Bestobell Steam Total Trap 2 User Manual
Please read these instructions, Ideal installation, Start and initial warm-up
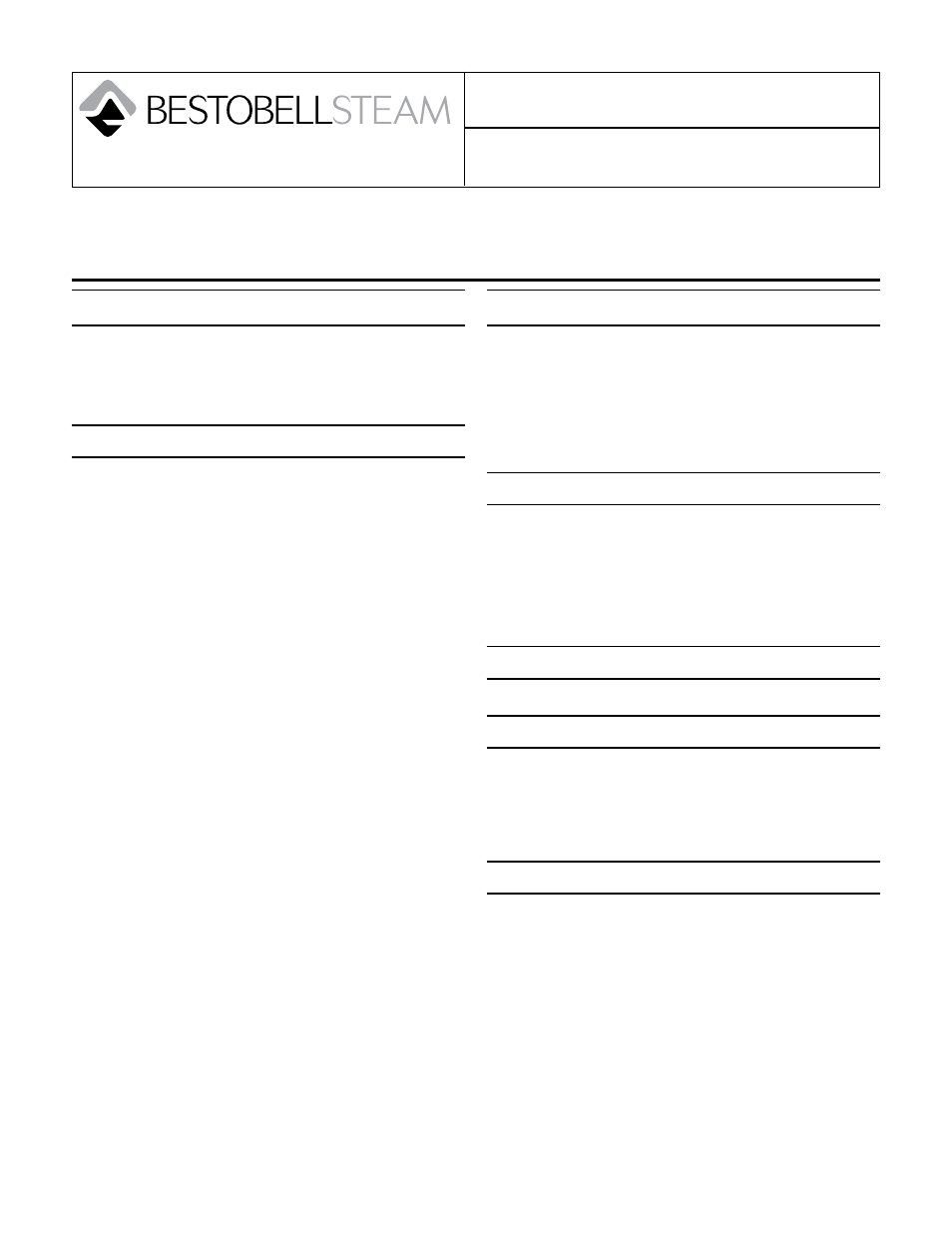
3170 Wasson Road • Cincinnati, OH 45209 USA
Phone 513-533-5600 • Fax 513-871-0105
[email protected] • www.bestobellsteamtraps.com
TT2/TT3 Series
Installation & Maintenance Instructions for
Bestobell Steam TT2/TT3 Series Total Trap
®
Stations
Warning: Bestobell Steam products must only be used, installed and repaired in accordance with these Installation & Maintenance Instructions.
Observe all applicable public and company codes and regulations. In the event of leakage or other malfunction, call a qualified service person;
continued operation may cause system failure or a general hazard. Prior to servicing equipment, disconnect, shut off, drain and/or bypass all pres-
surized fluids.
Please Read These Instructions
The Total Trap
®
2 & 3 Series will provide you with long, trou-
ble-free service if it is correctly installed and maintained. A
few minutes of your time spent reading these instructions
may save hours of trouble and downtime later.
Ideal Installation
1. To protect the trap from grit, scale, metal chips,
and other foreign matter, ALL pipelines and piping
components should be blown out and thoroughly
cleaned before the trap is installed.
2. In preparing welded connections, care should be
exercised to prevent debris, fluids or compound
from getting into pipe lines.
3. The flow arrow on the trap body must be pointed
in the direction of flow. Ideally, the trap should be
installed in the lowest horizontal line of downcomer
piping to provide for maximum drainage of conden-
sate and to obtain a faster response by the disc trap.
4. The trap should be installed horizontally with disc
trap cap on top. The outlet of the blowdown valve
on the bottom of the trap should be connected to
blowdown piping to adequately route high tempera-
ture/pressure steam away from personnel and other
equipment that could be damaged. The vent on the
back of the trap should similarly be oriented away
from personnel and other equipment that could be
damaged.
5. Piping should be the same material and sized ap-
propriately for the hub end connections. Inlet and
outlet piping should be the same size.
6. A full-ported shutoff valve upstream is recommend-
ed to allow isolation for servicing. A shutoff valve
downstream will protect against back flow from the
return line during servicing. Alternately, the isolation
valves built into the trap can be used to adequately
isolate the disc trap assembly for maintenance pur-
poses provided the trap is isolated upstream and/or
the system is in a cold iron state, i.e. shutdown.
7. The downcomer piping should be sloped to and
from the trap to ensure adequate flow and freeze
protection.
Start and Initial Warm-Up
1. Fully open the inlet and outlet isolation valves.
2. Fully close the freeblow/vent, strainer blowdown, and
bypass valves.
3. Slowly apply system pressure to steam trap and
bring system up to operating conditions per customer
usual start-up procedures.
Caution!
The strainer blowdown valve achieves maximum
sealing properties when heated up. A slight amount
of steam leak-by during start-up from the blowdown
valve may be noticed until the valve packing heats
enough, at which point leak-by should cease.
Maintenance
Warning!
Hot discharge from the trap may cause severe burns.
Shut off steam supply and make sure that the trap is
cool to the touch before conducting maintenance or
inspection.
Caution!
Do not remove the flush plug above the steam inlet hub
unless the system is shut-down, the trap is cool to the
touch, and the intent is to clean the disc trap assembly
through back flushing. If debris has not been allowed
to enter the steam system, cleaning of the disc trap
assembly and removal of the flush plug should not be
necessary.
1. The trap can be maintained without disturbing the
piping connections. Ensure that the trap is isolated -
upstream and downstream - before attempting
any maintenance involving disassembly of the disc
trap. ALLOW THE TRAP TO COOL BEFORE
DISASSEMBLY.