Yaskawa F7 Drive Technical Manual Orientation User Manual
Page 7
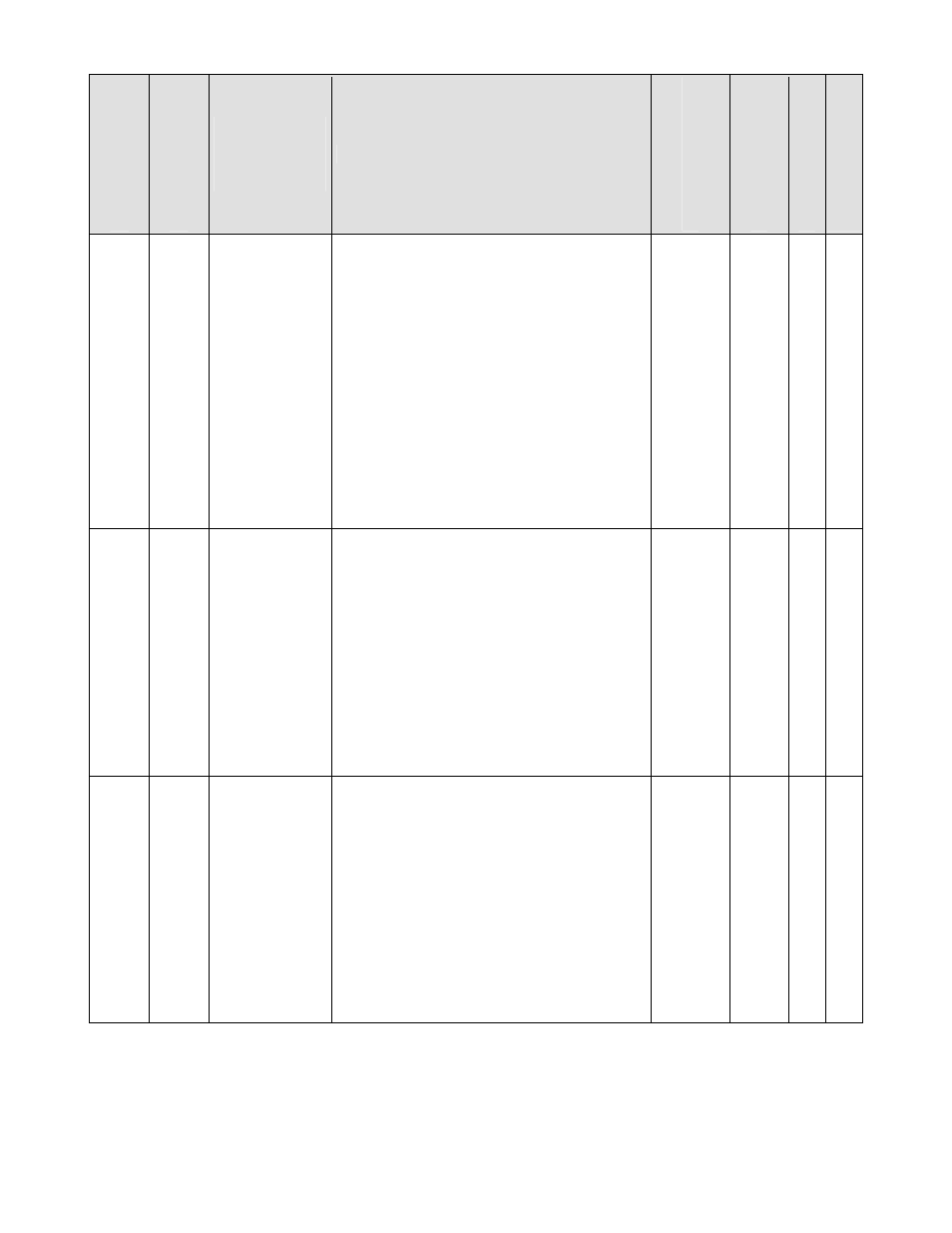
Date: 03/03/06, Rev: 06-03
Page 7 of 16
TM.F7SW.063
4.1 Parameters (continued)
Parameter Number
Modb
us Addr
e
ss
Parameter Name
Digital Operator
Display
Description
Ran
ge
Default
Cha
nge D
uri
ng
Run
Access Level For All
Contro
l Modes
*1
P2-05 60EH
Motor Gear Ratio
1
Motor Ratio 1
This parameter sets gear ratio 1 between the
driven motor shaft and the orientation encoder. A
setting of 2.0000 means that there are 2 motor
shaft revolutions for every one revolution of the
orientation encoder.
The exact ratio must be able to be expressed by
this parameter. If not, over time the machine will
drift away from the desired orient position as error
builds up from the mis-expressed ratio.
This parameter is used in conjunction with
parameters P2-06 and P2-07 to determine the
active motor gear ratio. See section 5.2 for
details. If neither of the multi-function input
functions 86 or 87 (Motor Gear Ratio Selection 1
or 2) are programmed, P2-05 is the active
parameter.
0.0400 ~
2.5000
1.0000
No A
P2-06 60FH
Motor Gear Ratio
2
Motor Ratio 2
This parameter sets gear ratio 2 between the
driven motor shaft and the orientation encoder. A
setting of 2.0000 means that there are 2 motor
shaft revolutions for every one revolution of the
orientation encoder.
The exact ratio must be able to be expressed by
this parameter. If not, over time the machine will
drift away from the desired orient position as error
builds up from the mis-expressed ratio.
This parameter is used in conjunction with
parameters P2-05 and P2-07 to determine the
active motor gear ratio. See section 5.2 for
details.
0.0400 ~
2.5000
1.0000
No A
P2-07 610H
Motor Gear Ratio
3
Motor Ratio 3
This parameter sets gear ratio 3 between the
driven motor shaft and the orientation encoder. A
setting of 2.0000 means that there are 2 motor
shaft revolutions for every one revolution of the
orientation encoder.
The exact ratio must be able to be expressed by
this parameter. If not, over time the machine will
drift away from the desired orient position as error
builds up from the mis-expressed ratio.
This parameter is used in conjunction with
parameters P2-05 and P2-06 to determine the
active motor gear ratio. See section 5.2 for
details.
0.0400 ~
2.5000
1.0000
No A
*1: Access Level (A1-01): Q = “Quick Start”, A = “Advanced”, F = “Factory”.