Jordan Valve Mark 67 Series – Piloted Sliding Gate Regulator User Manual
Ideal installation, Control line
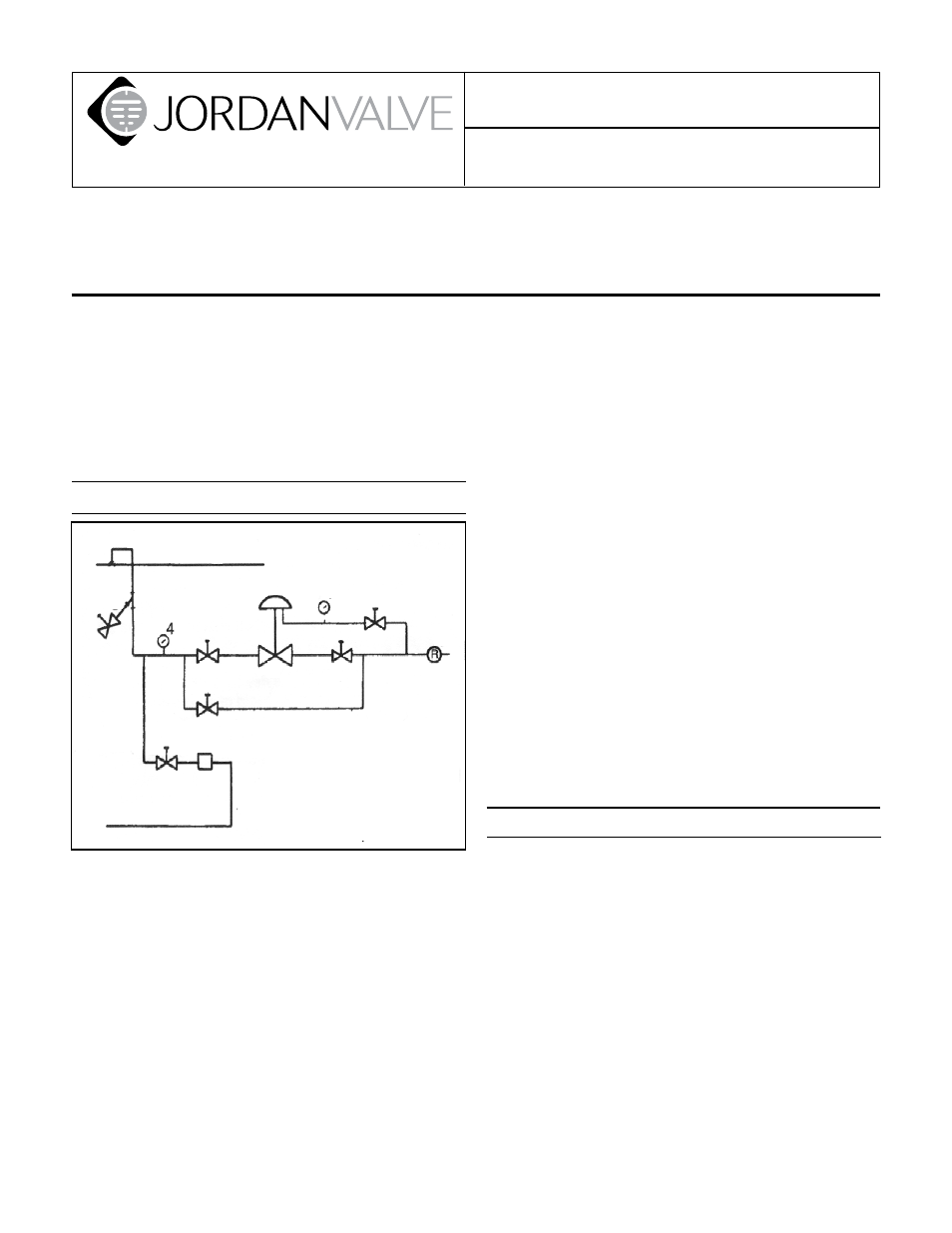
3170 Wasson Road • Cincinnati, OH 45209 USA
Phone 513-533-5600 • Fax 513-871-0105
[email protected] • www.jordanvalve.com
I & M Mark 67 (1/2” – 6”)
Installation & Maintenance Instructions for
Mark 67 Pressure Regulators
Warning: Jordan Valve pressure regulators must only be used, installed and repaired in accordance with these
Installation & Maintenance Instructions. Observe all applicable public and company codes and regulations. In the
event of leakage or other malfunction, call a qualified service person; continued operation may cause system failure
or a general hazard. Before servicing any valve, disconnect, shut off, or bypass all pressurized fluid. Before disas-
sembling a valve, be sure to release all spring tension.
Please read these instructions carefully!
Your Jordan Valve product will provide you with long,
trouble-free service if it is correctly installed and main-
tained. Spending a few minutes now reading these in-
structions can save hours of trouble and downtime later.
When making repairs, use only genuine Jordan Valve
parts, available for immediate shipment from the factory.
Ideal Installation
1.
To protect the valve from grit, scale, thread chips
and other foreign matter, ALL pipelines and piping
components should be blown out and thoroughly
cleaned before the installation process begins.
2.
Shutoff valves, pressure gauges and by-pass piping
should be installed as indicated in the diagram to
provide easier adjustment, operation, and testing.
3.
A line strainer should be installed on the inlet side
of the valve to protect it from grit, scale and other
foreign matter. A 0.033 perforated screen is usually
suitable for this purpose. Line strainers are avail-
able from Jordan Valve.
4.
For best control, 3’0” straight sections of pipe
should be installed on either side of the valve.
5.
In preparing threaded pipe connections, care
should be exercised to prevent pipe-sealing com-
pound from getting into pipelines. Pipe-sealing
compound should be used sparingly, leaving the
two end threads clean. Jordan uses, and recom-
mends, thread sealer Teflon ribbon.
6.
The flow arrow on the valve body must be pointed
in the direction of flow. Ideally, the valve should be
installed in the highest horizontal line of piping to
provide drainage for inlet and outlet piping, to pre-
vent water hammer, and to obtain faster response.
7.
If possible, install a relief valve downstream from
the valve. Set at 15 psi above the control point of
the valve.
8.
In hot vapor lines, upstream and downstream pip-
ing near the valve should be insulated to minimize
condensation.
9.
In gas service, expand the outlet piping at least
one pipe size if the control pressure (downstream)
is 25% of the inlet pressure or less. A standard
tapered expander connected to the outlet of the
valve is recommended.
10. Where surges are severe, a piping accumulator is
recommended.
11. On steam control applications, install a steam trap
with sufficient capacity to drain the coil or condens-
er. Be sure to have a good fall to the trap, and no
backpressure. Best control is maintained if the coil
or condenser is kept dry.
Control Line
A control line must be installed as follows:
1.
Connect one end of a 3/8” tubing to the fitting un-
der the diaphragm.
2.
Connect the other end in a straight run of pipe 3 to
5 feet downstream of the valve.
3.
DO NOT locate the control line tap in an elbow,
swage or other changes in configuration of the
pipeline where turbulence or abnormal velocities
may occur.
4.
DO NOT locate the control line tap in vessel, such
as a deaerator located immediately downstream of
the valve. Locate the tap in the pipeline leading to
the vessel.
5.
The control line should be sloped away from the
valve.
6.
Install a shutoff valve (not a needle valve) in the
control line.
Main Steam Line
Condensate Return Line
1. Shut off Valve
2. Jordan Regulator
3. Strainer and Drain Valve
4. Pressure Gauge
5. Relief Valve
6. Steam Trap
1
6
3
1
1
2
1
5
4