Yaskawa MotionWorks IEC User Manual
Page 6
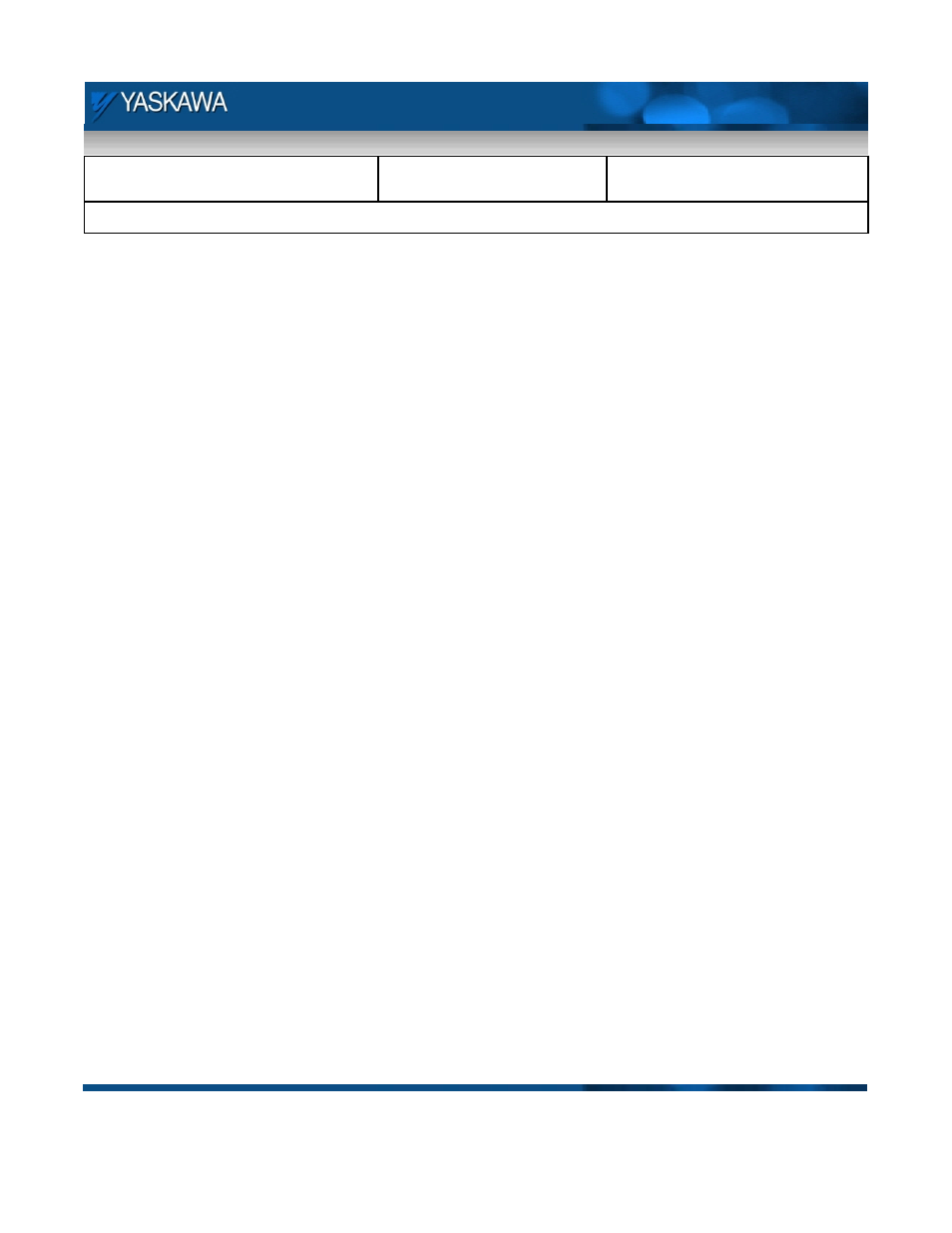
Subject: Example Code Manual
Product: MP2300Siec and
MotionWorks IEC
Doc#: EM.MCD.08.011
Title: Feed-to-Length Application using MC_TouchProbe for Position Latching
October 24, 2008
Page 6 of 10
2. Interface: This program assigns the 6 inputs to the input variable names. The two outputs are also
defined in this program.
Attribute: Makes use of structured text for definitions
3. Interlocks: This program enables the various modes of operation. The two main modes are manual and
automatic. In manual mode, the axis can be jogged and homed to the C channel of the encoder. In
automatic mode, the axis can be used for part production. The interlocks for various modes, and how
they synchronize with the inputs and outputs, can be seen in this program.
Attribute: Makes use of structured text for definitions
4. EnableAxis: This program controls the axis enabling sequence. The axis gets enabled only if there are
no axis errors. This program also controls clearing any alarms that may be present on the axis before
enable is carried out.
Attribute: MC_Power, MC_ReadAxisError, MC_Reset
5. JogProgram: This program provides function blocks for the jog routine.
Attribute: MC_MoveVelocity, MC_Stop
6. HomeProgram: This program controls the home routine, which can be activated in manual mode. The
axis is driven in a negative direction, until a marker on the axis belt is seen. The axis is stopped and after
a time delay, the axis moves to the closest c channel and stops.
Attribute: MC_MoveVelocity, MC_Stop, MC_StepRefPulse
7. AutoProduction: This program controls the automatic production. On enabling the auto mode and
starting production, the axis continues motion until a part is sensed. The axis location is then latched.
The first motion is aborted and a new relative motion is executed, bringing the axis to rest at a desired
distance after the axis latch position.
Attribute: Uses ladder logic for various interlocks. Uses rising and falling edge detectors, timers.
MC_MoveRelative, MC_TouchProbe