Sun Pumps PCC-BT-M2 User Manual
Page 9
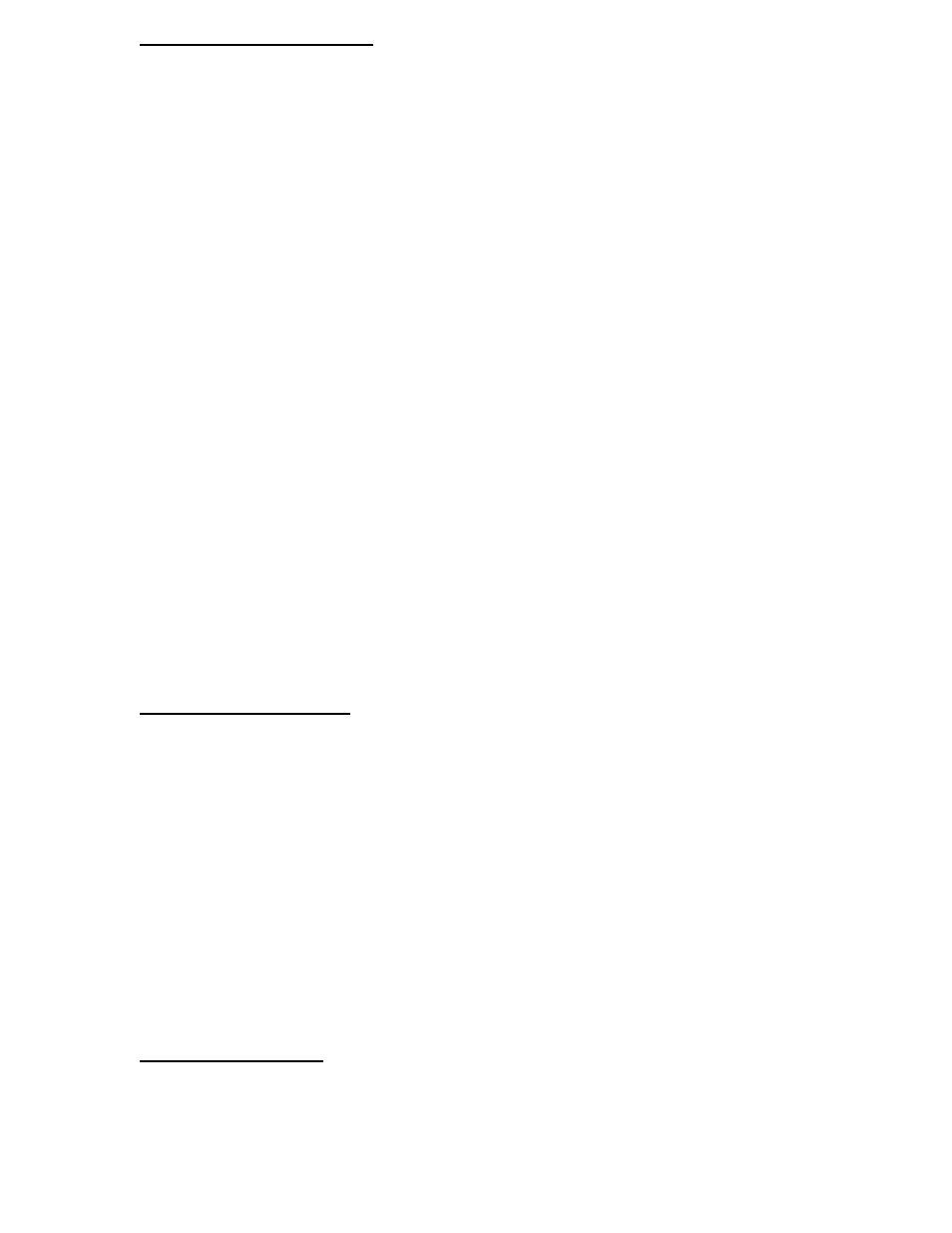
3.4
Controller Settings
The PCC series controllers have several settings (see figure 2). Most features include system configuration
adjustments, some of which are user selectable by an eight position DIP-switch located on the face of the
controller.
Switch 1 is the Remote Switch Logic 1. With this switch off (down), terminals “RS1” and “GND” must be
connected to turn the controller off. With this switch on (up), terminals “RS1” and “GND” must be
connected to turn the controller on. Never connect a float switch between “RS1” and “RS2” terminals.
Switch 2 is the Remote Switch Logic 2. With this switch off (down), terminals “RS2” and “GND” must be
connected to turn the controller off. With this switch on (up), terminals “RS2” and “GND” must be
connected to turn the controller on. Never connect a float switch between “RS1” and “RS2” terminals.
Switches 3, 4, 5 and 6 are current regulation settings. The controller will regulate current at 5, 7.5, 10 and
14 amps respectively depending on which one of the 4 dipswitches is on. One must be on for the controller
to operate but only one should be on at a time. In the case of multiple switches the lower current setting
will take precedence.
Switches 7 and 8 are used for a turn-on timer for remote switch 1. With both off, there will be no timer and
the pump will turn on immediately. With only dip switch 7 on, the timer will be 3 minutes from the time
the “RS1” and “GND” connect/disconnect until the pump turns on. With only dip switch 8 on, the timer
will be 7 minutes from the time the “RS1” and “GND” connect/disconnect until the pump turns on. With
dip switches 7 & 8 on, the timer will be 10 minutes from the time the “RS1” and “GND”
connect/disconnect until the pump turns on.
Switch 9 is used to control the user interface. When switch 9 is down, the LCD will display various
screens conveying pump and controller operating parameters. The display will cycle through each screen
at a predetermined rate. For troubleshooting and some setup features certain screens are desired. By
turning dip switch number 9 on, the display will stop cycling and the current screen will stay on the display.
Switch 10 is used to disable the Maximum Power Point Tracking feature for testing purposes. All other
functionality of the controller remains unchanged including the current and voltage regulation which will
continue to function normally. The low power setting will be ignored but minimum input voltage and
current will still be functional.
3.5 Auxiliary Control
The auxiliary control circuits are configured and controlled with the “Dip Switches”, “LP Adj.”, “Output
Voltage Adjust” and the “RS1”, “RS2” and “GND” terminals. (See Figure 2)
These circuits offer expanded capability and are described here. The remote switch controls are for float
switches (storage tank level), pressure switches or a remote system “ON/OFF” toggle switch.
The output voltage adjustment is for regulating the output voltage to the pump and is used to limit the
maximum flow rate of the system.
There are also the low power shut down and current regulation circuits. See each corresponding detailed
description below.
NOTE: Use only “Shielded Wire” to run from the remote switch to the controller. The shielding
must be grounded to the controller side only. This can be done on the terminal labeled “GND” or on
the ground lug at the bottom of the controller. If shielded wire is not used, induced voltages from
lightning storms or two-way radio transmissions could damage the controller.
Current Regulation
The PCC-BT series controller is designed to run at the maximum power possible for the system. This may
be the maximum power point of the solar panels, the maximum current of the pump motor or it may be at
the maximum output voltage of the controller. When enough power is available to run the pump at the
maximum current, the current regulation will limit the pump to maximum current set by the dip switches.
During this regulation the “Over Current” LED on the controller will flash. This is normal operation.