MK Products MiniMicro Orbital Weldhead User Manual
Page 11
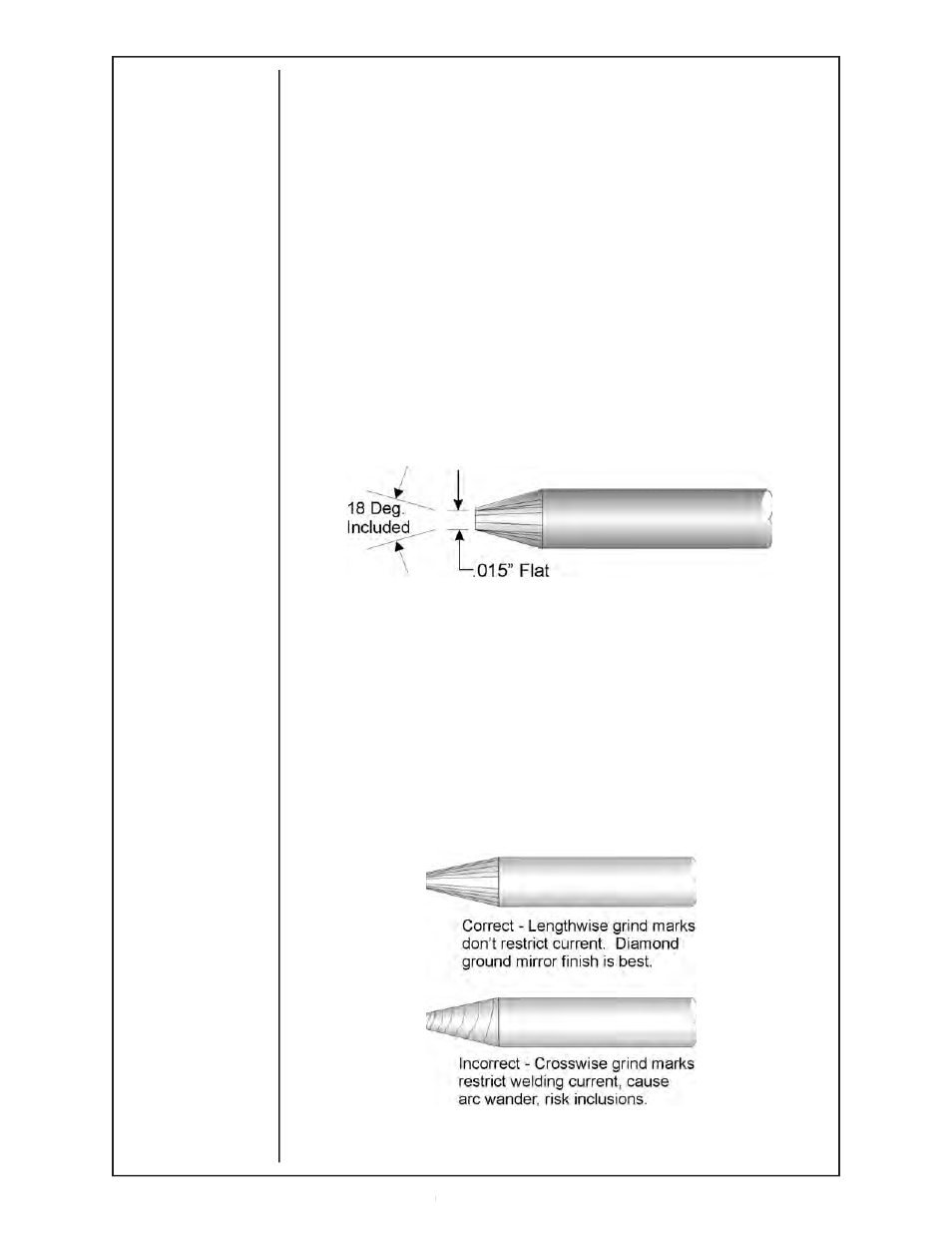
Mini Micro
®
Owner’s Manual - Page 5
®
®
5. Repeat the process for the opposite side of the weldhead.
6. Once completed, check the alignment of the parts. A misalignment may
be corrected by moving the left or right plunger in or out by a fraction of
a turn and then repeating the opposite action to the opposing plunger on
the same Collet.
Tungsten Electrode
The recommended tungsten type to be used in the MiniMicro™ and the MK
orbital welding system is 2% Ceriated, 1/16 inch diameter.
Appendix C gives the MK part numbers for pre-ground tungsten electrodes
required for a specifi ed tube diameter. These lengths of tungsten are long
enough to allow the setscrew to securely hold the tungsten while maintaining
a relatively close arc gap, and keep the tungsten from sticking out the back of
the rotor while using a large arc gap.
Tungsten Geometry
The recommended grind angle and shape for tungsten is 18° included angle
and a .015 inch fl at (Figure 2). Regardless of the electrode tip geometry
selected; it is important that consistent electrode geometry be used once a
welding procedure is established.
Figure 2
Changes in electrode geometry can signifi cantly infl uence the weld bead
shape and size; therefore, electrode tip confi guration is a welding variable
that should be defi ned during procedure development.
Tungsten Preparation
Tungsten electrodes should be properly ground for consistent results. If
the electrode is to be hand ground, use a dedicated diamond wheel. The
grinding marks should be perpendicular to the tungsten electrode or poor arc
starts, arc wander and inclusions may occur (See Figure 3). No other parts
should be ground with these wheels, since contamination of the electrode
could result and create problems with arc initiation, arc wander during the
weld and tungsten inclusions in the weld bead.
Figure 3
Section
A Cont.