Program control handles – Yaskawa MotionWorks IEC User Manual
Page 7
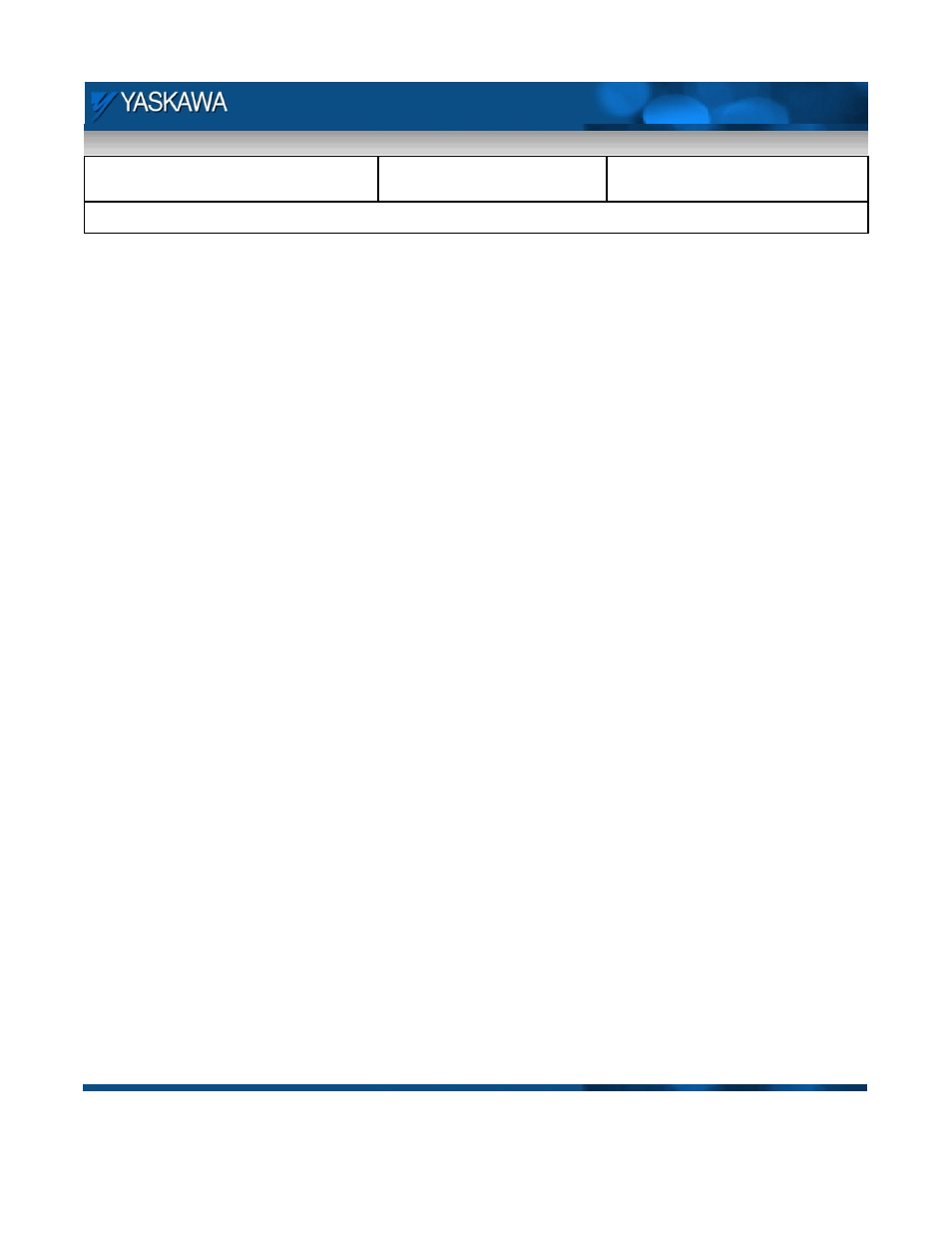
Subject: Example Code Manual
Product: MP2300Siec and
MotionWorks IEC
Doc#: EM.MCD.08.011
Title: Feed-to-Length Application using MC_TouchProbe for Position Latching
October 24, 2008
Page 7 of 10
4. Program Control Handles
1) Output 2 in a high state indicates an alarm on the axis. This can be cleared using Input 6, which resets
the alarm. If reset fails, controller/servopack power will have to be cycled.
2) If there are no alarms, Input 1 enables the feed axis.
3) Input 2 in a low state indicates manual mode and jogging or homing can be accomplished.
4) Input 3 jogs the axis and does so until input 3 is turned off.
5) Input 4 in a high state starts the homing routine. The axis runs until it encounters a signal on the EXT 1
input of the servopack. At this signal, the axis stops. After a delay, the axis moves slowly to stop at the C
channel position of the axis encoder. After homing is completed, turn input 4 off.
6) Input 5 starts automatic production. However, for auto production to start, the controller should be in auto
mode (Input 2 high). Also, auto start is possible only after the homing routine has been accomplished.
Autostart (Input 5) gets the axis moving. On encountering a part (latched EXT 1 signal), the move is
aborted by another relative move. The axis then moves a predefined distance and stops. The axis
restarts the cycle after a small predefined pause. This continues until input 5 is turned off. If no part is
encountered after a predetermined variable ‘part length’, Output 1 turns on indicating an alarm. This can
be cleared, so the cycle can be restarted by cycling Input 5.