Start-up procedure, Troubleshooting, Maintenance – Jordan Valve Mark 87 Series - Piloted Temperature Regulator User Manual
Page 2: Bulb installation
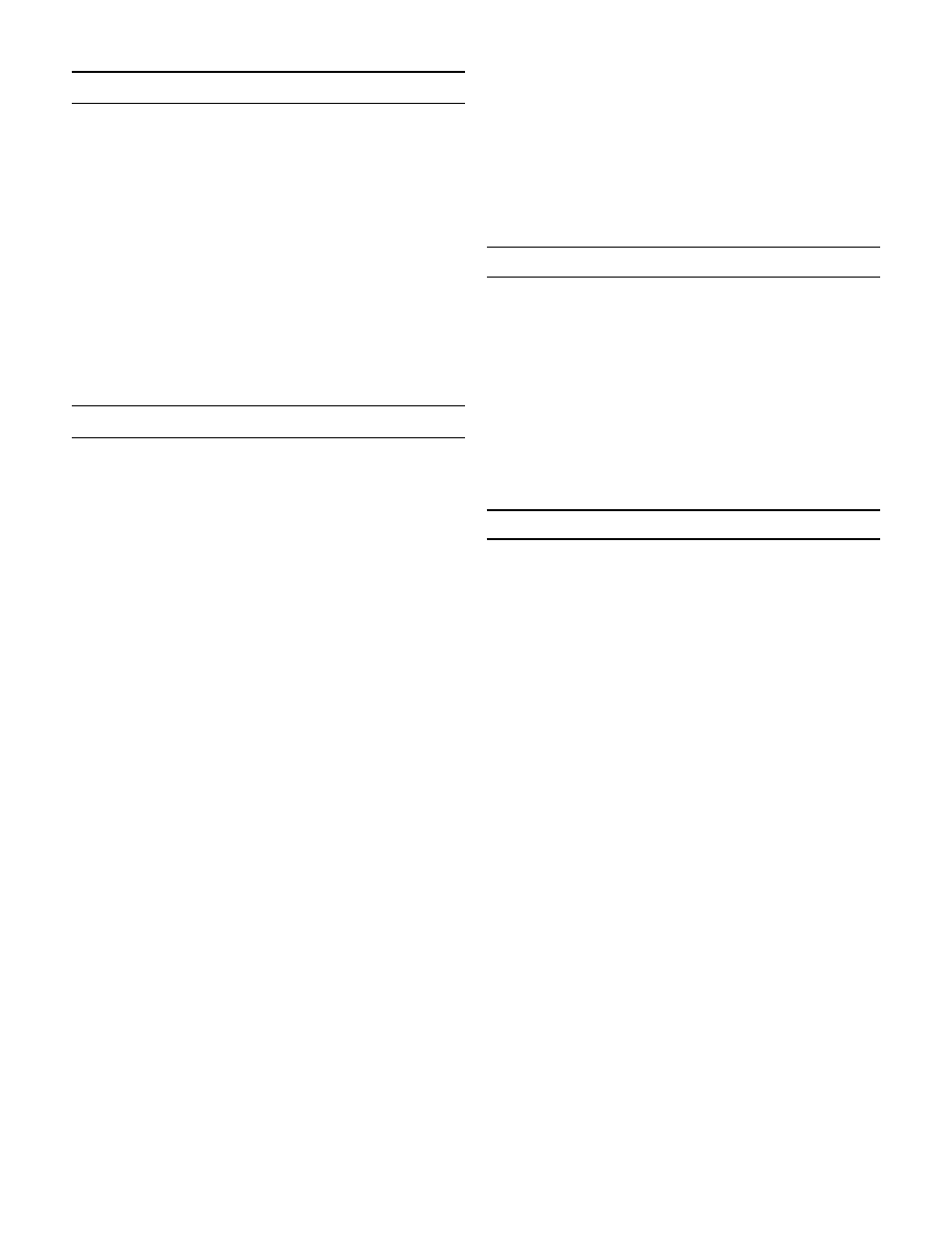
Start-Up Procedure
With the inlet, outlet and by-pass shut-off valves closed:
Fully open the outlet shut-off valve
1.
Slowly open the inlet valve just enough to start flow
2.
through the regulator. Observe the downstream
pressure gauge. Increase the downstream pressure
slowly by gradually opening the inlet valve.
Do not fully open the inlet valve until you are sure
3.
that the regulator has control of the system. Usu-
ally, the handwheel on the inlet valve will turn freely
when this point is reached.
To change the controlled temperature, rotate the
4.
adjusting wheel on the pilot valve upward to in-
crease the temperature, and downward to crease
the temperature.
Troubleshooting
Insufficient Heating (or Cooling)
1.
A valve undersized for the application. Check capac-
•
ity required and valve capacity.
Line strainer or pilot strainer screen could be
•
clogged. Blow down strainers or visually check that
they are clear.
Incorrect setting on range spring. Vary the setting
•
and check response.
Main valve diaphragm may be ruptured. See section
•
on main valve maintenance.
Malfunction of other piping components. Check for
•
leaking traps and safety valves, inadvertently opened
or closed valves.
Overheating (or Cooling)
2.
Incorrect setting on range spring. Vary the setting
•
and check response.
Pilot valve or main valve seats leaking. Close inlet
•
shut-off valve, allow downstream pressure to bleed
off, close outlet valve and remove loading pres-
sure tubing. FOR HEATING APPLICATION: Heat the
sensing bulb to approximately 20° - 30°F above the
control point and/or reduce the compression of the
adjusting spring to guarantee that the pilot valve is
stroked closed. FOR COOLING APPLICATION: Cool
the sensing bulb to approximately 20° - 30°F below
the control point and /or increase the compression
of the adjusting spring to guarantee that the pilot
valve is stroked closed. Crack open inlet shut-off
valve - if fluid issues from pilot valve point, the pilot
seats are leaking. If the fluid issues from the main
valve port, the main valve seats are leaking.
By-pass shut-off valve leaking. During period of leak-
•
age, close outlet shut-off valve, observe thermometer.
Bleed port in main valve clogged. Remove Upper
•
Bonnet to gain access to bleed port and clean bleed
-2-
port. Follow instructions in section “To Remove Main
Diaphragm”.
Thermal System Failure. See Series 80 I & M Sheet.
•
Controlled Temperature Fluctuates
Valve oversized. Check capacity required and valve
•
capacity.
Maintenance
WARNING: Be sure that there is no pressure in the
valve before loosening any fittings or joints. The fol-
lowing steps are recommended.
Close inlet shut-off valve.
1.
Allow pressure to bleed off through downstream
2.
piping. Do not cause a reverse flow through valve by
bleeding pressure from upstream side of valve.
When downstream pressure gauge indicates no
3.
pressure in the line, close the outlet shut-off valve.
Close the control line shut-off valve.
4.
Bulb Installation
The Thermal System is a hermetically sealed unit consist-
ing of a sensing bulb, capillary tubing, protective armor,
and actuator assembly. This unit contains the thermo-
static charge that operates the temperature regulator.
Please do not tamper with it. In case the charge is lost,
the thermal system must be replaced as a complete unit.
It is not repairable in the field and must be returned to
the factory for repairs.
Correct Installation
1.
- For effective temperature control
installation of the sensing bulb is essential. For best
results, the bulb should be installed at a point of true
representative temperature and where there is good
circulation. A thermometer or other temperature
sensing device (if used) should be placed as close as
possible to the sensing bulb of the regulator.
Handle the capillary and armor carefully so they are
2.
not crushed, kinked or twisted. A bend of 4-1/2”
radius or larger is recommended.
Horizontal Mounting
3.
- When the bulb is to be
mounted horizontally, it must be turned so that the
word TOP and center punch mark (stamped on the
adapter) faces upward.
Vertical Mounting
4.
- No special precaution is required
when the bulb is mounted vertically pointing down.
Inverted Mounting
5.
- A special capillary is required
if the tip of the bulb will be higher than the capil-
lary end. The temperature regulator equipped with