Section 3 general, Section 4 design, Electrical – MK Products MK 2000A User Manual
Page 10
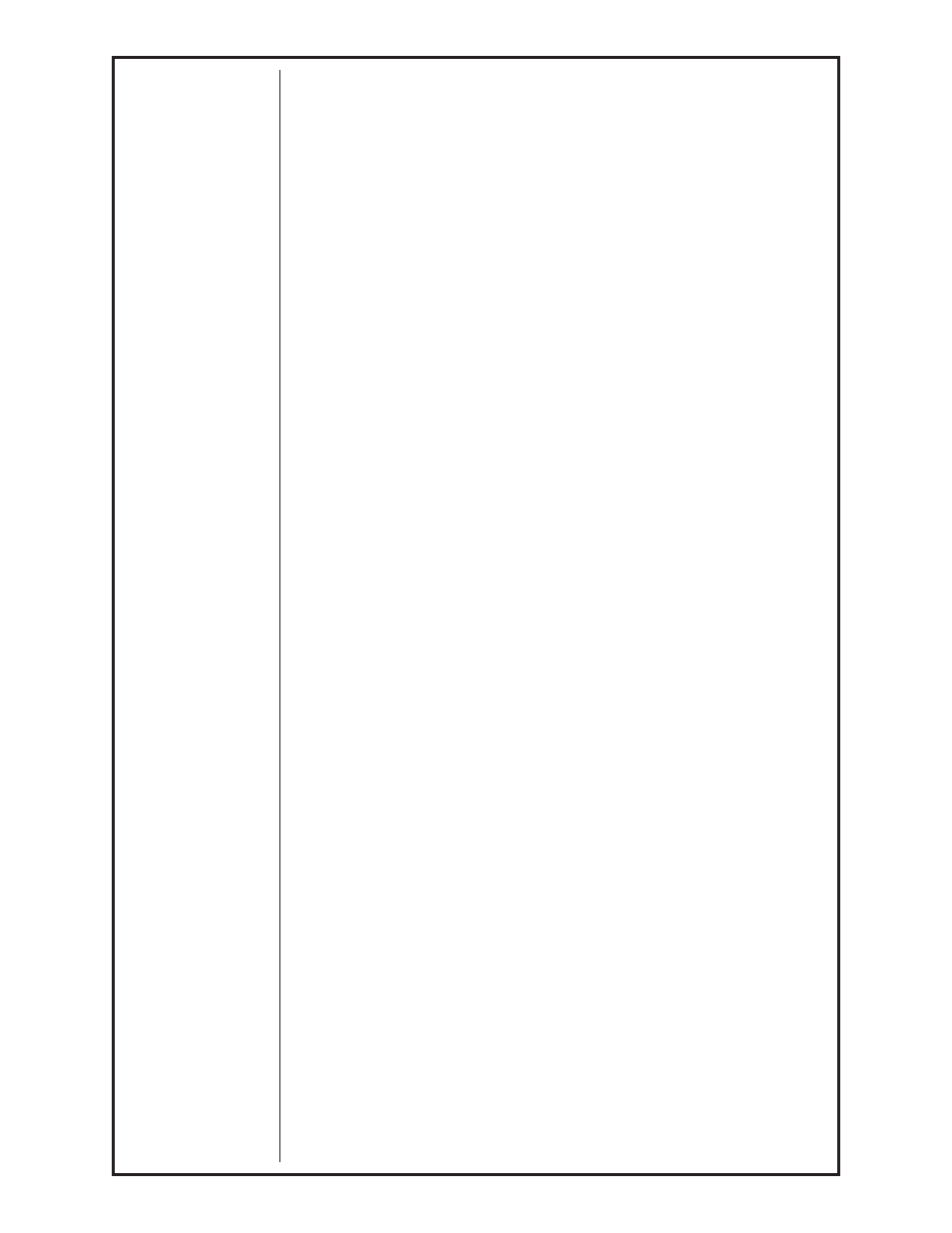
MK 2000A - Owner's Manual - Page 10
Section 3 GENERAL
The MK2000A Electronic Pulsed Welding Power Supply is designed to
provide precision controlled, highly efficient welding power in a compact,
extremely reliable form.
The demands of modern fabrication techniques, with well- designed parts
accurately fitted together, require exceptionally well controlled welding wire
feed and welding power control. The MK Cobramatic Wire Feed Systems,
long known for precision wire feeding for critical applications are now
matched with a precision power supply. The combination is exceptionally
well suited for fixtured or robotic welding, although the exceptionally stable
characteristics also make hand welding much easier.
The welding engineer will appreciate the flexibility to utilize constant voltage,
constant current, pulsed welding and unique combinations of all in a single
compact, efficient unit.
Section 4 DESIGN
Electrical
The MK2000A is a transistorized inverter power supply intended for use on
three phase 208 to 277 volt and 380 to 460 volt, 4 wire wye (with neutral),
50/60 Hertz supply circuits. (See page 24 for more details) The unit will also
operate on single phase 208 to 277 volt circuits, although the reduced power
factor may require limiting the duty cycle based on the volt ampere capacity
of the primary wiring.
The input power is converted to direct current and a switching inverter utilized
to generate alternating current at 20,000 hertz.
A compact, low-loss transformer steps the high voltage down to the welding
voltage range where it is rectified and filtered for output.
The inverter is controlled by a digital/analog control system which permits an
exceptional range of voltage, current and waveform controls.
For constant voltage (CV) operation, the output voltage is sensed and
compared with a digital reference. The inverter switch is controlled on a cycle
by cycle basis to hold the output at the reference value over the entire load
range. To provide spatter free welding conditions, slope may be added so
that the output voltage decreases with increasing current. Any slope from 0
volts per 100 amperes to vertical (constant current) may be set.
For constant current (CC) operation, the output current is sensed and
compared with a digital reference. The inverter switch is controlled on a
cycle by cycle basis to hold the output at the reference value over the entire
load range.
Pulsed operation is provided whereby the background voltage set by the
background level control is increased periodically. These pulses may
increase the output by any amount up to 100% of the power supply capacity.
Pulse rates may be any frequency from 20 pulses per second to 2000 pulses
per second. This, of course, includes the common pulse frequencies of 60
and 120 pulses per second available from thyristor supplies operated at line
frequency. Pulse widths may be any value from 0 to 100% of the pulse
period. In addition, the pulse shape may be controlled to provide a gradual
rise and fall (symmetrical), when an external control computer is used.
An exceptional capability is provided by the MK2000A through the use of
the Pulse Level and Pulse Slope controls in conjunction with the Background
Level and Background Slope. These two sets of controls function identically
cept that the pulse modulation is only added to the Background Control.