MK Products MiniMicro Orbital Weldhead User Manual
Page 12
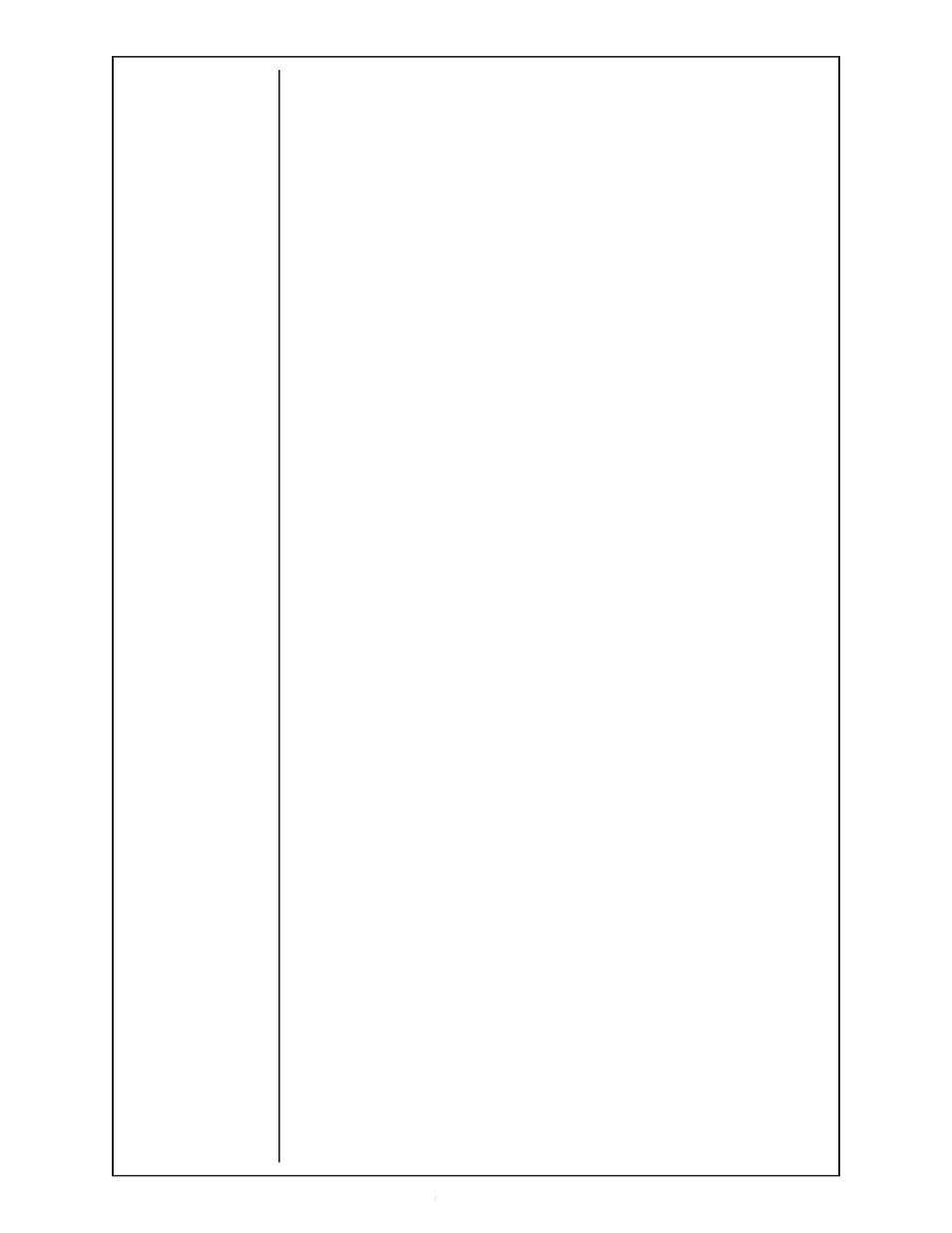
Mini Micro
®
Owner’s Manual - Page 6
®
®
All tungsten supplied by MK Products, Inc. is prepared using the latest
manufacturing techniques in order to meet the geometry specifi cations as
described above.
Installing the Tungsten Electrode
The electrode is mounted in the rotor and held in place with a setscrew.
To insert the electrode, jog the rotor around until both the tungsten hole and
the tungsten set screw are visible in the top of the rotor. Loosen the tungsten
setscrew. Insert a properly prepared electrode from the top of the rotor and
tighten the setscrew. Be sure to set the appropriate arc gap prior to welding.
Setting the Arc Gap
1. Place the part to be welded on the lower Collets with the clamps in the
upright open position.
2. Place the appropriate thickness gauge between the tungsten electrode
and the part to be welded so that the tungsten electrode is at the correct
gap.
Be certain the thickness gauge is perpendicular to the tungsten
electrode.
3. Tighten the setscrew to secure the tungsten electrode in the rotor.
Recommended Arc Gap
The proper arc gap is an important part of the proper use of your orbital
welding equipment. Improper arc gap can cause arc strikes to occur to your
Collets or to the Side Plate Clamp.
Be sure the arc gap is as short as possible, consistent with the process and
weld current level, but not so short as to ‘crash’ or touch the weld being
made.
If no arc gap is known when designing a weld procedure a good rule-of-
thumb is as follows:
Arc Gap = (Wall Thickness x 0.5) + .010”
CAUTION
Do not over-tighten the tungsten set screw. Over-tightening the setscrew can
crack and splinter the tungsten causing errant starts and arc wander.
Be sure that the tungsten does not extend into the rotor teeth and that both
setscrews are fl ush with the rotors surface.
Any length of tungsten that is protruding out the back of the rotor will jam with
the meshing gears inside the weldhead. This will push the tungsten into the
weld being made and inevitably cause an ARC FAULT.
If the weldhead becomes jammed, a “Motor Stall” will result. Usually, some
foreign matter, or a piece of tungsten electrode has fallen within the gear
mechanism of the weldhead, hindering the rotation of the gears.
Clearing a Jammed Weldhead
In order to clear the jam, turn the weldhead upside-down and vigorously
shake the weldhead.
Before turning the weldhead right side up, attempt to locate the foreign
object. If the jam cannot be cleared in this manner, the weldhead must be
returned to MK for disassembly to have the objects removed.
Section
A Cont.