Manual operation, Maintenance, Valve disassembly – Marwin Valve MS3000 Series High Performance Valve User Manual
Page 2
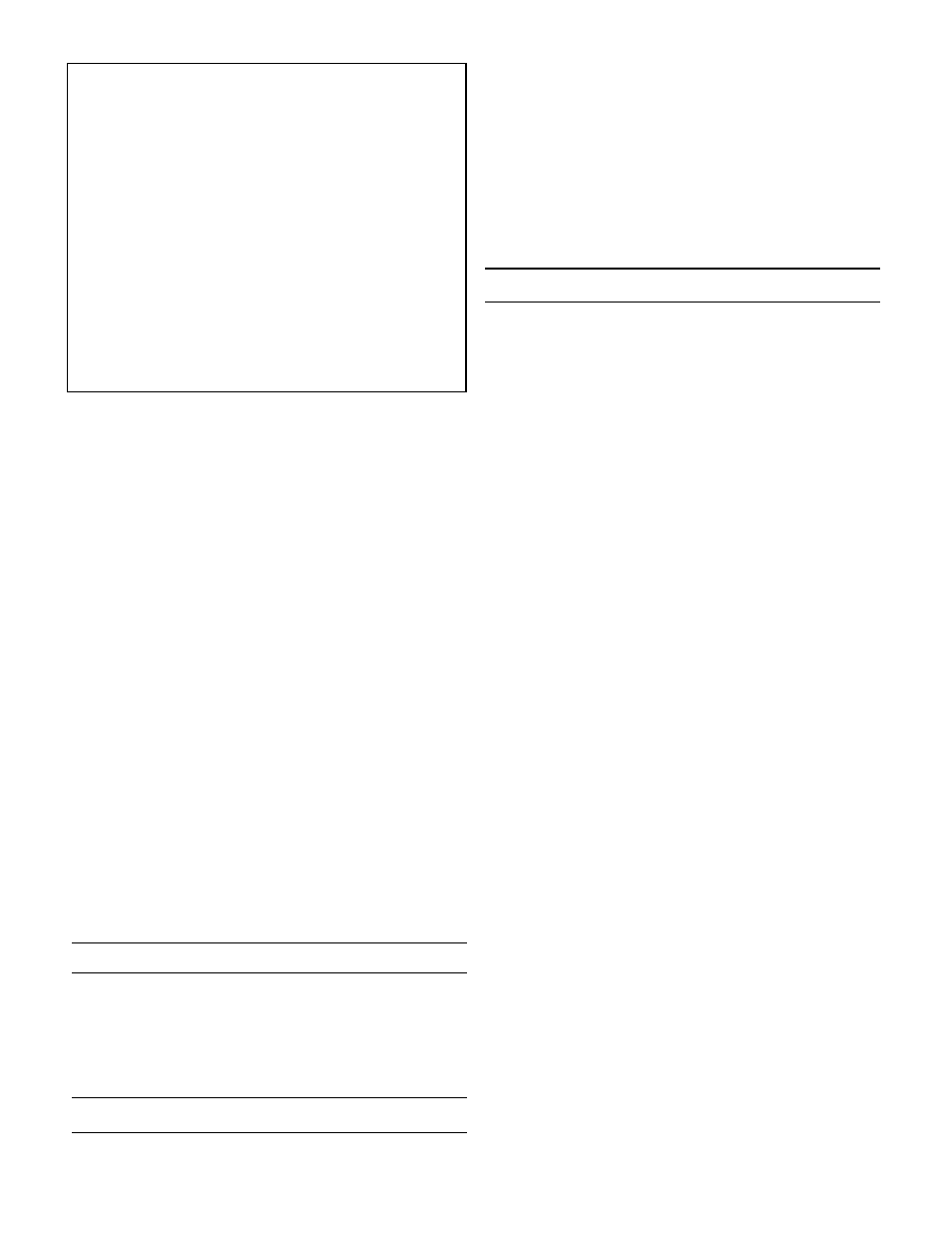
CAUTION: Before installation of the valve:
Pipe must be free of tension both during and after in-
1.
stallation.
Pipe must be flushed to clean dirt, welding residues,
2.
etc. which would damage ball or seats.
The valve should be kept in OPEN POSITION during
3.
installation and protective plastic covers must be re-
moved only at the moment of installation.
Before shipment, the ball is lubricated with a petro-
4.
leum based oil. This can be easily removed with an
application compatible solvent if required.
If the valve was specified to be tested per ASTM 16.34,
5.
there may be some trapped water between the ball
and the body cavity. This can be removed by partially
opening the valve, thereby exposing the cavity to the
through port of the ball.
Special care should always be taken when installing
6.
automated ball valves that the ball is in the proper posi-
tion.
Installation of Threaded Ends
Unless otherwise specified, pipe threads are per ANSI
1.
B1.20.1 and require applicable pipe sealant.
Install valve using standard piping practices.
2.
When tightening valve, apply wrench to the end cap
3.
nearest the pipe being worked on.
Extended Weld End Valves
The standard weld end connections (female socket and butt
weld versions) are extended ends (ANSI 300# face to face)
with integral cooling fins to dissipate the heat associated with
the welding process. This allows most valves to be welded in-
line without disassembly, given the following guidelines.
Valve must be in the full open position.
1.
Limit continuous weld time to 1 minute.
2.
Direct moving air across finned area, or wrap extended
3.
end with wet cloth.
Body bolts are checked for torque after complete cooling
4.
of weld area per Re-Assembly Section of this manual.
Installation of Flanged-Ends
Verify valve is in the full open position.
1.
Use the appropriate size bolt and heavy hex nut (not in-
2.
cluded) as recommended for flange size and class.
Flange connection requires gasket (not included).
3.
Follow gasket manufacturer’s recommended practice for
4.
tightening flange bolts.
Manual Operation
Open and close the valve by turning the handle ¼ turn
1.
(90°).
Valve is in open position when handle is in line with the
2.
pipe.
Valve is in closed position when the handle is perpen-
3.
dicular to the pipe.
Maintenance
Before starting maintenance, please read information con-
tained in the Caution Section of the manual.
Open and close the ball valve at least once to release the
1.
pressure completely from valve body.
Ball valves, if correctly used, normally do not need any
2.
internal lubrication and maintenance. However, when
necessary, ball or seats can be replaced by qualified per-
sonnel following the instructions of this manual.
For further information about recommended SPARE
3.
PARTS LIST, please check drawing, catalog, or contact the
factory.
Valve Disassembly
The MS3000 Series valves seat require special care when try-
ing to repair in-line. If possible, the valve should be removed
intact from the pipeline before disassembly (step 4 can be then
be omitted). If ends have been welded in place and not remov-
able, follow these steps (see warnings on page 1):
Operate valve to full open position. (The ball will extend
1.
into end caps in the closed position).
Remove all body bolts.
2.
Separate ends (up to ¼” per side), to allow body to clear
3.
end cap lips. (Take care not to damage body seal contact
seal surfaces on end caps).
Remove body center section and valve seats from end
4.
caps.
Close valve and remove ball (protect ball).
5.
Remove handle for manual valves, or bracket and coupler
6.
if automated.
Remove body gaskets/o-rings and emergency gaskets/
7.
o-rings from body. Some gasket materials may require
“picking” from groove, be careful not to scratch metal
mating surface.
Remove stem nut and packing gland(s) remove bon-
a.
net bolts and push upper stem down thru bonnet.
Now that the packing ID has been exposed, carefully pry
8.
out old packing and thrust washer(s).
Inspection and Replacement
With the valve completely disassembled, clean and examine all
components:
The surface of the ball should be free from any defect.
1.
If any are found, the ball should be replaced. Using a
defective ball will be extremely detrimental to valve per-
formance.
Seats: Replacement of seats is recommended if they
2.
have been damaged or the coating has been worn
through.
Seat seals and body seals: Should be discarded and
3.
replaced.
Remaining components of the valves: After cleaning,
4.
carefully examine for wear, corrosion, and mechanical
damage. Replace all defective parts.
Clean inside of body and stem housing. Light grease,
5.
compatible with line fluid, can be used on ball, seals and
stem surfaces.
NOTE: A spare parts list is available for this valve. See figure
for identification. Please specify valve number to ensure
proper parts are ordered.
-2-