Torque value table, Reassembly precautions, General installation guidelines – Bestobell Steam TS22 Series User Manual
Page 2
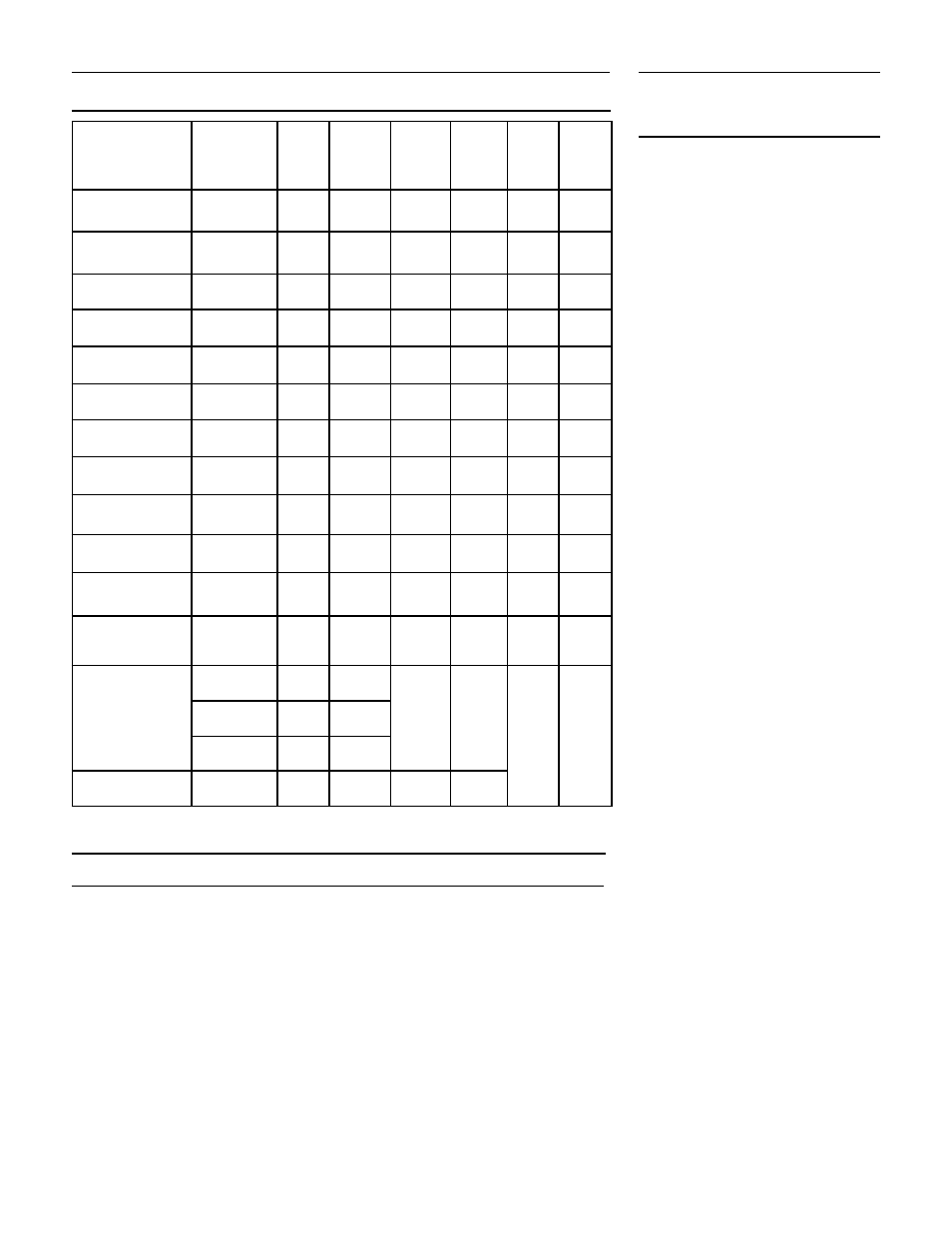
Torque Value Table
Model
Sizes inches
(DN)
Cover
Fittings
FT/Lbs
(N-m)
Wrench
Size in
Strainer
Cap
Ft/Lbs
(N-m)
Wrench
Size in
Valve
Seat
Ft/Lbs
(N-m)
Wrench
Size
mm
DMR6
1/2”-3/4”
DN15-20
120
(162,7)
1-1/4
N/A
N/A
20
(27,1)
17
3A, 6A, 10, 22,
GM3/6/10, DM25
3/8”-3/4”
DN10-20
15
(20,3)
1/2
50
(67,8)
1-3/16
or 1-1/4
30
(40,7)
22
16/25/40
1/2”-3/4”
DN15-20
30
(40,7)
5/8
11/16
70
(94,9)
1-3/8
30
(40,7)
22
GM16/25
1/2”-3/4”
DN15-20
30
(40,7)
5/8
11/16
70
(94,9)
1-3/8
35
(47,5)
27
16/25/40
GM3/6/10
1”
DN25
25
(33,9)
5/8
11/16
90
(122,0)
1-1/2
35
(47,5)
27
16/25 GM10
1-1/4”-2”
DN32-50
110
(149,1)
1-1/8
1-1/4
170+
(230,5+)
2
62
(84,1)
41
GM3/6
1-1/4”-1-1/2”
DN32-40
110
(149,1)
1-1/8
1-1/4
170+
(230,5+)
2
65
(88,1)
41
GM3/6
2”
DN50
25
(33,9)
3/4
7/8
170+
(230,5+) 7/8” SQ
80
(108,5)
50
DM64/100
1/2”-1”
DN15-25
50
(67,8)
7/8
70
(94,9)
1-7/16
35
(47,5)
27
40/64/100
1-1/2”-2”
DN40-50
85
(115,2)
1-1/4
170+
(230,5+)
2
65
(88,1)
41
DM160 DM320
All
90
(122,0) 1-7/16
N/A
N/A
35
(47,5)
27
TM22 DM6/12
DM10E
All
12
(16,3)
1/4 allen
1/2
N/A
N/A
20
(27,1)
17
Multi-element
Magnums
Small
80
(108,5)
3/4
N/A
N/A
80
(108,5)
80
Medium
160
(216,9) 15/16
Large
280
(379,6)
1-1/8
Single Element
1-1/2”-2”
DN40-50
110
(149,1)
1-1/4,
1-1/8
Note: Where 2 wrench sizes are shown, one is bolt size, one is wrench size
ReAssembly Precautions
Lubricate all bolts, strainer cap, and control element threads with anti-
•
seize compound.
Install control element gasket.
•
Follow all instructions on back cover of this brochure, and always install
•
new gasket.
On bonnet-to-bonnet joint: bring bolts to hand tight.
•
Torque to 100% of specified torque.
•
Check bolt torques directly following the steam test.
•
On DMR6 with copper gasket, torque to 50%, loosen and torque to
•
100%.
General Installation
Guidelines
For top performance of any
steam trap, the pipework must
be designed to provide the best
condensate flow possible to the
steam trap. To achieve this, follow
the general guidelines shown
below:
Where possible, arrange the
•
piping such that condensate
flows to the trap by gravity.
Trap each piece of equipment
•
separately.
Locate the trap at the lowest
•
point, preferably below the
equipment outlet.
On most applications, the trap
•
should be 2 to 5 lineal feet
from the equipment outlet.
Arrange piping and trap loca-
•
tion to be easily accessible for
inspection and repair.
Bestobell traps have very high
•
cold start-up capacities. Install
bypasses only if required for
maintenance.
Shutoff valves, unions and
•
test “tee” after a trap should
be installed to provide easier
operation, maintenance, and
testing.
Check all pipe sizes to prevent
•
restricted flows, especially in
condensate return lines. Un-
dersized returns are a major
cause of poor system perfor-
mance.
Insulation after the trap is ide-
•
al, but do not insulate the trap.
Consult your local distributor
for information on when piing
before the trap should not be
insulated.
Observe all applicable public
•
and company codes and regu-
lations concerning steam and
condensate piping.