially opening the valve, thereby
exposing the cavity to the through port of the
ball.
Special care should always be taken when
6.
installing automated ball valves that the ball is in
the proper position.
Installation of Threaded-Ends
Unless otherwise specified, pipe threads are
1.
American National Standard Taper Pipe Threads
(NPT) per ANSI B1.20.1, and require that a pipe
sealant be used.
Use an anti-seize thread sealant to seal and pre-
2.
vent galling.
a. Marwin recommends PTFE-based liquid sealant
or Grafoil tape as thread sealants.
b. Notes:
1.Use all pipe sealant products in accordance
with the manufacturer’s instructions and good
piping practices.
2. Correct lubrication of stainless steel pipe threads
in especially important to prevent galling.
To prevent distortion or damage to the valve, do not
3.
apply torque through the valve. When tightening
valve, use wrench on the end nearest the pipe being
tightened.
Always leak test the system before using.
4.
Installation of Welded-End Ball Valves
Tack weld in four points on both end caps.
1.
Lift out the valve body and seat per disassembly
2.
section in this procedure and complete the welding.
Allow welds to cool.
3.
Reassemble valve per section in this procedure and
4.
inspect for easy operation.
Extended end valves may be welded into place with-
5.
out disassembly using the following guidelines:
a. Valve must be in the full open position
b. Limit continuous weld time to one minute.
c. Direct moving air across finned area or wrap
extended end with wet cloth.
d. Check body bolts for proper torque after welds
have completely cooled per Assembly Section of
this procedure.
Note: Guide for extended valve installation does not
apply to UHMW-PE or Delrin seats or standard EPDM
or Nitrile body seals due to the low tolerance to high
temperatures of these materials.
Installation of Flanged Ends
Verify valve is in the full open position.
1.
Use the appropriate size bolt and heavy hex nut
2.
(not included) as recommended for flange size and
class.
Flange connection requires gasket (not included).
3.
Follow gasket manufacturer’s recommended prac-
4.
tice for tightening flange bolts.
Manual Operation
Open and close the valve by turning the handle one-
1.
quarter turn (90°).
Valve is in open position when handle is in line with
2.
the pipe.
Valve is in closed position when the handle is per-
3.
pendicular to the pipe.
Maintenance
Before starting maintenance, please read information
contained in the Caution Section of the manual.
Open and close the ball valve at least once to
1.
release the pressure completely from valve body.
Ball valves, if correctly used, normally do not
2.
need any internal lubrication and maintenance.
However, when necessary, ball or seats can be
replaced by qualified personnel following the
instructions of this manual.
For further information, please refer to
3.
SPARE
PARTS LIST
.